-
- News
- Books
Featured Books
- smt007 Magazine
Latest Issues
Current IssueWhat's Your Sweet Spot?
Are you in a niche that’s growing or shrinking? Is it time to reassess and refocus? We spotlight companies thriving by redefining or reinforcing their niche. What are their insights?
Moving Forward With Confidence
In this issue, we focus on sales and quoting, workforce training, new IPC leadership in the U.S. and Canada, the effects of tariffs, CFX standards, and much more—all designed to provide perspective as you move through the cloud bank of today's shifting economic market.
Intelligent Test and Inspection
Are you ready to explore the cutting-edge advancements shaping the electronics manufacturing industry? The May 2025 issue of SMT007 Magazine is packed with insights, innovations, and expert perspectives that you won’t want to miss.
- Articles
- Columns
- Links
- Media kit
||| MENU - smt007 Magazine
3D Printing and Medical Electronics: A Disruptive Beneficial Technology
December 11, 2018 | Dan Feinberg, Technology Editor, I-Connect007Estimated reading time: 3 minutes
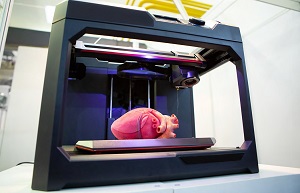
It seems that every few months, we hear about new advances in disruptive technologies. As these technologies become accepted to a greater degree, there are additional areas to research. One of the areas we have been following is additive/semi-additive 3D manufacturing with PCB fabrication as the main focus.
However, another innovative area is 3D-printed manufactured devices, replacement body parts, and medications in the medical industry. We are seeing significant advances and increased uses for 3D manufacturing in medicine—many more than 3D-printed and conductive circuits on device structural components (e.g., conductors printed on a device wall or structural angle, etc.). There is enough movement in this area that 3D additive fabrication in medicine—including but not limited to 3D-printed circuits—has become its own topic, and one that we will be watching and continuing to cover.
Overview
First, let’s take a look at the present status of this segment to set a foundation for future coverage, especially as we are about to enter the high-tech trade show season where new advances will be introduced. Since we are discussing 3D-printed devices that are used on or in the human body, let’s review the Food and Drug Administration (FDA) definition.
“3D printing is a type of additive manufacturing. There are several types of additive manufacturing, but the terms ‘3D printing’ and ‘additive manufacturing’ are often used interchangeably. Here, we will refer to both as 3D printing for simplicity. 3D printing is a process that creates a three-dimensional object by building successive layers of raw material. Each new layer is attached to the previous one until the object is complete. Objects are produced from a digital 3D file, such as a computer-aided design (CAD) drawing or a magnetic resonance image (MRI). The flexibility of 3D printing allows designers to make changes easily without the need to set up additional equipment or tools. It also enables manufacturers to create devices matched to a patient’s anatomy (patient-specific devices) or devices with very complex internal structures. These capabilities have sparked huge interest in the 3D printing of medical devices and other products, including food, household items, and automotive parts.”
Figure 1: 3D-printed dentures.
As those of you who have followed our coverage of disruptive technologies know, 3D additive technology has transformed many industry segments already, which includes significant changes to the medical and dental industries. 3D printing has been used to manufacture dentures and other oral implants for years but is also proving to be useful in other areas (Figure 1). For example, I recently chose to have a tooth replaced with an implant. In the past, it was necessary for the oral surgeon to take numerous X-rays from differing angles, combine them, and use them to measure and create the specifications for the implant fabricator. This time, I only had to do a single 360° 3D image that allowed the surgeon to design the perfect implant at the exact size and shape needed with CAD. The entire process took 15 minutes. It is no wonder that fast, high-quality 3D scanning has replaced X-rays as the preferred method of gathering the necessary data for so many areas of medicine.
Beyond dental devices, 3D printing is also being used to manufacture an entirely new generation of advanced medical implants that can be customized for individual patients’ bodies. It is also starting to become commonly used in numerous areas, such as surgery planning and patient consultations. In addition, as we have seen at the last few consumer electronics shows (CESs), 3D-printed manufacturing technology is revolutionizing the prosthetic and assistive devices segments. 3D-printed manufacturing is now providing access to reasonably priced, highly customized and optimized prosthetics for individual needs on a case-by-case basis (Figure 2).
Figure 2: 3D prosthetic.
According to a new market report from London-based industrial research firm Future Market Insights, the unexpected growth of the 3D-printed medical devices market is likely to be a fixture for some time to come. The report notes that medical communities worldwide are adopting 3D printing technology, and the use of 3D-printed devices at a consistent and rapid pace. It adds that the technology is leading to significantly improved quality of care for patients and is capable of reducing the average procedure time for most surgical applications.
This new industry benefits patients, and it also provides great improvements for doctors and hospitals by lowering the strain placed on already overworked staff. Overall, 3D printing leads to lower costs, which benefits those who would never have been able to afford traditionally manufactured devices. Now, people can afford and use greatly improved devices—such as my dental implant—rather than having to have a false tooth like my parents’ generation had to endure.
To read the full article, which appeared in the November 2018 issue of SMT007 Magazine, click here.
Suggested Items
Zollner Completes Full Acquisition of Bluechips Microhouse
07/01/2025 | Zollner Elektronik AGZollner Elektronik AG has successfully finalized its com- plete takeover of Bluechips Microhouse Co., Ltd., in Thailand. In the future the company will operate as part of the Zollner Group of companies under the leadership of Thomas Kiefl – strategically networked, technologically focused and internationally oriented.
Inission Acquires the Lithuanian Company Selteka
07/01/2025 | InissionInission AB has signed an agreement to acquire 100% of UAB Selteka. Selteka is a well-respected EMS (electronics manufacturing services) company with operations located in Kaunas, Lithuania.
Kitron Strengthens Order Backlog with EUR 11 Million Contract for Defense Communication
07/01/2025 | KitronKitron has received an order valued at EUR 11 million to produce advanced military communication products destined for the European market.
TRI Unveils New Multi-Camera AOI, TR7500 SIII Ultra
07/01/2025 | TRITest Research, Inc. (TRI), the leading test and inspection systems provider for the electronics manufacturing industry, proudly introduces the new TR7500 SIII Ultra.
IMI Wins Gold Award for Best Managed Technology Company at FinanceAsia’s 29th Asia’s Best Companies Awards
07/01/2025 | IMIIntegrated Micro-Electronics Inc. (IMI) has been awarded the prestigious Gold Award for Best Managed Technology Company at the 29th edition of the Asia’s Best Companies Awards, hosted by FinanceAsia.