Graphene’s Magic is in the Defects
December 21, 2018 | NYUEstimated reading time: 2 minutes
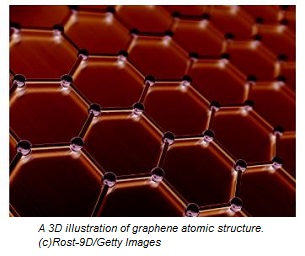
A team of NYU researchers has solved a longstanding puzzle of how to build ultra-sensitive, ultra-small electrochemical sensors with homogenous and predictable properties by discovering how to engineer graphene structure on an atomic level.
A team of researchers at the New York University Tandon School of Engineering and NYU’s Center for Neural Science has solved a longstanding puzzle of how to build ultra-sensitive, ultra-small electrochemical sensors with homogenous and predictable properties by discovering how to engineer graphene structure on an atomic level.
Finely tuned electrochemical sensors (also referred to as electrodes) that are as small as biological cells are prized for medical diagnostics and environmental monitoring systems. Demand has spurred efforts to develop nanoengineered carbon-based electrodes, which offer unmatched electronic, thermal, and mechanical properties. Yet these efforts have long been stymied by the lack of quantitative principles to guide the precise engineering of the electrode sensitivity to biochemical molecules.
Davood Shahrjerdi, an assistant professor of electrical and computer engineering at NYU Tandon, and Roozbeh Kiani, an assistant professor of neural science and psychology at the Center for Neural Science, have revealed the relationship between various structural defects in graphene and the sensitivity of the electrodes made of it. This discovery opens the door for the precise engineering and industrial-scale production of homogeneous arrays of graphene electrodes.
Graphene is a single, atom-thin sheet of carbon. There is a traditional consensus that structural defects in graphene can generally enhance the sensitivity of electrodes constructed from it. However, a firm understanding of the relationship between various structural defects and the sensitivity has long eluded researchers. This information is particularly vital for tuning the density of different defects in graphene in order to achieve a desired level of sensitivity.
“Until now, achieving a desired sensitivity effect was akin to voodoo or alchemy — oftentimes, we weren’t sure why a certain approach yielded a more or less sensitive electrode,” Shahrjerdi said. “By systematically studying the influence of various types and densities of material defects on the electrode’s sensitivity, we created a physics-based microscopic model that replaces superstition with scientific insight.”
In a surprise finding, the researchers discovered that only one group of defects in graphene’s structure — point defects — significantly impacts electrode sensitivity, which increases linearly with the average density of these defects, within a certain range. “If we optimize these point defects in number and density, we can create an electrode that is up to 20 times more sensitive than conventional electrodes,” Kiani explained.
These findings stand to impact both the fabrication of and applications for graphene-based electrodes. Today’s carbon-based electrodes are calibrated for sensitivity post-fabrication, a time-consuming process that hampers large-scale production, but the researchers’ findings will allow for the precise engineering of the sensitivity during the material synthesis, thereby enabling industrial-scale production of carbon-based electrodes with reliable and reproducible sensitivity.
Currently, carbon-based electrodes are impractical for any application that requires a dense array of sensors: The results are unreliable due to large variations of the electrode-to-electrode sensitivity within the array. These new findings will enable the use of ultra-small carbon-based electrodes with homogeneous and extraordinarily high sensitivities in next-generation neural probes and multiplexed “lab-on-a-chip” platforms for medical diagnostics and drug development, and they may replace optical methods for measuring biological samples including DNA.
Suggested Items
TT Electronics Achieves ISO 13485 Medical Certification at Mexicali EMS Facility
06/27/2025 | TT ElectronicsThis milestone underscores TT Electronics’ commitment to delivering high-quality, compliant, and reliable manufacturing solutions to its global customers in healthcare and life sciences.
Elementary Mr. Watson: Retro Routers vs. Modern Boards—The Silent Struggle on Your Screen
06/26/2025 | John Watson -- Column: Elementary, Mr. WatsonThere's a story about a young woman preparing a holiday ham. Before putting it in the pan, she cuts off the ends. When asked why, she shrugs and says, "That's how my mom always did it." She asks her mother, who gives the same answer. Eventually, the question reaches Grandma, who laughs and says, "Oh, I only cut the ends off because my pan was too small." This story is a powerful analogy for how many PCB designers approach routing today.
Stephen Winchell Appointed DARPA Director
06/02/2025 | DARPAStephen Winchell was sworn in today as the 24th director of the Defense Advanced Research Projects Agency.
Uyemura Expands Engineering Team in Great Lakes Region
05/30/2025 | UyemuraAndrew Jin has joined Uyemura’s Engineering Team as Technical Service Engineer for the Midwest. Jin was formerly with Sensient Technologies, Flavors and Extracts Division, where his focus was CO2 emissions and water quality; he also did capital project work with production equipment.
Defining the Ideal PCB Design Data Output
05/27/2025 | Stephen V. Chavez, Siemens EDAAt the heart of delivering successful, manufacturable printed circuit boards lies a vital question: What should your design data output package include to best support manufacturing? The answer: It depends. There are many factors to consider regarding the specific category you’re designing for—such as mil/aero, space, medical, and commercial. Other factors that need to be considered are requirements and engineering intent.