Atotech on Challenges and Opportunities in PCB Manufacturing
September 4, 2018 | Stephen Las Marias, I-Connect007Estimated reading time: 10 minutes
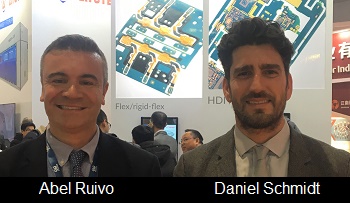
Abel Ruivo, Atotech Deputy Business Director of Electronics for Greater China, and Daniel Schmidt, head of Global Marketing for Electronics at Atotech Group, spoke with I-Connect007 about the various challenges of PCB manufacturing in China, as well as about the opportunities in the sector.
Stephen Las Marias: Abel, tell us more about Atotech and your role in the company.
Abel Ruivo: I’ve been working in this field for 30 years and have been in China for almost 20 of those, overseeing the sales and service aspect of the business. Our team here is dedicated to opening doors, supervising trends and providing technical solutions. We support all market segments, supplying products for every step of the wet chemistry production process in PCB and semiconductor manufacturing. This includes everything from multilayer bonding, desmear and PTH to plating, surface treatment technology and selective finishing for PCB. We also provide solutions for wafer metallization, chip interconnects and a comprehensive range of advanced packaging products. This includes dual damascene, re-distribution layers (RDL) and pillar plating as well as pad- and under-bump metallization, through via filling, through-silicon via filling and side-plating for semiconductors. Atotech provides the most advanced technical solutions for surface finishing industries worldwide by combining cutting edge chemistry and world-class technology. We are committed to being innovative, adapting to meet the needs of our customers as well as those of our investors and employees worldwide.
Las Marias: What new trends are you currently seeing in the PCB manufacturing industry?
Ruivo: 2018 has been a year of increased capability expansion. Many emerging companies are looking to expand production, and in doing so they are creating and using new applications and technologies. Many are making the transition from double-sided PCBs to flex or HDI. Some companies are branching out to produce high-end technologies using modified semi-additive processes (mSAP), something that became very popular last year with OEMs alongside flex and rigid-flex circuits. Within the automotive industry, electronics are becoming an increasingly integral part of the production process. This is something that we’ve been seeing in China, too.
Las Marias: What pain points have you identified amongst your customers?
Ruivo: The challenge for our customers is to grow fast whilst contending with competitors in terms of cost to increase market share. In this respect, China is very competitive. We want to support the development and production plans of our customers, and we know that it’s a balancing game: What can we deliver in terms of technology and reliability whilst ensuring our customers’ overall costs remain conducive to coming up with sustainable solutions in a competitive environment?
Las Marias: Tell us about the latest technology you’ve introduced to the market.
Ruivo: Atotech has several products that we began introducing to customers two years ago. For example, we developed new products (based on mSAP technology) to comply with latest fine line and space requirements especially in mobile applications. Another innovation is our MultiPlate, a unique high-tech plating tool which meets the challenges of wafer- and panel-level packaging.
Las Marias: So MultiPlate is intended to be used in the semiconductor industry. Can it also be used for PCB manufacturing?
Ruivo: Not directly, but there are some trend requirements in panel-level packaging that this technology arguably meets. The unique thing about MultiPlate is that it allows you to plate from both sides. The technique is unique and has excellent panel-to-panel distribution, a highly sought-after quality in the market.
With the same end in mind, we also started designing new systems technology in Germany for PCB production in China. This technology is competitive cost-wise and has proven to be outstanding in terms of quality performance. This state-of-the-art product line is called Polygon and is made in China. It is revolutionizing surface treatment as well as desmear and PTH processes, and we plan to offer this solution also for PCB final finishing.
Las Marias: What makes these latest products unique?
Ruivo: We started engaging with customers at a much earlier stage than usual to establish ahead of time what products they plan to produce and what their future needs will be. This has allowed us to develop at a faster rate to meet their demands before these demands have even really materialized. The two products I just mentioned, MultiPlate and Polygon, are going in that direction.
