-
-
News
News Highlights
- Books
Featured Books
- smt007 Magazine
Latest Issues
Current IssueWhat's Your Sweet Spot?
Are you in a niche that’s growing or shrinking? Is it time to reassess and refocus? We spotlight companies thriving by redefining or reinforcing their niche. What are their insights?
Moving Forward With Confidence
In this issue, we focus on sales and quoting, workforce training, new IPC leadership in the U.S. and Canada, the effects of tariffs, CFX standards, and much more—all designed to provide perspective as you move through the cloud bank of today's shifting economic market.
Intelligent Test and Inspection
Are you ready to explore the cutting-edge advancements shaping the electronics manufacturing industry? The May 2025 issue of SMT007 Magazine is packed with insights, innovations, and expert perspectives that you won’t want to miss.
- Articles
- Columns
- Links
- Media kit
||| MENU - smt007 Magazine
Eutect's Sensitive Wire Feeder (SWF) Celebrates 10th Anniversary
November 22, 2018 | Eutect GmbHEstimated reading time: 2 minutes
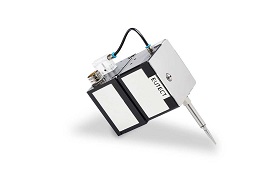
10 years ago Eutect GmbH developed the world's first and so travel only force-controlled wire feeder, the SWF. The SWF is used in particular in the field of laser soldering. In the context of the 10th anniversary, the SWF has been refined once again.
"The SWF is one of our most successful modules", stated Matthias Fehrenbach, CEO of Eutect GmbH, joyfully. In 2008 he developed the force-controlled wire feeder in the context of a student research project. In the years that followed the module was continuously refined, and now in its latest version is also going into the third dimension. "During the further development our focus was on weight reduction, improved servicing capability as well as increased flexibility, in particular for robot applications", emphasized Fehrenbach.
The entire module was slimmed down by almost 300 g. New drive rollers and an optimized wire guide enable simple and fast adaptation of the module to different wire thicknesses. Furthermore, through these improvements the servicing is facilitated, because the key components of the module are easily accessible. Likewise, in future the wire reels can be freely integrated. This is enabled by means of a supply tube, through which the wire is guided.
A further optimization is the module's inclination detection. As a result, with immediate effect the module can also be employed for 3D resurfacing welding as well as installed on a 6-axis robot. "In particular the use on a robot arm enables new opportunities for us to offer 100% process-oriented solutions for our customers. Due to the third dimension of use as well as the freely integrable wire reel, we gain further flexibility and new possibilities for the realization of complex customer projects", explained Fehrenbach.
The control of the SWF has also been expanded. Thanks to a newly developed, compact control unit with the name EcoGerD, even more parameters and interfaces can be activated and regulated via the user interface. The visualization has also been simplified and enables fast and uncomplicated use of the control system. "We are already looking forward to the delighted customers, who can solve the tasks of tomorrow with the further development, and that we will celebrate even more product anniversaries", stated Fehrenbach.
About Eutect
For over 20 years, soldering and joining systems have been developed, manufactured, installed, and programmed at EUTECT as well as commissioned at customers throughout the world. The Swabian team of experts offers a comprehensive, constantly evolving module construction kit for process solutions in the field of soldering.
From process modules of the most varied of soldering techniques, the optimal modules with regard to process technology and efficiency are selected for the task and combined to proven stand-alone, rotary transfer or inline production concepts for complete solutions.
The EUTECT modular construction kit shows, that with individual modules or free combinations a lean, individual solution of proven modules can often be achieved for the task of a customer product.
For the optimal solution through evaluation or the manufacture of A-B-C prototypes ready for series production, there is a technologically comprehensive and innovative EUTECT technology center available.
Suggested Items
Hands-On Demos Now Available for Apollo Seiko’s EF and AF Selective Soldering Lines
06/30/2025 | Apollo SeikoApollo Seiko, a leading innovator in soldering technology, is excited to spotlight its expanded lineup of EF and AF Series Selective Soldering Systems, now available for live demonstrations in its newly dedicated demo room.
SolderKing’s Successful Approach to Modern Soldering Needs
06/18/2025 | Nolan Johnson, I-Connect007Chris Ward, co-founder of the family-owned SolderKing, discusses his company's rapid growth and recent recognition with the King’s Award for Enterprise. Chris shares how SolderKing has achieved these award-winning levels of service in such a short timeframe. Their secret? Being flexible in a changing market, technical prowess, and strong customer support.
E-tronix Announces Upcoming Webinar with ELMOTEC: Optimizing Soldering Quality and Efficiency with Robotic Automation
05/30/2025 | E-tronixE-tronix, a Stromberg Company, is excited to host an informative webinar presented by Raphael Luchs, CEO of ELMOTEC, titled "Optimize Soldering Quality and Efficiency with Robotic Automation," taking place on Wednesday, June 4, 2025 at 12:00 PM CDT.
SMTA Releases Final Batch of Training Resources Donated by Bob Willis
05/29/2025 | SMTAThe Surface Mount Technology Association (SMTA) announces the release of several more webinars, poster sets, and photo libraries to conclude a generous donation from renowned industry expert Bob Willis.
Altus Supports Phoenix Systems in Advancing THT Assembly with Robotic Soldering
05/27/2025 | Altus GroupAltus Group, a leading distributor of capital equipment in the UK and Ireland, has successfully supported Phoenix Systems UK Ltd in its investment in robotic soldering technology to further enhance its through-hole technology (THT) assembly processes.