-
- News
- Books
Featured Books
- pcb007 Magazine
Latest Issues
Current IssueThe Hole Truth: Via Integrity in an HDI World
From the drilled hole to registration across multiple sequential lamination cycles, to the quality of your copper plating, via reliability in an HDI world is becoming an ever-greater challenge. This month we look at “The Hole Truth,” from creating the “perfect” via to how you can assure via quality and reliability, the first time, every time.
In Pursuit of Perfection: Defect Reduction
For bare PCB board fabrication, defect reduction is a critical aspect of a company's bottom line profitability. In this issue, we examine how imaging, etching, and plating processes can provide information and insight into reducing defects and increasing yields.
Voices of the Industry
We take the pulse of the PCB industry by sharing insights from leading fabricators and suppliers in this month's issue. We've gathered their thoughts on the new U.S. administration, spending, the war in Ukraine, and their most pressing needs. It’s an eye-opening and enlightening look behind the curtain.
- Articles
- Columns
- Links
- Media kit
||| MENU - pcb007 Magazine
TTM on Flex and Rigid-flex PCB Challenges
March 20, 2019 | Barry Matties, I-Connect007Estimated reading time: 4 minutes
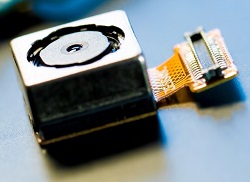
One of the biggest bareboard manufacturers in the world, TTM Technologies (TTM), has seen a recent surge in flex and rigid-flex demands from their customers. In this interview, Clay Zha, Vice President of Technology Solutions of TTM’s Mobility business unit, and VP of Corporate Marketing Winnie Ng discuss the differences in manufacturing flex versus traditional PCBs, and the increasing need for rigid-flex HDI boards.
Barry Matties: Clay, can you give us a quick overview of TTM?
Clay Zha: TTM is probably one of the top three PCB manufacturers in the world. If you’re only considering the bare PCB, we’re probably the leader in the world, and right now, we have 29 manufacturing sites across the world. We offer not only rigid PCBs, but also flex and flex assembly, rigid-flex, and EMS solutions. Also, after the acquisition of Anaren, we offer radiofrequency (RF) modules and components as well.
Winnie Ng: As you mentioned, in 2018 we completed the integration of and acquired the company called Anaren. They are a manufacturer of RF and microwave components. We broadened our product horizon and are now positioned for not just PCB manufacturing but also RF and microwave components and assembly for future technologies.
Matties: Let’s talk a little bit about flex and rigid-flex capabilities. First, since you are focused on the mobility business, what sort of percentage of your business is in the flex and rigid-flex space?
Zha: It’s about 20% of the mobility business.
Matties: Flex is certainly one of the faster-growing segments. Do you see that in your overall business as well?
Zha: Especially in 2017, we’ve seen a huge demand from the market because a lot of people require more flexible and reliable connections with thinner, high-density connection devices. That’s where we see the drivers coming from. Some of them come from the signal integrity considerations, and others from the compact assembly needs. You can eventually form a small device with a lot of components and 3D assembled in a very limited geometry with reliable signal transmissions; these are the two areas where we see people adopting rigid-flex and flex.
Matties: You’re in an interesting position because you deal with the people integrating flex into their products.
Zha: For PCB manufacturing, we mainly deal with their PCB interfaces. We rarely deal with their system-level designers, but we did talk about why they require this or what they look for, so we may have some understanding.
Matties: We constantly hear that collaboration from system design to the fabricator and assembler before designing the board is critical and that companies would wind up with a better product overall if they followed that path. Is that the case?
Zha: That is true, and I agree with that point. If the PCB manufacturer can work with customers with early involvement in terms of flex assembly or rigid-flex design, that will definitely help the cost, quality, and reliability of the products.
Flex material is very different than the material used for rigid products. There are also a lot of manual handling processes during flex or rigid-flex manufacturing. For example, how do you design the cavity inside, how do you want to remove the cap of the cavity, and what kind of connection are you trying to realize? All these considerations are going to be linked to the cost, quality, and challenge of manufacturing the FPCs. Early involvement will improve the understanding of the manufacturing process and the final product needs from both parties and put considerations of manufacturability of board and final assembly before the product is designed. It is not straightforward as with rigid PCBs; without communication and careful consideration, a very small design feature that may not be necessary to the function could cause a huge difficulty for the fabricator and could eventually become a yield and cost issue. It’s quite different from traditional rigid PCBs we manufacture at other plants right now.
Matties: Where is the growth you’re experiencing coming from? Is it coming from customers using flex for the first time?
Zha: From our experience, most of our customers are not actually using flex for the first time, but rather we are seeing more project teams within their organization start to adopt flex and rigid-flex technology. Even within one organization, there may be some individuals who are quite familiar with flex products, but there may be other teams that just started and are puzzled about the whole process, materials properties, etc. From our current situation, I would say probably half of our customers have a good understanding of flex and rigid-flex, and the other half are less experienced with flex/rigid-flex or are working with it for the first time.
Even with the half who understands flex, flex assembly, and rigid-flex processes, their understanding of it is not as deep as their knowledge of rigid PCBs. Usually it involves a lot of our rigid-flex/flex field application engineers’ early involvement efforts to provide design consultations and the education they need.
To read the full article, which appeared in the January 2019 issue of FLEX007 Magazine, click here.
Suggested Items
NEPCON ASIA 2025: Innovating Smart Manufacturing Ecosystems and Bridging Global Opportunities
07/11/2025 | PRNewswireTaking place from October 28 to 30, 2025 at the Shenzhen World Exhibition & Convention Center (Bao'an), NEPCON ASIA is the premier platform to discover the latest technologies and market trends, connect with new suppliers and products, and explore potential partnerships and distribution opportunities.
Mycronic Delivers Strong Q2 Performance and Raises 2025 Outlook to SEK 7.5 Billion
07/11/2025 | MycronicMycronic reported a 35% increase in Q2 net sales and a 27% EBIT margin, prompting an upward revision of its full-year 2025 revenue forecast to SEK 7.5 billion.
Cetec ERP Expands into Larger Office to Support Continued Growth
07/11/2025 | Cetec ERPCetec ERP, a leading provider of cloud-based ERP software for manufacturers, has officially relocated to a larger, modern office facility in central Austin as of July 2, 2025.
Digital Twin Concept in Copper Electroplating Process Performance
07/11/2025 | Aga Franczak, Robrecht Belis, Elsyca N.V.PCB manufacturing involves transforming a design into a physical board while meeting specific requirements. Understanding these design specifications is crucial, as they directly impact the PCB's fabrication process, performance, and yield rate. One key design specification is copper thieving—the addition of “dummy” pads across the surface that are plated along with the features designed on the outer layers. The purpose of the process is to provide a uniform distribution of copper across the outer layers to make the plating current density and plating in the holes more uniform.
Kitron Reports Strengthening Momentum in Q2 2025
07/10/2025 | KitronKitron reported solid quarterly sales and profits, particularly driven by the Defence & Aerospace market sector.