Customized Mix of Materials for 3D Micro- and Nanostructures
February 14, 2019 | KITEstimated reading time: 2 minutes
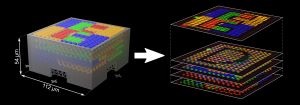
Three-dimensional structures on the micrometer and nanometer scales have a great potential for many applications. An efficient and precise process to print such structures from different materials is now presented by researchers of Karlsruhe Institute of Technology (KIT) and Carl Zeiss AG in Science Advances: they integrated a microfluidic chamber into a 3D laser lithography device. Then, they used this system to produce multi-colored, fluorescent security features to protect banknotes, documents, and branded products against counterfeiting.
Image Caption: Multi-colored fluorescent security feature in computer design (left) and its layers under the laser scanning microscope (right). (Figure: Frederik Mayer, INT/KIT)
From components for data processing with light to optical microlenses, mechanical metamaterials, or artificial scaffolds for cell cultures to security features of banknotes or branded products, printed three-dimensional micro- and nanostructures have a large range of applications. 3D laser lithography has become an established, reliable, and versatile process for their production. A laser beam is passed through a liquid photoresist in a computer-controlled way and the material is exposed and hardened at the focal point of the laser beam only. This gives rise to highly precise filigree structures for many applications, including optics and photonics, materials sciences, biotechnology or security technology. Nearly all of the micro- and nanostructures produced by 3D laser lithography so far consist of a single material. But they might also be manufactured from several materials by successive application and hardening of different photoresists, with the unexposed resist being washed out in a subsequent developing bath. Such a process, however, is very time-consuming and complicated and its precision decreases with an increasing number of materials and repetitions.
Within the Cluster of Excellence “3D Matter Made to Order,” scientists of KIT’s Institutes of Nanotechnology (INT), of Applied Physics (APH), for Chemical Technology and Polymer Chemistry (ITCP), and of the School of Chemistry of Queensland University of Technology (QUT) in Brisbane/Australia, together with researchers of Carl Zeiss AG, have now developed a new system for the efficient and precise production of printed micro- and nanostructures from several materials. They integrated a microfluidic chamber for the fluids on smallest space directly into a 3D laser lithography device.
In their publication “Multimaterial 3D Laser Microprinting Using an Integrated Microfluidic System” in Science Advances, the researchers report that they used the integrated system to produce three-dimensional microstructured security features from seven different fluids: a non-fluorescent photoresist as backbone, two photoresists with different fluorescent quantum points, two photoresists with different fluorescent dyes, and two developer fluids. Such security features may protect banknotes, documents, and branded products against counterfeiting. A security feature consists of a three-dimensional lattice enclosed by retaining walls and fluorescent markers in different colors.
For their system, the scientists used a 3D laser lithography device developed and commercialized by Nanoscribe GmbH, a spinoff of KIT, and integrated it into a self-developed microfluidic chamber. It is provided with a cover glass of ten millimeters in diameter onto which the 3D structures can be printed. The chamber is connected to an electronic pressure control, up to ten containers for the different photoresists and developers, and a star-shaped selection valve. The fluid selected is passed to a specimen holder via an overpressure valve. Finally, it flows into a waste container. “All steps for producing three-dimensional micro- and nanostructures from several materials can be integrated into one system,” says Professor Martin Wegener, who heads the working group at APH. “This system paves the way towards multi-material additive manufacture on the micro- and nanoscale.”
Suggested Items
Accenture Acquires SYSTEMA to Drive Manufacturing Automation for Semiconductor Clients
07/02/2025 | AccentureAccenture has acquired SYSTEMA, a provider of software solutions and consulting services for manufacturing automation, headquartered in Dresden, Germany.
Driving Innovation: Direct Imaging vs. Conventional Exposure
07/01/2025 | Simon Khesin -- Column: Driving InnovationMy first camera used Kodak film. I even experimented with developing photos in the bathroom, though I usually dropped the film off at a Kodak center and received the prints two weeks later, only to discover that some images were out of focus or poorly framed. Today, every smartphone contains a high-quality camera capable of producing stunning images instantly.
Specially Developed for Laser Plastic Welding from LPKF
06/25/2025 | LPKFLPKF introduces TherMoPro, a thermographic analysis system specifically developed for laser plastic welding that transforms thermal data into concrete actionable insights. Through automated capture, evaluation, and interpretation of surface temperature patterns immediately after welding, the system provides unprecedented process transparency that correlates with product joining quality and long-term product stability.
United Electronics Corporation Advances Manufacturing Capabilities with Schmoll MDI-ST Imaging Equipment
06/24/2025 | United Electronics CorporationUnited Electronics Corporation has successfully installed the advanced Schmoll MDI-ST (XL) imaging equipment at their advanced printed circuit board facility. This significant technology investment represents a continued commitment to delivering superior products and maintaining their position as an industry leader in precision PCB manufacturing.
IBM, RIKEN Unveil First IBM Quantum System Two Outside of the U.S.
06/24/2025 | IBMIBM and RIKEN, a national research laboratory in Japan, today unveiled the first IBM Quantum System Two ever to be deployed outside of the United States and beyond an IBM Quantum Data Center.