IoT: Driving Change in Manufacturing
October 15, 2018 | Stephen Las Marias, I-Connect007Estimated reading time: 5 minutes
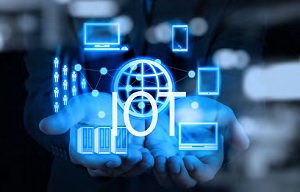
In our new manufacturing environment where trends such as data, robotics and artificial intelligence (AI) are proliferating, there are numerous strategies and tactics—predictive analytics, new OEM/supplier collaborative innovation models, technology platforms that support real-time business intelligence, and resilient and transparent supply chains that create virtual, vertically integrated manufacturing networks—that global manufacturing companies can deploy to capitalize on new market opportunities and stay ahead of their competition.
Enabling these strategies are key transformative technologies such as big data, analytics, and the Internet of Things (IoT). There are two categories for IoT: consumer and industrial. In the consumer space, imagine yourself arriving home from work. As you reach the curb in front of your home, your car will send a signal to your garage door to open. As you enter your home, your network will detect your presence and immediately turn on specific appliances, such as lights, the TV or stereo, air-conditioning unit, or whatever it has been programmed to do. As you sit down to relax, you eye your tablet resting nearby, and thinking about the workout you did earlier that day, you transfer the data collected by your smart watch to have a full view of overall impact of that workout on your health statistics. That’s just a simple example of how the consumer IoT can function.
The industrial IoT, on the other hand, describes an integrated system of systems where sensors and actuators provide specific data such as measurements, timing, and equipment status, to name a few, all connected and visible throughout the enterprise. This is where the convergence of operations technology (OT) in the factory floor with information technology (IT) in the enterprise happens, all working together towards a single purpose—a more-efficient, profitable and successful manufacturing operation. With industrial IoT, companies will be able to view real-time data on their manufacturing processes, and compare performance across their plants, or even shifts within their plants. With industrial IoT, they can also quickly scale their production up or down; manage their energy consumption; and manage, troubleshoot and fix their processes and plants, even when they are located around the world.
Still, most people continue to be confused when it comes to IoT.
According to Michael Ford, the European marketing director for Aegis Industrial Software Corp., "If you think about what IoT is, people’s expectation is that we can exchange data between devices, obviously systems, quite like you would look up things on the Internet. And the technologies for creating the transported data between these systems make it easy to do. I mean, any software developer can go online, have a look at a couple of live bus controller units (BCUs) and set up a genuine IoT kind of communication protocol, maybe a device or two. There’s no end of things that they can create. I was at a trade show recently in Italy, and there were many different stands there, each of them showing their own IoT solution that they’d been creating. They were advertising things like taking data into the cloud, or sharing data with people, etc. And in all those cases, it was simply that there was a mechanism for moving data from one place to another. This isn’t groundbreaking technology; you could send it on USB sticks or email. There are so many different ways of doing it. So, I think that people are jumping on it kind of like a bandwagon, seeing that IoT is a popular technology and trying to create solutions that are IoT, but in actual fact are simply new ways of transferring the same data as we’ve been transferring before."
More and more equipment manufacturers are promoting Industry 4.0-capable solutions—and in a way, IoT can be seen as an element of Industry 4.0. The idea behind it is that factories would evolve to be able to be a lot more flexible, to be able to make the products that customers want, basically at any time that they need. In this manufacturing vision, customers can call their manufacturers about how many products they want, almost on a day-by-day basis. That must be achieved without accumulating stock, because anybody could build a load, put them in the warehouse and then call them off as needed—but then you’ve got the added cost of warehousing and risk of depreciation while they’re being stored there. So, the idea of Industry 4.0 is that factories will be flexible.
"Now, this flexibility comes at a cost, because everyone in the SMT industry knows that the higher the mix of product, the lower the overall productivity of the machines," says Ford. "Looking at how that works, we see that people are using Excel spreadsheets to do planning, and we’re seeing a lot of manual intervention in the decision making about what products should be made. And this is where the delays come in and why we are not able to optimize our factories for high-mix production."
On the other hand, Ford explains that if computers were able to make the decisions based on the data that's coming to them about the status and the progress and all of the things going on that support production, like the supply chain and tools, and if a computer could see that information and it was accurate and reliable, then it is in a position to start making a decision that previously people were making. "So, instead of people having meetings and sending emails and engaging in discussions and arguments in the canteen or around the water cooler, over the course of hours, days or even weeks, the computer can make a decision within seconds. Now, the key element to drive this is that that decision must be based on good information, and that information must be accurate and timely."
As we all know, Ford has been instrumental in promoting the IPC Connected Factory Exchange (CFX) Initiative, an electronics manufacturing industry developed standard forming the foundation/backbone of Industry 4.0 applications. IPC-CFX simplifies and standardizes machine-to-machine communication while also facilitating machine to business/business to machine solutions.
To read the full article, which appeared in the September 2018 issue of SMT007 Magazine, click here.
Testimonial
"Our marketing partnership with I-Connect007 is already delivering. Just a day after our press release went live, we received a direct inquiry about our updated products!"
Rachael Temple - AlltematedSuggested Items
Creating Connections in Mexico
07/30/2025 | Michelle Te, Community MagazineA concerted effort by the Global Electronics Association—Mexico team over the past year has created inroads for the Global Electronics Association (formerly IPC) with leading electronics companies, government offices, and academic institutions in Mexico. “Our goal is to bring more awareness to what the Global Electronics Association is and what it offers,” says Lorena Villanueva, senior director. “We also aim to increase our membership. Of 3,200 members of the Global Electronics Association, only 180 are in Mexico.”
Powering Progress: Summer 2025 Community Magazine Now Available
07/22/2025 | Community MagazineIn the new Summer 2025 edition of Community Magazine, members of the Global Electronics Association demonstrate what progress really looks like—through innovation on the factory floor, influence on public policy, and investment in the next generation of engineers.
TRI to Exhibit at SMTA Queretaro Expo 2025
07/16/2025 | TRITest Research, Inc. (TRI), the leading provider of test and inspection systems for the electronics manufacturing industry, is pleased to announce plans to exhibit at the SMTA Querétaro Expo 2025, scheduled to take place on July 24, 2025, at the Querétaro Centro de Congresos y Teatro Metropolitano.
Global PCB Connections: Let the Spec Fit the Board, Not Just the Brand
07/17/2025 | Jerome Larez -- Column: Global PCB ConnectionsIf you’ve ever seen an excellent PCB quote delayed, or worse, go cold because of a single line on the fab print, you’re not alone. Often, that line reads something like, “Use 370HR only,” or “IT-180A required.” These and other brand-name materials are proven performers, but unless your design needs that specific resin system (say, for RF performance, thermal reliability, or stringent CAF resistance), you may inadvertently be holding your job hostage.
IPC Hall of Fame Spotlight Series: Highlighting Lionel Fullwood
07/15/2025 | Dan Feinberg, I-Connect007Many IPC members who have contributed significantly to IPC and our industry have been awarded the IPC Raymond E. Pritchard Hall of Fame (HOF) Award. Though many early HOF members have passed away and are unknown to today’s IPC membership, their contributions still resonate. This special series on IPC Hall of Fame members provides a reminder of who was honored and why. As a bonus, for those who are still around, we get to find out what these talented individuals are up to today.