A Flexible Future
February 20, 2019 | UNSW SydneyEstimated reading time: 2 minutes
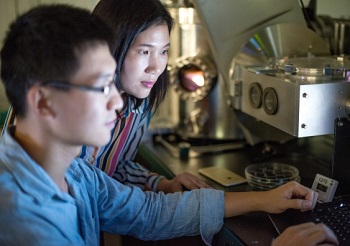
Thin, flexible panels that will revolutionise how we use solar energy are on the drawing board at UNSW. Imagine a future in which thin, flexible solar panels cover the surfaces of cars and buildings, powering their activities.
Xiaojing Hao, associate professor and Scientia fellow in the School of Photovoltaic and Renewable Energy Engineering, and her team, are building such cells made of kesterite photovoltaics.
Containing copper, zinc, tin and sulphur, they are cheaper to make and more environmentally friendly than other thin-film varieties on the market, some of which contain toxic materials, such as cadmium, or rare elements, such as indium and tellurium.
There are significant industrial applications for flexible, thin photovoltaic cells. But a key challenge has been their limited capacity to generate energy with a comparable efficiency and cost to that of conventional silicon solar panels.
In 2017, A/Prof Hao’s team built a kesterite photovoltaic cell that attained 11% efficiency. This set a world record—a fourth for the team—and was the first time that the 10% efficiency threshold was broken for this type of cell. This work was published in the Nature Energy journal in 2018.
“For each efficiency change, we need a step-change technology to make it happen,” says A/Prof Hao. She hopes to improve the efficiency of kesterite photovoltaic cells to close to 20% in the next five years.
To do this, her team needs to work out how to prevent the common defects in the lattice of the kesterite material. The reasons for these defects are not yet well understood. However, once corrected, the electrical quality of the material—the main barrier to efficiency—will improve.
Exciting findings from 2018 point to some new directions to control the defects and improve the performance of kesterite cells. The plan is to apply for Australian Research Council funding to delve deeper and publish some of these results in 2019.
Dr Xiaojing Hao of UNSW's Australian Centre for Advanced Photovoltaics holding the new CZTS solar cells.
In 2017, A/Prof Hao was one of 18 young scientists selected from more than 1000 applicants to take up one of UNSW’s inaugural Scientia fellowships. Last year, she won two prestigious prizes: the $5000 Premier’s Prize for Energy Innovation from the state of New South Wales and the $3000 UNSW Engineering Faculty Dean’s Award for Excellence in Research. A/Prof Hao’s enthusiasm for discovery is given free rein at UNSW.
“I love to explore the unknowns and deal with challenges. Achieving research progress, particularly through challenging work, brings me deep fulfilment.”
Suggested Items
RF PCB Design Tips and Tricks
05/08/2025 | Cherie Litson, EPTAC MIT CID/CID+There are many great books, videos, and information online about designing PCBs for RF circuits. A few of my favorite RF sources are Hans Rosenberg, Stephen Chavez, and Rick Hartley, but there are many more. These PCB design engineers have a very good perspective on what it takes to take an RF design from schematic concept to PCB layout.
Trouble in Your Tank: Causes of Plating Voids, Pre-electroless Copper
05/09/2025 | Michael Carano -- Column: Trouble in Your TankIn the business of printed circuit fabrication, yield-reducing and costly defects can easily catch even the most seasoned engineers and production personnel off guard. In this month’s column, I’ll investigate copper plating voids with their genesis in the pre-plating process steps.
Elephantech: For a Greener Tomorrow
04/16/2025 | Marcy LaRont, PCB007 MagazineNobuhiko Okamoto is the global sales and marketing manager for Elephantech Inc., a Japanese startup with a vision to make electronics more sustainable. The company is developing a metal inkjet technology that can print directly on the substrate and then give it a copper thickness by plating. In this interview, he discusses this novel technology's environmental advantages, as well as its potential benefits for the PCB manufacturing and semiconductor packaging segments.
Trouble in Your Tank: Organic Addition Agents in Electrolytic Copper Plating
04/15/2025 | Michael Carano -- Column: Trouble in Your TankThere are numerous factors at play in the science of electroplating or, as most often called, electrolytic plating. One critical element is the use of organic addition agents and their role in copper plating. The function and use of these chemical compounds will be explored in more detail.
IDTechEx Highlights Recyclable Materials for PCBs
04/10/2025 | IDTechExConventional printed circuit board (PCB) manufacturing is wasteful, harmful to the environment and energy intensive. This can be mitigated by the implementation of new recyclable materials and technologies, which have the potential to revolutionize electronics manufacturing.