Las Marias: There must be an increasing need today to collaborate closely with your customers…
Ruivo: That’s correct. We have to engage as early as possible, taking our lead to interact and then act on information we receive from potential customers as well as from OEMs, institutes and associations.
Las Marias: Daniel, tell us more about the market here in China and how it has changed in the past few years. What are the opportunities and challenges?
Daniel Schmidt: Let me start by briefly commenting on the global market situation. Development last year was relatively good following 2016, in which there was a lot less expansion happening. The PCB industry, bolstered by the expanding HDI and flex circuit market, saw an increase of almost 9%. There was a growth of about 16% in HDI production, while the figure for flex circuits was around 15%. The main growth contributor within the flex circuit market was in rigid-flex circuit products, a hot topic still right now. In the space of just one year, the rigid-flex segment grew by over 51%. Why is that? There's a much more widespread use of flexible and rigid-flexible circuits in all kinds of end markets now, not only in the automotive field but also in mobile, medical and consumer electronics production. We see a lot of wearable technology and small gadgets coming to the market that use flex and rigid-flex circuits to ensure they can be bent into specific required shapes. So that’s one factor that influenced the market; high-end smartphones is another. The latest generation smartphones are also making high use of more flex and rigid-flex circuits. Last year, for instance, one smartphone OEM introduced new phones using OLED displays, which really boosted the rigid-flex segment. This year several smartphone OEMs are using similar technologies. These are developments that we’re very interested in. We’re consistently working toward enabling more suppliers to benefit from this growth, offering comprehensive production solutions that allow then to produce advanced HDI, flexible and rigid-flex printed circuit boards.
We have seen that the PCB market is also rapidly developing in China. There are a lot of new PCB shops that have opened up with the aim of continuing expansion. We believe China will continue to increase its overall production share, with local manufacturers exploring the newest technologies. The Chinese market has also benefited from investments by Korean and Taiwanese companies that are looking to increase their exposure in the Chinese markets. The Chinese manufacturer base is currently working towards gaining major shares in the market where technologies such as mSAP, flex and rigid-flex circuits—and now also multilayer flex—are concerned.
Las Marias: What is Atotech’s role in all this?
Schmidt: Fortunately, Atotech has a really strong position in the market. As a supplier, we have a reputation for providing solutions that make the most of the very newest technologies to address the latest industry requirements. We see ourselves as a strategic partner for our customers; we’re regularly called upon to help them in both the early stages of research and development and the later prototyping phases to fulfill the requirements of their customers, the OEMs. As Abel mentioned, the progress China is making in mSAP technology is huge. The first discussions started about two and a half years ago. At that time, it was a fairly new idea to use this technology for the main circuit board of a smartphone. Atotech has always been a turnkey solution provider for the industry, playing a major role by providing the technology needed in this specific moment of market development. The same is true of the adoption of rigid-flex printed circuit boards in smartphones, especially for applications such as displays, batteries and dual cameras. We are currently working together with many top manufacturers on new technologies and products that are slated to appear in the coming two years.
Las Marias: The semiconductor industry is one of your markets here, an area in which China is investing heavily. What kind of an impact is that having on Atotech?
Schmidt: China’s market opens a lot of doors for Atotech and our semiconductor and advanced packaging products. The Chinese government is offering benefits to companies that are increasing their operations in these particular market segments, and as we have established, these are areas in which Atotech is doing well. We work closely together with several major semiconductor companies, offering new technologies and helping them deal with the market demands.
We mentioned MultiPlate earlier; this product is great not only for the semiconductor but also for the panel level packaging industry, which has come about as a result of the semiconductor packaging and IC substrate markets merging. Our MultiPlate product meets multiple needs. It can be used by semiconductor companies to manufacturer wafers, but also by IC substrate companies that are looking at small- to medium-sized panels to produce the next generation of substrates.
Las Marias: You mention the merging of semiconductor and IC substrate field. What is driving that trend?
Schmidt: It ultimately boils down to miniaturization and cost. Everything is becoming smaller and at the same time more cost-effective solutions are needed. This requires substantial changes to manufacturing. For example, when taking cost of ownership into consideration, substrate manufacturers need our help finding new ways to increase the holding capacity of pre-existing formats.
