Stretchy Solar Cells a Step Closer
November 16, 2018 | Rice UniversityEstimated reading time: 3 minutes
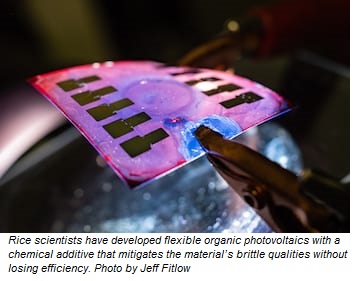
Organic solar cells that can be painted or printed on surfaces are increasingly efficient, and now show promise for incorporation into applications like clothing that also require them to be flexible.
The Rice University lab of chemical and biomolecular engineer Rafael Verduzco has developed flexible organic photovoltaics that could be useful where constant, low-power generation is sufficient.
Verduzco and his team incorporate a network of elastic additives that make the electrically active material less brittle with little to no loss of current flow.
Organic solar cells rely on carbon-based materials including polymers, as opposed to hard, inorganic materials like silicon, to capture sunlight and translate it into current. Organics are also thin, lightweight, semitransparent and inexpensive. While middle-of-the-road, commercial, silicon-based solar cells perform at about 22% efficiency — the amount of sunlight converted into electricity — organics top out at around 15%.
“The field has been obsessed with the efficiency chart for a long time,” Verduzco said. “There’s been an increase in efficiency of these devices, but mechanical properties are also really important, and that part’s been neglected.
“If you stretch or bend things, you get cracks in the active layer and the device fails.”
Verduzco said one approach to fixing the brittle problem would be to find polymers or other organic semiconductors that are flexible by nature, but his lab took another tack. “Our idea was to stick with the materials that have been carefully developed over 20 years and that we know work, and find a way to improve their mechanical properties,” he said.
Rather than make a mesh and pour in the semiconducting polymers, the Rice researchers mixed in sulfur-based thiol-ene reagents. The molecules blend with the polymers and then crosslink with each other to provide flexibility.
The process is not without cost, because too little thiol-ene leaves the crystalline polymers prone to cracking under stress, while too much dampens the material’s efficiency.
Testing helped the lab find its Goldilocks Zone. “If we replaced 50% of the active layer with this mesh, the material would get 50% less light and the current would drop,” Verduzco said. “At some point, it’s not practical. Even after we confirmed the network was forming, we needed to determine how much thiol-ene we needed to suppress fracture and the maximum we could put in without making it worthless as an electronic device.”
At about 20% thiol-ene, they found that cells retained their efficiency and gained flexibility. “They’re small molecules and don’t disrupt the morphology much,” Verduzco said. “We can shine ultraviolet light or apply heat or just wait, and with time the network will form. The chemistry is mild, fast and efficient.”
The next step was to stretch the material. “Pure P3HT (the active polythiophene-based layer) started cracking at about 6% strain,” Verduzco said. “When we added 10% thiol-ene, we could strain it up to 14%. At around 16% strain we started seeing cracks throughout the material.”
At strains higher than 30%, the material flexed just fine but became useless as a solar cell. “We found there’s essentially no loss in our photocurrent up to about 20%,” he said. “That seems to be the sweet spot.”
Damage under strain affected the material even when the strain was released. “The strain impacts how these crystal domains pack and translates to microscopic breaks in the device,” Verduzco said. “The holes and electrons still need paths to get to the opposite electrodes.”
He said the lab expects to try different organic photovoltaic materials while working to make them more stretchable with less additive for larger test cells.
Rice graduate student Jorge Wu Mok is lead author of the paper. Co-authors are Rice graduate student Zhiqi Hu, undergraduate Changxu Sun and alumnus Isaiah Barth; summer researchers Rodrigo Muñoz and Joshua Jackson of Rice and Houston Community College; research scientist Tanguy Terlier of Rice’s Shared Equipment Authority; and Kevin Yager of Brookhaven National Laboratory, Upton, New York.
The research was supported by the National Science Foundation, the Welch Foundation for Chemical Research and the Department of Energy Office of Science Facilities.
Suggested Items
Symposium Review: Qnity, DuPont, and Insulectro Forge Ahead with Advanced Materials
07/02/2025 | Barb Hockaday, I-Connect007In a dynamic and informative Innovation Symposium hosted live and on Zoom on June 25, 2025, representatives from Qnity (formerly DuPont Electronics), DuPont, and Insulectro discussed the evolving landscape of flexible circuit materials. From strategic corporate changes to cutting-edge polymer films, the session offered deep insight into design challenges, reliability, and next-gen solutions shaping the electronics industry.
Indium Corporation Expert to Present on Automotive and Industrial Solder Bonding Solutions at Global Electronics Association Workshop
06/26/2025 | IndiumIndium Corporation Principal Engineer, Advanced Materials, Andy Mackie, Ph.D., MSc, will deliver a technical presentation on innovative solder bonding solutions for automotive and industrial applications at the Global Electronics A
Gorilla Circuits Elevates PCB Precision with Schmoll’s Optiflex II Alignment System
06/23/2025 | Schmoll MaschinenGorilla Circuits, a leading PCB manufacturer based in Silicon Valley, has enhanced its production capabilities with the addition of Schmoll Maschinen’s Optiflex II Post-Etch Punch system—bringing a new level of precision to multilayer board fabrication.
Day 1: Cutting Edge Insights at the EIPC Summer Conference
06/17/2025 | Pete Starkey, I-Connect007The European Institute for the PCB Community (EIPC) Summer Conference took place this year in Edinburgh, Scotland, June 3-4. This is the second of three articles on the conference. The other two cover the keynote speeches and Day 2 of the technical conference. Below is a recap of the first day’s sessions.
American Made Advocacy: Supporting the Entire PCB Ecosystem—Materials to OEMs
06/17/2025 | Shane Whiteside -- Column: American Made AdvocacyWith the addition of RTX to PCBAA’s membership roster, we now represent the interests of companies in the entire PCB ecosystem. From material providers to OEMs, the insights of our collective members help us educate, advocate, and support legislation and policy favorable to America’s microelectronics manufacturers. The industry veterans who lead these companies provide valuable perspective, and their accumulated wisdom makes us an even stronger association.