Driverless Car Project Researches Advances in Vehicle Connectivity
March 12, 2019 | University of BristolEstimated reading time: 1 minute
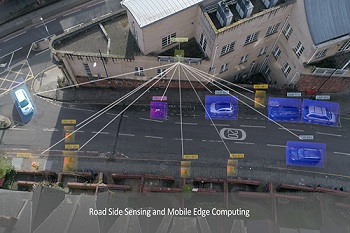
The £5.5m FLOURISH driverless car project has successfully completed the latest phase of its investigations into the requirements of the cyber-physical infrastructure of the future.
Pioneered by the University of Bristol, a member of the FLOURISH consortium, the findings of this research give new insights into the ability of connected vehicles to communicate with each component in the system, including other connected vehicles and the roadside and digital infrastructure.
“Digitally connected vehicles have the potential to revolutionise the cities we live in and the way we travel. Our research into the optimum conditions for the robust, effective and resilient transfer of data is the cornerstone of a new customer journey experience,” said Robert Piechocki, professor of Wireless Systems at the University of Bristol.
The FLOURISH car trials explore the minimum conditions needed for data to be effectively transferred. They focus on the level of connectivity required to communicate with integrity, to respond to real-time traffic events and to identify if the source of information is trustworthy. With its varied topography, the results proven in Bristol are directly transferrable to other cities across the country, in both even and more challenging terrain. The project is testing ever more complex scenarios to assure the recommendations it makes and their application elsewhere.
“By enabling the management of a network of driverless cars, we can help transport authorities to improve road safety, ease congestion and tackle the challenge of improving air quality, by offering a genuine alternative to manually driven cars,” added Professor Piechocki.
In addition, the project is also exploring the potential for connected and autonomous vehicles to communicate with each other and the surrounding infrastructure using frequencies typically associated with WiFi. Usually seen as an enabler of indoor connectivity, its low frequencies can enable data to be effectively transmitted for longer distances.
Suggested Items
Specially Developed for Laser Plastic Welding from LPKF
06/25/2025 | LPKFLPKF introduces TherMoPro, a thermographic analysis system specifically developed for laser plastic welding that transforms thermal data into concrete actionable insights. Through automated capture, evaluation, and interpretation of surface temperature patterns immediately after welding, the system provides unprecedented process transparency that correlates with product joining quality and long-term product stability.
Smart Automation: The Power of Data Integration in Electronics Manufacturing
06/24/2025 | Josh Casper -- Column: Smart AutomationAs EMS companies adopt automation, machine data collection and integration are among the biggest challenges. It’s now commonplace for equipment to collect and output vast amounts of data, sometimes more than a manufacturer knows what to do with. While many OEM equipment vendors offer full-line solutions, most EMS companies still take a vendor-agnostic approach, selecting the equipment companies that best serve their needs rather than a single-vendor solution.
Keysight, NTT, and NTT Innovative Devices Achieve 280 Gbps World Record Data Rate with Sub-Terahertz for 6G
06/17/2025 | Keysight TechnologiesKeysight Technologies, Inc. in collaboration with NTT Corporation and NTT Innovative Devices Corporation (NTT Innovative Devices), today announced a groundbreaking world record in data rate achieved using sub-THz frequencies.
Priority Software Announces the New, Game-Changing aiERP
06/12/2025 | Priority SoftwarePriority Software Ltd., a leading global provider of ERP and business management software announces its revolutionary aiERP, leveraging the power of AI to transform business operations.
Breaking Silos with Intelligence: Connectivity of Component-level Data Across the SMT Line
06/09/2025 | Dr. Eyal Weiss, CybordAs the complexity and demands of electronics manufacturing continue to rise, the smart factory is no longer a distant vision; it has become a necessity. While machine connectivity and line-level data integration have gained traction in recent years, one of the most overlooked opportunities lies in the component itself. Specifically, in the data captured just milliseconds before a component is placed onto the PCB, which often goes unexamined and is permanently lost once reflow begins.