True-Meaning Wearable Displays: Self-Powered, Washable and Wearable
March 21, 2019 | KAISTEstimated reading time: 2 minutes
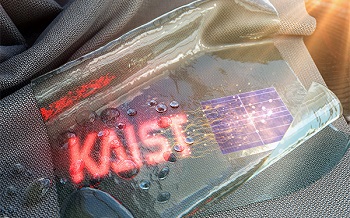
When we think about clothes, they are usually formed with textiles and have to be both wearable and washable for daily use; however, smart clothing has had a problem with its power sources and moisture permeability, which causes the devices to malfunction. This problem has now been overcome by a KAIST research team, who developed a textile-based wearable display module technology that is washable and does not require an external power source.
To ease out the problem of external power sources and enhance the practicability of wearable displays, Professor Kyung Cheol Choi from the School of Electrical Engineering and his team fabricated their wearing display modules on real textiles that integrated polymer solar cells (PSCs) with organic light emitting diodes (OLEDs).
PSCs have been one of the most promising candidates for a next-generation power source, especially for wearable and optoelectronic applications because they can provide stable power without an external power source, while OLEDs can be driven with milliwatts. However, the problem was that they are both very vulnerable to external moisture and oxygen. The encapsulation barrier is essential for their reliability. The conventional encapsulation barrier is sufficient for normal environments; however, it loses its characteristics in aqueous environments, such as water. It limits the commercialization of wearing displays that must operate even on rainy days or after washing.
To tackle this issue, the team employed a washable encapsulation barrier that can protect the device without losing its characteristics after washing through atomic layer deposition (ALD) and spin coating. With this encapsulation technology, the team confirmed that textile-based wearing display modules including PSCs, OLEDs, and the proposed encapsulation barrier exhibited little change in characteristics even after 20 washings with 10-minute cycles. Moreover, the encapsulated device operated stably with a low curvature radius of 3mm and boasted high reliability.
Finally, it exhibited no deterioration in properties over 30 days even after being subjected to both bending stress and washing. Since it uses a less stressful textile, compared to conventional wearable electronic devices that use traditional plastic substrates, this technology can accelerate the commercialization of wearing electronic devices. Importantly, this wearable electronic device in daily life can save energy through a self-powered system.
Professor Choi said, “I could say that this research realized a truly washable wearable electronic module in the sense that it uses daily wearable textiles instead of the plastic used in conventional wearable electronic devices. Saving energy with PSCs, it can be self-powered, using nature-friendly solar energy, and washed. I believe that it has paved the way for a ‘true-meaning wearable display’ that can be formed on textile, beyond the attachable form of wearable technology.”
Figure 1. Schematic and photo of a washable wearing display module
Figure 2. Cover page of Energy and Environmental Science
Suggested Items
Creative Electron Strengthens Leadership Team with Strategic Appointments in Marketing and SMT Business Unit
05/08/2025 | Creative ElectronCreative Electron, the largest U.S. manufacturer of X-ray inspection systems for the electronics industry, is proud to announce the addition of two seasoned leaders to its executive team: Wagner Lima as Marketing Director and Giancarlo De La Garza as SMT Business Unit Director.
LG Electronics India Limited Begins Construction of Its Third Manufacturing Plant in India
05/08/2025 | BUSINESS WIRELG Electronics India Ltd. (LGEIL) announced the commencement of construction of its new manufacturing facility in Sri City, Andhra Pradesh today at a ceremony graced by the presence of Shri Nara Lokesh, Hon'ble Minister for Information Technology, Electronics and Communications.
Scanfil Boosts Investment in Electronics Manufacturing in the US
05/08/2025 | BUSINESS WIREScanfil is investing in a second electronics manufacturing line in Atlanta, Georgia, USA. The demand for manufacturing electronics in the USA has increased over the past two years and is expected to continue growing.
IPC Strengthens Global Focus with Promotion of Sanjay Huprikar to Chief Global Officer
05/08/2025 | IPCIPC, the global electronics association, announces the promotion of Sanjay Huprikar to chief global officer. This newly created position reflects the association’s forward-looking strategy and industry needs to strengthen the electronics supply chain.
IPC White Paper Maps the Regulatory Terrain for Electronics Suppliers in E-Mobility Sector
05/07/2025 | IPCElectronics suppliers supporting the rapidly growing e-mobility sector are facing a dramatic escalation in environmental and social governance (ESG) compliance expectations. A new white paper from IPC’s e-Mobility Quality and Reliability Advisory Group provides a comprehensive overview of the evolving regulatory landscape and outlines the data infrastructure needed to stay ahead.