Causes for Defects in 3D Printing and Paves Way for Better Results
February 22, 2019 | PRNewswireEstimated reading time: 6 minutes
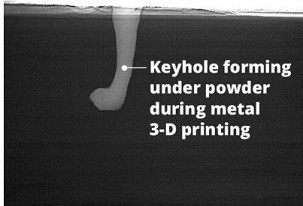
Additive manufacturing's promise to revolutionize industry is constrained by a widespread problem: tiny gas pockets in the final product, which can lead to cracks and other failures.
This image, taken under the synchrotron at Argonne National Laboratory, shows a keyhole void forming during the metal 3-D printing process. During laser powder bed fusion, a 3-D printer “drills” a hole into the metal.
New research published today in Science, led by researchers from Carnegie Mellon University and Argonne National Laboratory, has identified how and when these gas pockets form, as well as a methodology to predict their formation—a pivotal discovery that could dramatically improve the 3D printing process.
"The research in this paper will translate into better quality control and better control of working with the machines," said Anthony Rollett, a Professor of Materials Science and Engineering at Carnegie Mellon University and an author on the paper. "For additive manufacturing to really take off for the majority of companies, we need to improve the consistency of the finished products. This research is a major step in that direction."
The scientists used the extremely bright high-energy X-rays at Argonne's Advanced Photon Source (APS), a DOE Office of Science User Facility, to take super-fast video and images of a process called Laser Power Bed Fusion (LPBF), in which lasers are used to melt and fuse material powder together.
The lasers, which scan over each layer of powder to fuse metal where it is needed, literally create the finished product from the ground up. Defects can form when pockets of gas become trapped into these layers, causing imperfections that could lead to cracks or other breakdowns in the final product.
Until now, manufacturers and researchers did not know much about how the laser drills into the metal, producing cavities called "vapor depressions," but they assumed that the type of metal powder or strength of laser were to blame. As a result, manufacturers have been using a trial and error approach with different types of metals and lasers to seek to reduce the defects.
In fact, the research shows that these vapor depressions exist under nearly all conditions in the process, no matter the laser or metal. Even more important, the research shows how to predict when a small depression will grow into a big and unstable one that can potentially create a defect.
"We're drawing back the veil and revealing what's really going on," Rollett said. "Most people think you shine a laser light on the surface of a metal powder, the light is absorbed by the material, and it melts the metal into a melt pool. In actuality, you're really drilling a hole into the metal."
By using highly specialized equipment at Argonne's APS, one of the most powerful synchrotron facilities in the world, researchers watched what happens as the laser moves across the metal powder bed to create each layer of the product.
Under perfect conditions, the melt pool shape is shallow and semicircular, called the "conduction mode." But during the actual printing process, the high-power laser, often moving at a low speed, can change the melt pool shape to something like a keyhole in a warded lock: round and large on top, with a narrow spike at bottom. Such "keyhole mode" melting can potentially lead to defects in the final product.
"Based on this research, we now know that the keyhole phenomenon is more important, in many ways, than the powder being used in additive manufacturing," said Ross Cunningham, a recent graduate from Carnegie Mellon University and one of the co-first authors of this paper. "Our research shows that you can predict the factors that lead to a keyhole—which means you can also isolate those factors for better results."
The research shows that keyholes form when a certain laser power density is reached that is sufficient to boil the metal. This, in turn, reveals the critical importance of the laser focus in the additive manufacturing process, an element that has received scant attention so far, according to the research team.
"The keyhole phenomenon was able to be viewed for the first time with such details because of the scale and specialized capability developed at Argonne," said Tao Sun, an Argonne physicist and an author on the paper. "The intense high-energy X-ray beam at the APS is key to discoveries like this."
The experiment platform that supports study of additive manufacturing includes a laser apparatus, specialized detectors, and dedicated beamline instruments.
Page 1 of 2
Suggested Items
Delta SEA Partner Event 2025 Unites Regional Partners to Embrace a “Future Ready” Vision
07/03/2025 | Delta ElectronicsDelta Electronics (Thailand) Public Company Limited, successfully hosted its Delta SEA Partner Event 2025: Future Ready at Delta Chungli Plant 5, Taiwan on June 10 – 11 , 2025.
Murray Percival Company Welcomes CeTaQ to Its Line Card, Optimizing SMT Processes for PCB Manufacturers
07/03/2025 | Murray Percival CompanyThe Murray Percival Company, a trusted supplier to the Midwest's electronics industry, is pleased to announce that it has added CeTaQ to its line card, a global expert in Surface Mount Technology (SMT) measurement systems.
RBB’s Jeff Schartiger Appointed to SMTA Ohio Board as Technical Advisor
07/03/2025 | RBBRBB, a trusted leader in electronics manufacturing since 1973, is proud to announce that Jeff Schartiger, Operations Manager at RBB, has been appointed to the SMTA Ohio Chapter Board as a Technical Advisor.
Kitron Receives EUR 4 Million Contract for Defense Airborne Radar Application
07/02/2025 | KitronKitron has received an order valued at EUR 4 million to produce electronics modules for airborne radar application, destined for the US market.
Zollner Completes Full Acquisition of Bluechips Microhouse
07/01/2025 | Zollner Elektronik AGZollner Elektronik AG has successfully finalized its complete takeover of Bluechips Microhouse Co., Ltd., in Thailand. In the future the company will operate as part of the Zollner Group of companies under the leadership of Thomas Kiefl—strategically networked, technologically focused and internationally oriented.