-
- News
- Books
Featured Books
- pcb007 Magazine
Latest Issues
Current IssueInventing the Future with SEL
Two years after launching its state-of-the-art PCB facility, SEL shares lessons in vision, execution, and innovation, plus insights from industry icons and technology leaders shaping the future of PCB fabrication.
Sales: From Pitch to PO
From the first cold call to finally receiving that first purchase order, the July PCB007 Magazine breaks down some critical parts of the sales stack. To up your sales game, read on!
The Hole Truth: Via Integrity in an HDI World
From the drilled hole to registration across multiple sequential lamination cycles, to the quality of your copper plating, via reliability in an HDI world is becoming an ever-greater challenge. This month we look at “The Hole Truth,” from creating the “perfect” via to how you can assure via quality and reliability, the first time, every time.
- Articles
- Columns
- Links
- Media kit
||| MENU - pcb007 Magazine
Estimated reading time: 3 minutes
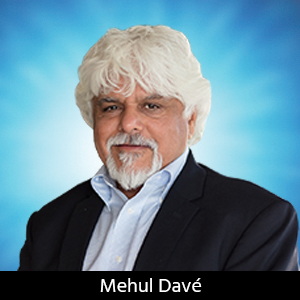
‘Can Do’ in CAM Outsourcing: Improving Quality in CAM Engineering
In this series, I will address six ways in which a company can significantly benefit from outsourcing their front-end CAM work:
- On-demand capacity
- Improving automation
- Fast turn-around
- Reducing costs
- Improving quality
- Building redundancy in critical areas
This column will focus on the fifth benefit: improving quality.
Improving Quality
One of the hallmarks of achieving and maintaining high quality is having a controlled process. However, the main challenge of attaining a repeatable process is that different individuals tool complex jobs—especially when it is possible to complete the same job in multiple ways. Many companies have a tremendous amount of tribal knowledge in the heads of a few key people who execute tooling jobs using their own unique methods. This occurrence often leads to huge problems when the individuals leave the company because their tribal knowledge walks out the door with them.
The key to achieving repeatable processes is using automation and developing systems that allow tribal knowledge to be captured using a formal approach. For example, in our facility, the goal is to fully automate the entire tooling process. Moreover, focusing on improving quality can affect other critical areas of the business. Better systems result in faster turn-around times and reduced costs. One of William Edwards Deming’s 14 points for management states, “Improve constantly and forever the system of production and service to improve quality and productivity, and thus constantly decrease costs.”
Therefore, it is essential to work with an outsourcing partner that solves problems with a systems-based approach. It can be easy to throw bodies and resources at a problem and hope it will be solved—especially if you’re based in a low-cost region. However, this usually leads to more issues. When it comes to tooling and CAM, the solution is to develop scripts and automation. Maintaining automation over time is critical. Some people don’t create automation in the first place, and a majority of others don’t keep it updated due to a lack of commitment to quality. In an environment where scarce resources get pulled into fighting fires and keeping up “hot jobs,” there isn’t enough time in the day to devote to systems and automation.
Partnering with the right outsourcing partner can help. Systems and automation can be developed and used by the outsourcer and have a significant impact on your workforce. Plan to use the same systems and automation for your engineers. Entering into a partnership where the outsourcing partner becomes an extension of your engineering team is extremely beneficial. As they work on new jobs alongside your employees, they should keep a finger on the pulse of your changing requirements and adjust the systems and automation on a regular basis. By doing so, you can avoid the systems and automation becoming outdated, which can lead to people returning to using tribal knowledge and manual processes.
Another tool from William Edwards Deming is the Deming Cycle—a four-step management method for continuous quality improvement of processes and products. It’s referred to as the plan-do-study-act (PDSA) cycle. The PDSA cycle should be employed when undergoing a systems/automation quality improvement program. The steps are as follows:
- Plan: Assess current and future states and identify alternative solutions for how to close the gaps
- Do: Try or test the solutions (sometimes at a pilot level)
- Study: Check to see if the tested solutions accomplished the objective
- Act: Request corrective actions for significant differences between the actual and planned results, and analyze the differences to determine the causes
- Repeat the cycle
Conclusion
In summary, using an outsourcing partner can help improve quality by allowing you to:
- Implement repeatable and consistent processes
- Reduce or eliminate reliance on individuals with tribal knowledge
- Streamline and systematize your entire front-end process
- Reduce shop floor rejects through improved front-end quality, which results in lower costs and higher margins
- Easily add and train new employees with better processes and systems
- Capture more market share from your competitors
- Free critical engineering capacities to help generate more technical sales and have more customer interactions
- Grow your business and have scalable front-end resources to fulfill your changing requirements
Mehul J. Davé is CEO of Entelechy Global Inc.
More Columns from The Big Picture
The Big Picture: Our Big ‘Why’ in the Age of AIThe Big Picture: The Shift From China to Southeast Asia
The Big Picture: Quality Front-end Engineering as a Core Differentiator
The Big Picture: What Two Hot Wars Could Mean for the Electronics Supply Chain
The Big Picture: Essential Engineering—The Intersection of Humans and Machines
The Big Picture: How Values Drive Company Culture and Create Trust
The Big Picture: A New Globalization
The Big Picture: The Virtual Via Drum