Ventec at IPC APEX EXPO 2019—Delivering on Price, Performance and Availability for High Frequency PCB Materials
January 17, 2019 | Ventec International GroupEstimated reading time: 2 minutes
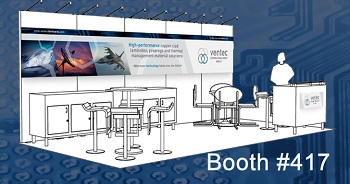
Ventec International Group Co., Ltd. will be showcasing its latest high reliability PCB materials on booth #417 at IPC APEX EXPO 2019 in San Diego from 29-31 January. A key focus at the show will be Ventec's extended ceramic-filled hydrocarbon thermoset material series tec-speed 20.0 which is designed for the world's most demanding high frequency printed circuit board applications. The global Ventec team will be on hand to present the company's unique laminate and prepreg capability across a very wide range of applications and budgets.
Following on from its global launch at electronica in November last year, Ventec's extended tec-speed 20.0 range of ceramic-filled hydrocarbon thermoset material series will make its US debut at IPC APEX EXPO2019. Combining unrivaled high-frequency performance (Dk 3.00-3.48 / Df 0.002-0.0037), superior loss characteristics and the highest reliability with fast availability and efficient delivery through Ventec's fully controlled and managed global supply chain and technical support-network, the tec-speed 20.0 series offers excellent dimensional stability and uniform mechanical properties that help limit PIM. The extended tec-speed 20.0 range is already proving to be very popular with customers demanding high-performance, reliable and cost-efficient high frequency materials that are supported by a fast and efficient global delivery promise and dependable technical support.
PCB-Material Showcase
Booth visitors are invited to view Ventec's product & material showcase, which will demonstrate a range of PCB material applications including power- and LED lighting modules. The showcase will illustrate examples of IMS boards combined with FR-4 control boards made with Ventec's high performance and highly reliable IMS materials like VT-4B5SP, VT-4B5L and VT-4B7.
Automotive Executive Forum Presentation
Automotive manufacturers around the world already rely on Ventec's thermal management materials for a range of applications including LED headlights, ECU, break energy reclamation & e-power train, establishing Ventec as a global leader in technology for high performance thermal management materials. At the IPC's Automotive Executive Forum on 28 January, Ventec's Technology Ambassador Alun Morgan has been invited to present his paper on 'Developing Universal Solutions to Automotive Materials Challenges'. Alun's presentation will demonstrate how Ventec was able to quickly develop thermal management solutions for challenging automotive applications by working collaboratively with Tier 1 automotive suppliers.
Thermal Interface Materials
As a perfect complement to Ventec's IMS material families, thermally conductive and standard laminates and prepregs for multilayer PCB's, EMI Thermal's Thermal Interface Materials (TIM) will be presented on the booth. The range of materials distributed through Ventec includes double sided thermal tape, electrical insulators, natural graphite and void fillers, that ensure reliability and performance and prevent electronic components from overheating and being damaged or burnt out.
About Ventec International Group
Ventec International is a premier supplier to the Global PCB industry. With volume manufacturing facilities in Taiwan and China and distribution locations and manufacturing sites in both the US and Europe, Ventec specializes in advanced copper clad glass reinforced and metal backed substrates. Ventec materials, which include high-quality enhanced FR-4, high-speed/low-loss and high-performance IMS material technology and an advanced range of thermal management solutions, are manufactured by Ventec using strict quality-controlled processes that are certified to AS9100 Revision D, IATF 16949:2016 and ISO 9001:2015, and are backed by a fully controlled and managed global supply chain, sales- and technical-support network.
Visit I-007eBooks to download your copy of Ventec micro eBook today:
The Printed Circuit Designer's Guide to...Thermal Management with Insulated Metal Substrates
Suggested Items
RF PCB Design Tips and Tricks
05/08/2025 | Cherie Litson, EPTAC MIT CID/CID+There are many great books, videos, and information online about designing PCBs for RF circuits. A few of my favorite RF sources are Hans Rosenberg, Stephen Chavez, and Rick Hartley, but there are many more. These PCB design engineers have a very good perspective on what it takes to take an RF design from schematic concept to PCB layout.
Trouble in Your Tank: Causes of Plating Voids, Pre-electroless Copper
05/09/2025 | Michael Carano -- Column: Trouble in Your TankIn the business of printed circuit fabrication, yield-reducing and costly defects can easily catch even the most seasoned engineers and production personnel off guard. In this month’s column, I’ll investigate copper plating voids with their genesis in the pre-plating process steps.
Elephantech: For a Greener Tomorrow
04/16/2025 | Marcy LaRont, PCB007 MagazineNobuhiko Okamoto is the global sales and marketing manager for Elephantech Inc., a Japanese startup with a vision to make electronics more sustainable. The company is developing a metal inkjet technology that can print directly on the substrate and then give it a copper thickness by plating. In this interview, he discusses this novel technology's environmental advantages, as well as its potential benefits for the PCB manufacturing and semiconductor packaging segments.
Trouble in Your Tank: Organic Addition Agents in Electrolytic Copper Plating
04/15/2025 | Michael Carano -- Column: Trouble in Your TankThere are numerous factors at play in the science of electroplating or, as most often called, electrolytic plating. One critical element is the use of organic addition agents and their role in copper plating. The function and use of these chemical compounds will be explored in more detail.
IDTechEx Highlights Recyclable Materials for PCBs
04/10/2025 | IDTechExConventional printed circuit board (PCB) manufacturing is wasteful, harmful to the environment and energy intensive. This can be mitigated by the implementation of new recyclable materials and technologies, which have the potential to revolutionize electronics manufacturing.