Building a Better Board: It Always Comes Back to Communication
September 24, 2018 | I-Connect007 Editorial TeamEstimated reading time: 4 minutes
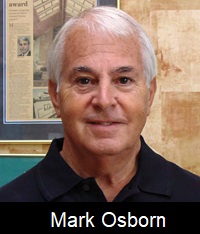
For our experts meeting on this month’s theme of reliability, we reached out to Colonial Circuits and asked them to participate in a conference call with our I-Connect007 editorial team consisting of Dan Feinberg, Andy Shaughnessy, Patty Goldman, and Happy Holden. Joining the call from Colonial Circuits was Mark Osborn, president and CEO, Kevin Knapp, quality manager, and Rodney Krick, manufacturing manager.
Dan Feinberg: Gentlemen, we really appreciate your participation. Mark, you and I have talked about the optimism of the industry with things that are going within it. There seems to be more optimism and general optimism in business that I’ve seen perhaps since the late ‘60s, early ‘70s.
Mark Osborn: I agree. We saw a slight dip in business last year, mainly because a key customer’s program ended. The new design switched from rigid to flex, and due to the quantity needed, the customer required the flex to be supplied on reels, something we are unable to do. Fortunately, today’s market is one where new opportunities are presenting themselves daily.
Feinberg: That’s great to hear. You never like to turn work away.
Patty Goldman: Does that mean you can kind of pick and choose your customers now?
Osborn: We’re getting quite a mix from the same customer. It’s the technology that’s taking so much time to fabricate.
Feinberg: Mark, I know you have had some issues with regard to reliability and materials, as well as counterfeit components. So, my question for you is, what reliability trends are you seeing regarding requirements from customers, especially over the last few years?
Kevin Knapp: I’m in the quality world here. We’re seeing a lot of dimensions going out four and five decimal places, where three was about it in the past. It’s getting to be a lot more particular. We’re also seeing parts from several years ago that have been in stock for two to three years, and then I’ll scrutinize them and find that what was acceptable then may or may not be today. I think it’s changed that much. And the other thing we are seeing is more customers sending parts out for third-party testing, just like you would for space flight prior to being accepted.
Osborn: Most of that arises when they’ve had a manufacturing problem, not necessarily with our boards, but with one of the other suppliers.
Feinberg: I think that going from two decimal places to five decimal places, or three to five, that’s huge. That’s a quantum jump in specs.
Osborn: It is. But as you know, the trend is to build smaller, and it must meet certain criteria, and with the new components, features have really shrunk. But we’re here taking on huge challenges every day knowing that next week a whole new set of challenges will materialize.
Feinberg: I know reliability trends relate to specs on what customers are demanding of you as a fabricator, but what are you seeing as far as raw material challenges, and what are you then passing on to your suppliers of raw materials as far as demands?
Osborn: The answer to that question is the ability to get laminate. In many cases we can, and I’m sure you have heard of the horror stories with Rogers. When they’re out to 30, 40, or 50 days on delivery and you’re in a quick-turn market, that makes it extremely difficult to compete. We just tried a new material at a customer’s suggestion called Astra, sold here in the states by Isola. But as we’re learning, it has its own set of issues that we were totally unaware of because we had never used this laminate before.
As you know, Dan, the grain direction of the material plays a role in potential warpage. Colonial, for the past five years, has only purchased material with the grain in the long dimension. This time period has allowed us to build an extensive library of data on dimensional stability surrounding our standard laminates. Unbeknownst to us, the Astra is only available with the grain in the short direction, meaning we were unable to predict the outcome! After two or three unsuccessful fabrication attempts, we finally nailed it.
Even the ability to obtain regular material has proven difficult, particularily with flight work. Polyimide-aramid-NT is a popular laminate used for this application, but the 4-5 week lead time on delivery is not appealing to our better customers.
Feinberg: Where is the Astra material made?
Osborn: China.
Feinberg: Any indication that, with the demand going up, there might be some made in the U.S. again at some point?
Osborn: I hope that some of that comes back, but at this moment we’re not hearing anything from our supplier.
To read the full version of this article which originally appeared in the August 2018 issue of PCB007 Magazine, click here.
Testimonial
"Our marketing partnership with I-Connect007 is already delivering. Just a day after our press release went live, we received a direct inquiry about our updated products!"
Rachael Temple - AlltematedSuggested Items
The Knowledge Base: Cultivating Your Brand in the Age of Connection
08/19/2025 | Mike Konrad -- Column: The Knowledge BaseAudiences have evolved in how they consume information, form opinions, and make purchasing decisions. While marketing still relies on tried-and-true methods—get your name and message in front of your audience—you must also cultivate connection, credibility, and community. Your customers, particularly the younger generation of engineers, buyers, and program managers, want to discover value on their terms.
Technica Demo Days Event Proves to Be Beneficial to Customers
08/18/2025 | Technica USATechnica USA’s Demo Days Event, took place August 13–14 at the company’s Demo Center in San Jose, California. The event featured live demonstrations and presentations from key supply partners ESSEMTEC, INOVAXE, and PARMI showcasing the latest innovations in SMT manufacturing and automation technology.
Insulectro and Electroninks Sign North American Distribution Agreement
08/12/2025 | InsulectroElectroninks, a leader in metal organic decomposition (MOD) inks for additive manufacturing and advanced semiconductor packaging, today announced a strategic collaboration and distribution partnership with Insulectro, a premier distributor of materials used in printed electronics and advanced interconnect manufacturing.
It’s Only Common Sense: Stop Chasing New Customers and Start Keeping the Ones You Have
08/11/2025 | Dan Beaulieu -- Column: It's Only Common SenseCustomer retention is not glamorous. It doesn’t have a flashy ad campaign, it’s not going viral on social media, and nobody’s handing out “Best in Retention” awards at trade shows. However, if you’re running a proper business, not a popularity contest, then customer retention is where you make your money. However, too many companies treat customer retention as an afterthought.
Automated Production Equipment and Manncorp Announce Strategic Partnership to Expand SMT Solutions for U.S. Electronics Manufacturers
08/06/2025 | Automated Production EquipmentAutomated Production Equipment (APE), a trusted supplier of high-performance soldering and rework systems, proudly announces a strategic partnership with Manncorp, a leading provider of Surface Mount Technology (SMT) production equipment. This collaboration brings together two industry leaders to deliver expanded, end-to-end SMT solutions to electronics manufacturers across North America.