-
- News
- Books
Featured Books
- smt007 Magazine
Latest Issues
Current IssueWhat's Your Sweet Spot?
Are you in a niche that’s growing or shrinking? Is it time to reassess and refocus? We spotlight companies thriving by redefining or reinforcing their niche. What are their insights?
Moving Forward With Confidence
In this issue, we focus on sales and quoting, workforce training, new IPC leadership in the U.S. and Canada, the effects of tariffs, CFX standards, and much more—all designed to provide perspective as you move through the cloud bank of today's shifting economic market.
Intelligent Test and Inspection
Are you ready to explore the cutting-edge advancements shaping the electronics manufacturing industry? The May 2025 issue of SMT007 Magazine is packed with insights, innovations, and expert perspectives that you won’t want to miss.
- Articles
- Columns
- Links
- Media kit
||| MENU - smt007 Magazine
Improving the Efficiency of Your PCBA Production
February 15, 2019 | Neil Sharp, JJS ManufacturingEstimated reading time: 3 minutes
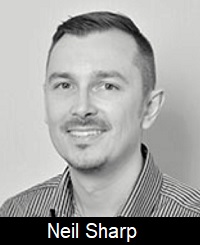
Ensuring you're hitting your build times is always a major priority in surface mount production. The challenge for many original equipment manufacturers (OEMs), however, is that the processes involved with printed circuit board assembly (PCBA) can be numerous and complex. And the smallest of details can make the biggest of differences.
In this article, we explore four core electronic component packaging issues that will help you streamline production, meet your targets, and keep your costs down.
1. Keep Component Variations to a Minimum
It’s not uncommon to find that a design engineer has listed several similar components against the same board reference when specifying the bill of materials (BOMs). While this element of choice might be offered with the best intentions, it can prove a challenge as the parts that are supplied by different manufacturers can potentially vary in size and shape.
Surface mount pick-and-place programs are often set up against one specific part. Any deviations outside of the expected tolerances could result in the part being rejected and the production line coming to a grinding halt. For consistency, always request that your materials supplier settles on just one approved part—or at the very least, they should give you the heads up about any possible variations so your pick-and-place programs can be updated offline and you can avoid any costly machine downtime.
2. Opt for the Most Efficient Packaging
The format in which devices are supplied can vary widely—especially when it comes to integrated circuits (ICs). Typical IC packaging methods can include waffle trays, tubes, and reels—each of which are often differentiated by a specific letter or number at the end of the part number.
If you're aiming for optimum efficiency, then taped and reeled parts are preferable as the use of tubed components relies on having operators on hand to change the parts over as the tubes become empty, which can delay the manufacturing process. There are, of course, certain situations where requesting taped and reeled parts simply may not be viable such as in the case of new product introductions (NPIs) where batch sizes are typically smaller. In those situations, it probably won’t make commercial sense to purchase a larger quantity of device just so you can receive it in a taped and reeled format.
If you do decide to change a part from being in tubed packaging to tape and reel, you will also want to make sure that the quality of the seal on the cover tape is sufficient. A poor-quality seal increases the risk of the cover tape dislodging, which can mean components could become damaged or lost.
3. Avoid Splicing Components
Sometimes, a combination of smaller amounts of taped and reeled components may need to be spliced together to create one larger, continuous strip. But if this splicing is poorly executed, there is an increased chance that the tape could become stuck in the surface mount machine feeders. And if the cover tape pulls away from the carrier tape, then you will be left with a jammed machine that will need to be resolved by an operator, leading to costly downtime.
4. Plan for Things to Not Always Go to Plan
Inherent within the manufacturing process is the knowledge that things occasionally don’t go quite as expected. If a surface mount machine misplaces, drops, or damages a component, and you don’t have more of that component in stock, then you’re likely to be left with two tough choices. You can opt to carry on with the SMT build regardless and fit the part by hand once it arrives, or you can halt the job while you order (and wait for) the replacement part. The reality is that neither option is especially ideal. Fitting parts by hand can affect quality, increase the risk of damage, and impact your lead times. Meanwhile, opting to halt the job means your machines are sitting idle and costing you money.
Building attrition into your kit of parts may cost you a small amount at the outset, but it can potentially save you hundreds of pounds in additional rework. So, whenever possible, make sure you request a few more of each component than you actually think you’re going to need. The smallest of details can have a massive impact on the efficiency of your PCBA production. By having a program in place to continually monitor and refine your processes, you will be able to identify and eliminate what is not working, retain a firm hand on quality, and boost your profitability.
Neil Sharp is the director of marketing for JJS Manufacturing.
Suggested Items
Count On Tools Recognizes Donna Orr’s Ongoing Leadership and Impact Across 27+ Years
06/26/2025 | Count On ToolsCount On Tools, Inc. (COT), a leading provider of precision components and SMT spare parts, is proud to recognize Donna Orr, Executive Manager, for her continued dedication and leadership as she marks more than 27 years with the company.
A Record Year for the 75th Annual IEEE Electronic Components and Technology Conference (ECTC)
06/26/2025 | ECTCThe 75th annual 2025 IEEE Electronic Components and Technology Conference (ECTC), held at the Gaylord Texan Resort & Convention Center here May 27-30, had record attendance, a record number of paper submissions/presentations, record international and student participation, and a record number of exhibitors in a sold-out exhibition hall:
The Death of the Microsection
06/26/2025 | Bob Neves, Reliability Assessment Solutions, Inc.I got my start out of college grinding and polishing PCB microsections. My thumbs are a bit arthritic today because of the experience (microsection grinders know what I mean). Back then, via structures were rather large, and getting to the center in six steps of grinding and polishing was easy compared to what my team has been doing recently at the lab.
Specially Developed for Laser Plastic Welding from LPKF
06/25/2025 | LPKFLPKF introduces TherMoPro, a thermographic analysis system specifically developed for laser plastic welding that transforms thermal data into concrete actionable insights. Through automated capture, evaluation, and interpretation of surface temperature patterns immediately after welding, the system provides unprecedented process transparency that correlates with product joining quality and long-term product stability.
Fresh PCB Concepts: Assembly Challenges with Micro Components and Standard Solder Mask Practices
06/26/2025 | Team NCAB -- Column: Fresh PCB ConceptsMicro components have redefined what is possible in PCB design. With package sizes like 01005 and 0201 becoming more common in high-density layouts, designers are now expected to pack more performance into smaller spaces than ever before. While these advancements support miniaturization and functionality, they introduce new assembly challenges, particularly with traditional solder mask and legend application processes.