Las Marias: One of the trends right now is smarter manufacturing, also known as Industry 4.0. What is Atotech's strategy for helping its customers on this front?
Ruivo: This is something we’re giving a great deal of consideration to as we’re aware that there are more and more companies looking to expand in this direction. We’re already exchanging our skills, capacities and experience with those we work with to help them do so. We have been collecting data and statistics for some time now, which puts us in the position of being able to share information with our customers on how to automate production, but more importantly how to assure high reliability and yield.
Schmidt: Our horizontal production lines are great when it comes to meeting reliability demands in PCB manufacturing. Today, Atotech technology is already compatible with external automation systems, and can be integrated rather easily. Fab automation systems and green manufacturing are high-priority for Atotech; we are already collaborating with several leading companies in this field. There was a great article just published in the March issue of PCB007 Magazine on these developments, and there’s more on the way.
Las Marias: Daniel, what is your outlook for Atotech this year?
Schmidt: We expect a stronger second half of the year for all end markets, whether these are communications, consumer electronics, computing or the automotive industry; all markets are showing positive unit sales and growth rates. OEMs are working on the next major products which means lots of new and exciting things are in the pipeline. We also expect the production of PCBs, whether these are multilayer, HDI, flex or rigid-flex, as well as IC substrates to be an integral factor in market developments. Atotech is well-established in all these markets, serving manufacturers of all these segments. So as we see it, the prognosis for Atotech for the remainder of 2018 is a positive one, with increased rates of expansion as more companies adopt mSAP technology and support the current trends in flex and rigid-flex manufacturing.
Las Marias: I’ve heard that mSAP technology can be used for 5G. Can you tell us something about that?
Schmidt: 5G is on its way, and it’s all about high-frequency applications. Atotech is already very active in working with some of our customers, developing processes to meet the very stringent requirements for high-frequency applications.
Ruivo: The market is investing in 5G, and China has revealed that by the end of the year, it will already be used in some of its cities. We’re working closely with our customers and OEMs to find solutions, and have already started to develop products that work with 5G. These will be developed further in the coming years, and will without a doubt increase market growth in the country.
Las Marias: Great! Thank you both for sharing these developments with us.
Schmidt: Thank you for having us.
Las Marias: Thank you for the interview, Daniel and Abel.
Both: Likewise. Thank you.
Suggested Items
Zhen Ding Promotes Digital Transformation and Embraces AI Business Opportunities
06/06/2025 | Zhen Ding TechnologyOn May 27, 2025, General Manager Chen-Fu Chien of Zhen Ding Technology Group was invited to attend the "2025 Two Thousand Forum" held by The CommonWealth Magazine.
Leidos Using Quantum Technology to Thwart GPS Jamming
06/05/2025 | PRNewswireSusceptibility to jamming is a significant military vulnerability of the Global Positioning System (GPS) signal. Through a Defense Innovation Unit contract, Leidos is developing an alternative navigation technology that measures variations in the Earth's magnetic field and harnesses the quantum properties of nitrogen in diamonds.
Growing Demand for Mid-Size Displays Opens New Opportunities for FMM-Free OLED Technologies
06/05/2025 | TrendForceTrendForce’s latest report on the display industry reveals that OLED technology—valued for its self-emissive structure, high contrast ratio, and lightweight design—continues to expand its market presence, primarily in small-size applications such as smartphones.
Orbel Corporation Integrates Schmoll Direct Imaging
06/04/2025 | Schmoll AmericaOrbel Corporation in Easton, PA, proudly becomes the first PCM facility in the U.S. equipped with Schmoll’s MDI Direct Imaging system. This installation empowers Orbel to support customers with greater precision and quality.
BAE Systems Unveils Comprehensive Line of M-Code GPS Receivers at Joint Navigation Conference
06/04/2025 | PRNewswireBAE Systems unveiled a diverse line of M-Code Global Positioning System (GPS) receiver solutions at the Joint Navigation Conference in Cincinnati this week, rounding out an extensive line of products that ensure U.S. warfighters have the most dependable GPS systems available across sea, land, and air.