Multitasking Graphene Ink Printed Into Tiny Flexible Supercapacitors
January 23, 2019 | CASEstimated reading time: 2 minutes
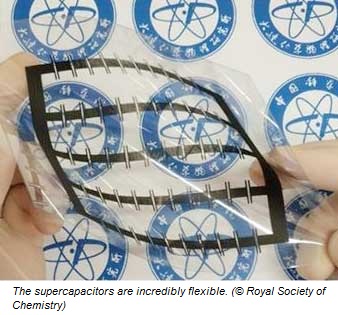
Researchers have developed an easy way to make complicated arrays of microsupercapacitors that involves screen-printing them out of graphene ink (Energy & Environmental Science, "Ultrahigh-voltage integrated micro-supercapacitors with designable shapes and superior flexibility"). The simplicity and freedom offered by the approach will aid the development of new approaches to electronics and flexible devices.
Although semiconductor components continue to shrink, not all of the parts of modern gadgets are as easy to miniaturise. Capacitors and batteries are particularly challenging given that they are complex and discrete bundles of different materials. Microsupercapacitors, a tiny relative of both of these components, can do similar jobs.
Now, scientists have come up with a screen-printing method using a multi-purpose graphene ink that quickly lays down multiple microsupercapacitors in a variety of shapes and as complicated arrays. The ink combines graphene and carbon black, both of which are conductive, with a polymer binder in a solvent, although the simplicity of the mixture belies the difficulty in finding the right composition.
'Preparing inks with suitable electrical, electrochemical and rheological properties was one of the biggest challenges for printable integrated microsupercapacitors,' emphasises Zhong-Shuai Wu, one of the principal investigators on the project.
Importantly, the ink shows shear-thinning behaviour, like ketchup: as it's applied, the force causes it to lose its viscosity so it flows easily, but as soon as the force is removed, it thickens and keeps its shape.
They applied the graphene ink to a substrate, such as glass or flexible PET plastic, using a patterned screen as a stencil. The resulting pattern includes all of the conductive parts of the device.
'The graphene-based ink can act as the microelectrodes, metal-free current collectors and interconnects, simultaneously,' Wu notes. The ink dries for 12 hours, and then an electrolyte gel is applied and allowed to solidify for a further 12 hours, at which point the device is ready to use.
Because the entire structure of the device can be laid out in one step, very complicated designs can be made with ease. Although a single microsupercapacitor supplies less than one volt, the researchers were able to integrate 130 of them in series, giving an output of over 100 volts.
'Micro-robots and soft actuators based on dielectric elastomer require hundreds and even thousands of volts,' says Wu. 'High voltage operation increases the scope and usefulness of microsupercapacitors,' agrees Francesca Iacopi, head of the integrated nanosystems lab at the University of Technology Sydney in Australia.
The devices are also flexible, if they're printed on a flexible substrate, which should make them compatible with wearable electronics.
'The versatility and low cost of this screen-print approach could be a plus in the wearable systems that are disposable, which is what most of the external health monitoring and other wearable systems are meant to be,' says Iacopi. 'I believe microsupercapacitors on flexible substrates like these would be particularly promising to support the area of wearable systems for health monitoring, for example sensors placed on skin and eyes.'
The investigators are keen use their method to make more complete devices, by including components that can harvest energy and store it in the microsupercapacitors, or put that stored energy to use. They also hope to use new electrolytes to increase the voltage each capacitor can provide, and improve the total energy a device can store.
Suggested Items
Symposium Review: Qnity, DuPont, and Insulectro Forge Ahead with Advanced Materials
07/02/2025 | Barb Hockaday, I-Connect007In a dynamic and informative Innovation Symposium hosted live and on Zoom on June 25, 2025, representatives from Qnity (formerly DuPont Electronics), DuPont, and Insulectro discussed the evolving landscape of flexible circuit materials. From strategic corporate changes to cutting-edge polymer films, the session offered deep insight into design challenges, reliability, and next-gen solutions shaping the electronics industry.
Flexible Electronics Market to Reach $66.9 Billion by 2032, Growing at a CAGR of 9.2% from 2025
06/30/2025 | PRNewswireThe flexible electronics market is projected to reach $66.9 billion by 2032, up from an estimated $38.4 billion in 2025, growing at a robust CAGR of 9.2% during the forecast period.
All Flex Solutions Upgrades Lamination Layup
06/22/2025 | All Flex SolutionsAll Flex Solutions has invested in Ulrich Rotte lamination layup stations in their rigid flex layup area. The Ulrich Rotte stations automate the layup process by handling the lamination plates, which are heavy, and sequencing the layup process for the operators.
SEMI FlexTech Solicits Proposals for Advancing the Future of Flexible Hybrid Electronics
06/18/2025 | SEMIFlexTech, a SEMI Technology Community, today issued a Request for Proposals (RFP) to advance flexible hybrid electronics (FHE) technologies, including the development of advanced materials and additive processing.
Roll-to-Roll Technologies for Flexible Devices Set to Grow at 11.5% CAGR
06/11/2025 | GlobeNewswireAccording to the latest study from BCC Research, the “Global Markets for Roll-to-Roll Technologies for Flexible Devices” is expected to reach $69.8 billion by the end of 2029 at a compound annual growth rate (CAGR) of 11.5% from 2024 to 2029.