Mass Manufacturing of Metasurfaces
March 18, 2019 | A*STAREstimated reading time: 1 minute
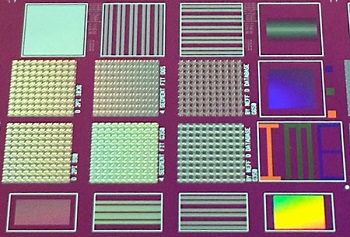
The mass production of flat optical devices with sub-wavelength structures could soon be a reality, thanks to a metasurface fabrication technique developed by researchers at A*STAR.
Image Caption: The metasurface's nano-pillar arrays displaying the letters I, M and E in red, green and blue, respectively. (The Optical Society)
Metasurfaces are synthetic, two-dimensional materials covered in tiny individual shapes with sizes and spacings smaller than the wavelengths of visible light. These ‘sub-wavelength’ structures enable scientists to precisely control the propagating shape, or wavefront, of light beams. As such, metasurfaces show promise for many applications from high-resolution imaging and color printing to controlling light polarization. Mass production of metasurfaces, however, has proven challenging, limited by the complexity of realizing such precise patterns.
Now, Ting Hu and his colleagues at A*STAR’s Institute of Microelectronics (IME) have developed a method of building silicon-based metasurfaces by introducing existing techniques from semiconductor fabrication. Their new metasurface design can produce high-resolution red-green-blue (RGB) color displays.
Until now, metasurfaces have mainly been fabricated via electron beam lithography (EBL), which is not applicable to mass production, as Hu explains:
“With EBL, the focused electron beam moves slowly, step by step, across the metasurface substrate. Metasurfaces with millions — possibly billions — of elements require a very long time to be patterned via EBL. We desired a faster and more efficient way of patternation.”
Hu and the team based their technique on ‘immersion lithography’, which has long been used to etch patterns on to electronic components. With multiple exposures, complex patterns can be built up. The researchers used ultraviolet-based (UV) lithography for initial patternation on to silicon substrates, followed by plasma etching to form the designs in small pixel blocks that were assembled into a 12-inch display surface (see image).
“Our UV lithography tool is a scanner, which can pattern a whole 12 inch wafer with designed devices within half an hour,” says Hu. “We designed the physical dimensions of the nano-pillar arrays of the metasurface to accurately display colors, with fantastic results, for example displaying the letters I, M and E in red, green and blue respectively.”
Hu and the team hope to optimize their design and improve the etching process to minimize losses induced by light scattering and defects in the nano-structure arrays. They are also making efforts to realize flat, lightweight ‘meta-lenses’ and dot projectors with potential uses in facial recognition technologies.
Suggested Items
Driving Innovation: Direct Imaging vs. Conventional Exposure
07/01/2025 | Simon Khesin -- Column: Driving InnovationMy first camera used Kodak film. I even experimented with developing photos in the bathroom, though I usually dropped the film off at a Kodak center and received the prints two weeks later, only to discover that some images were out of focus or poorly framed. Today, every smartphone contains a high-quality camera capable of producing stunning images instantly.
United Electronics Corporation Advances Manufacturing Capabilities with Schmoll MDI-ST Imaging Equipment
06/24/2025 | United Electronics CorporationUnited Electronics Corporation has successfully installed the advanced Schmoll MDI-ST (XL) imaging equipment at their advanced printed circuit board facility. This significant technology investment represents a continued commitment to delivering superior products and maintaining their position as an industry leader in precision PCB manufacturing.
Orbel Corporation Integrates Schmoll Direct Imaging
06/04/2025 | Schmoll AmericaOrbel Corporation in Easton, PA, proudly becomes the first PCM facility in the U.S. equipped with Schmoll’s MDI Direct Imaging system. This installation empowers Orbel to support customers with greater precision and quality.
Key Insights on Photoresist for Defect Reduction
05/21/2025 | I-Connect007 Editorial TeamIn PCB manufacturing, understanding the intricacies of the photoresist process is crucial for achieving high-quality results. Industry experts Josh Krick, a technical service engineer at IEC, and Tim Blair, a PCB imaging specialist at Tim Blair LLC, share their knowledge on the essential stages of photoresist application, highlight critical advancements in materials, and discuss common defects encountered during production. They share best practices and innovative solutions to enhance the manufacturing process, reduce defects, and ensure efficiency and reliability in high-tech applications.
NXP Unveils Third-Generation Imaging Radar Processors for Level 2+ to 4 Autonomous Driving
05/09/2025 | NXP SemiconductorNXP Semiconductors N.V. unveiled its new S32R47 imaging radar processors in 16 nm FinFET technology, building on NXP’s proven expertise in the imaging radar space.