Researchers Develop High-Resolution, High-Sensitivity Proximity Capacitance Imaging Sensor
April 8, 2019 | Tohoku UniversityEstimated reading time: 3 minutes
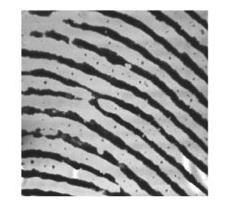
A fingerprint can serve as identification to access locked doors and more, but current scanners can be duped with fake or even similar fingerprints. That may change soon, thanks to a collaborative research team based in Japan.
Proximity capacitance image of a fingerprint. The captured image clearly shows not only the fingerprint, but also sweat pores of the skin. Shigetoshi Sugawa, Tohoku University
The group has developed a new proximity capacitance imaging sensor that has such high sensitivity and resolution, a finger print scan shows more than the swirls of a fingertip—it detects the sweat pores between the ridges.
The prototype sensor was first presented in December at the 2018 IEEE International Electron Devices Meeting in San Francisco, California. A paper describing the details of the sensor was published in the Technical Digests of 2018 International Electron Devices Meeting. Last week, the authors presented new materials and results from the study at a conference organized by the Institute of Image Information and Television Engineers (ITE) in Japan.
"The most significant point of the developed sensor is its high capacitance sensitivity," said paper author Shigetoshi Sugawa, a professor in the Graduate School of Engineering at Tohoku University.
Many touch screen phones and computer track pads use a less sensitive capacitance sensor, where the differences in electrical properties between a sensor and a conductive tool (such as a finger) allow the device to react to scrolling or double clicking. The capacitance increases when the object is closer—the double-click versus lighter scrolling.
The high sensitivity of this capacitance sensor is derived from newly introduced noise reduction technology, according to Sugawa.
Prototype in precision
The sensor chip contains pixels to detect the capacitance between the sample and detection electrodes. Each pixel has one detection electrode attached to it that's capacitively coupled with a ground wire. These electrical signals are converted into images of the samples. Previously, the signals would pick up background noise such as thermal noise and noise due to variability of electrical components of pixels, which made for lower-quality images.
To fix this, the researchers applied reset switches to the detection electrodes and employed a voltage pulse to produce a circuit that can follow the source of noise. The reset switches allow the systems to detect noise arising at the detection electrodes. The voltage pulse alternates the two voltage levels after the reset switches are turned off, effectively cancelling out and removing noise from the system.
It's the equivalent of removing the white and black snow from a television without signal input into a smooth, grey screen. It's much easier to sense any deviation on a solid background.
"This development is important to the general public because it can improve the efficiency of analysis and control in the fields of electronic industry, authentication, life sciences, agriculture, and more," Sugawa said.
Next, Sugawa and the researchers plan to optimize the sensor for specific applications, such as the non-contact inspection equipment of printed circuit boards and flat panels as well as a portable camera system with the developed sensor chip.
The research team consists of Sugawa, as well as Rihito Kuroda, an associate professor, Masahiro Yamamoto, Manabu Suzuki, graduate students both with the Tohoku University's Graduate School of Engineering; Tetsuya Goto, an associate professor with Tohoku University's New Industry Creation Hatchery Center; Hiroshi Hamori, president, Shinichi Murakami and Toshiro Yasuda, at OHT, Inc.
The prototype sensor was first presented in December at the 2018 IEEE International Electron Devices Meeting in San Francisco, California. A paper describing the details of the sensor was published in the Technical Digests of 2018 International Electron Devices Meeting. On March 22, the authors presented new materials and results from the study at a conference organized by the Institute of Image Information and Television Engineers (ITE) in Japan.
Suggested Items
Driving Innovation: Direct Imaging vs. Conventional Exposure
07/01/2025 | Simon Khesin -- Column: Driving InnovationMy first camera used Kodak film. I even experimented with developing photos in the bathroom, though I usually dropped the film off at a Kodak center and received the prints two weeks later, only to discover that some images were out of focus or poorly framed. Today, every smartphone contains a high-quality camera capable of producing stunning images instantly.
United Electronics Corporation Advances Manufacturing Capabilities with Schmoll MDI-ST Imaging Equipment
06/24/2025 | United Electronics CorporationUnited Electronics Corporation has successfully installed the advanced Schmoll MDI-ST (XL) imaging equipment at their advanced printed circuit board facility. This significant technology investment represents a continued commitment to delivering superior products and maintaining their position as an industry leader in precision PCB manufacturing.
Orbel Corporation Integrates Schmoll Direct Imaging
06/04/2025 | Schmoll AmericaOrbel Corporation in Easton, PA, proudly becomes the first PCM facility in the U.S. equipped with Schmoll’s MDI Direct Imaging system. This installation empowers Orbel to support customers with greater precision and quality.
Key Insights on Photoresist for Defect Reduction
05/21/2025 | I-Connect007 Editorial TeamIn PCB manufacturing, understanding the intricacies of the photoresist process is crucial for achieving high-quality results. Industry experts Josh Krick, a technical service engineer at IEC, and Tim Blair, a PCB imaging specialist at Tim Blair LLC, share their knowledge on the essential stages of photoresist application, highlight critical advancements in materials, and discuss common defects encountered during production. They share best practices and innovative solutions to enhance the manufacturing process, reduce defects, and ensure efficiency and reliability in high-tech applications.
NXP Unveils Third-Generation Imaging Radar Processors for Level 2+ to 4 Autonomous Driving
05/09/2025 | NXP SemiconductorNXP Semiconductors N.V. unveiled its new S32R47 imaging radar processors in 16 nm FinFET technology, building on NXP’s proven expertise in the imaging radar space.