Better Biomedical Devices, Wearable Displays May Result From Tiny Light-Guiding Structures
December 17, 2018 | OSAEstimated reading time: 3 minutes
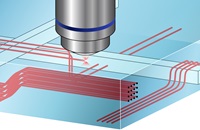
For the first time, researchers have fabricated light-guiding structures known as waveguides just over one micron wide in a clear silicone commonly used for biomedical applications. The tiny, flexible waveguides can be used to make light-based devices such as biomedical sensors and endoscopes that are smaller and more complex than currently possible.
Image Caption: Researchers optimized a laser writing process to create extremely narrow waveguides in a type of silicone known as PDMS. The new waveguides could be used to transport light in a variety of sensors, lab-on-a-chip systems and wearable devices. Credit: Ye Pu, École Fédérale de Lausanne.
“To the best of our knowledge, these are the smallest optical waveguides ever created in polydimethylsiloxane, or PDMS,” said research team member Ye Pu of École Fédérale de Lausanne in Switzerland. “Our flexible waveguides could be integrated into microfluidic lab-on-a-chip systems to eliminate bulky external optics needed to perform blood tests, for example. They might also deliver light for wearable devices such as a shirt featuring a display.”
As reported in the journal Optical Materials Express, the new optical waveguides are not only thinner than a piece of dust, they also exhibit very low light loss when used with certain wavelengths of light. A light-based signal can travel through the new waveguides for 10 centimeters or more before an unacceptable degradation of the signal will occur.
Creating Structures with Light
The researchers made the new waveguides by optimizing laser direct writing, a microfabrication approach that creates detailed 3-D structures by polymerizing a light sensitive chemical with a precisely positioned focused laser. Polymerization converts relatively small molecules called monomers into large, chainlike polymers.
The new approach does not require a photoinitiator, which is typically used to efficiently absorb the laser light and convert it into chemical energy that initiates polymerization. “By not using a photoinitiator, we simplified the fabrication process and also enhanced the compatibility of the final device with living tissue,” Pu said. “This enhanced biocompatibility could allow the approach to be used to make implantable sensors and devices.”
The new flexible waveguides could also serve as building blocks for photonic printed circuit boards that use high-speed optical signals rather than electrical links to transmit data in computers and other electronic devices.
Confining the Light
To achieve a small optical waveguide that efficiently confines light, there must be a large difference between the refractive index of the material making up the waveguides and the surrounding PDMS. The researchers used phenylacetylene for the waveguides because, compared to traditionally used materials, it has a higher refractive index once polymerized. As an added benefit, it also can be easily loaded into PDMS simply by soaking the PDMS in liquid phenylacetylene.
After soaking the PDMS in phenylacetylene, the researchers used focused ultrafast laser pulses to induce an optical phenomenon known as multiphoton absorption in which multiple photons are absorbed at once. Multiphoton laser direct writing produces much finer structures than one-photon processes because the volume of polymerization at each writing spot is much smaller. Using multiphoton laser direct writing also allowed the researchers to directly initiate phenylacetylene polymerization without a photoinitiator. They then evaporated any unpolymerized phenylacetylene by heating the PDMS.
The researchers showed that this new approach could make flexible waveguides in PDMS that are just 1.3 microns wide. For the 650 to 700 nanometer spectral band, only 0.07% of the light transmitted through the waveguides is lost every centimeter. Optimizing the setup would likely allow fabrication of waveguides that are smaller than 1 micron, according to the researchers.
A Flexible Endoscope
The researchers are now working to improve the yield of the fabrication process by developing a control system that would help avoid material damage during laser writing. They also plan to create an array of narrow waveguides in PDMS that could be used to construct a very flexible endoscope with a diameter of less than one millimeter.
“Such a small, mechanically flexible endoscope would allow a number of hard-to-reach places in the body to be imaged for diagnosis in the clinic, or for monitoring in a minimally invasive surgery,” said Pu.
Suggested Items
Symposium Review: Qnity, DuPont, and Insulectro Forge Ahead with Advanced Materials
07/02/2025 | Barb Hockaday, I-Connect007In a dynamic and informative Innovation Symposium hosted live and on Zoom on June 25, 2025, representatives from Qnity (formerly DuPont Electronics), DuPont, and Insulectro discussed the evolving landscape of flexible circuit materials. From strategic corporate changes to cutting-edge polymer films, the session offered deep insight into design challenges, reliability, and next-gen solutions shaping the electronics industry.
Flexible Electronics Market to Reach $66.9 Billion by 2032, Growing at a CAGR of 9.2% from 2025
06/30/2025 | PRNewswireThe flexible electronics market is projected to reach $66.9 billion by 2032, up from an estimated $38.4 billion in 2025, growing at a robust CAGR of 9.2% during the forecast period.
All Flex Solutions Upgrades Lamination Layup
06/22/2025 | All Flex SolutionsAll Flex Solutions has invested in Ulrich Rotte lamination layup stations in their rigid flex layup area. The Ulrich Rotte stations automate the layup process by handling the lamination plates, which are heavy, and sequencing the layup process for the operators.
SEMI FlexTech Solicits Proposals for Advancing the Future of Flexible Hybrid Electronics
06/18/2025 | SEMIFlexTech, a SEMI Technology Community, today issued a Request for Proposals (RFP) to advance flexible hybrid electronics (FHE) technologies, including the development of advanced materials and additive processing.
Roll-to-Roll Technologies for Flexible Devices Set to Grow at 11.5% CAGR
06/11/2025 | GlobeNewswireAccording to the latest study from BCC Research, the “Global Markets for Roll-to-Roll Technologies for Flexible Devices” is expected to reach $69.8 billion by the end of 2029 at a compound annual growth rate (CAGR) of 11.5% from 2024 to 2029.