Artificial Muscles for Soft Robots
April 9, 2019 | Harvard John A. Paulson School of Engineering and Applied SciencesEstimated reading time: 1 minute
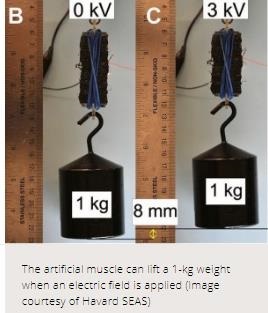
When we think about fast robots, we tend to think of rigid, traditional robotics like those found in factory automation, or perhaps the recent parkour-like demonstrations of the Atlas robot — not soft, squishy devices like the Octobot.
Developing soft, artificial muscles that are also fast and strong is an important step in developing soft robots that can both safely interact with people and complete important tasks.
Now, a team of researchers from the Harvard John A. Paulson School of Engineering and Applied Sciences (SEAS) has developed fully soft, electrically driven artificial muscles that operate on par with natural muscles.
The muscle is made using dielectric elastomers, soft materials with good insulating properties, that deform when an electric field is applied. By using a new combination of nanoscale conductive particles and many layers of thin soft elastomers, the researchers demonstrated that they could achieve contraction forces, motions, and operating frequencies on par with natural muscles.
This artificial muscle could be used for prosthetics, surgical robots, and wearable devices, as well as soft robots capable of locomotion and manipulation in natural or human-centric environments.
“Before this research, we didn't know the limits of performance of dielectric elastomer artificial muscles, meaning how much energy can we put in before they break down, and how much work we could get out,” said Mihai Duduta, Postdoctoral Fellow in Materials Science and Mechanical Engineering and first author of the study. “Now, we can make artificial muscles that are as strong and as fast as natural muscles, and can be driven directly by an electric signal rather than indirectly by a pump, as previous research has done for fluidically-driven artificial muscles.”
Next, the researchers aim to develop more conductive electrodes, and less viscoelastic elastomers to make the muscles even faster and stronger.
The research was co-authored by Robert Wood, the Charles River Professor of Engineering and Applied Sciences at SEAS, David Clarke, Extended Tarr Family Professor of Materials at SEAS, Ehsan Hajiesmaili and Huichan Zhao.
It was supported by the National Science Foundation Materials Research Science and Engineering Center Grant (MRSEC).
Suggested Items
Symposium Review: Qnity, DuPont, and Insulectro Forge Ahead with Advanced Materials
07/02/2025 | Barb Hockaday, I-Connect007In a dynamic and informative Innovation Symposium hosted live and on Zoom on June 25, 2025, representatives from Qnity (formerly DuPont Electronics), DuPont, and Insulectro discussed the evolving landscape of flexible circuit materials. From strategic corporate changes to cutting-edge polymer films, the session offered deep insight into design challenges, reliability, and next-gen solutions shaping the electronics industry.
Indium Corporation Expert to Present on Automotive and Industrial Solder Bonding Solutions at Global Electronics Association Workshop
06/26/2025 | IndiumIndium Corporation Principal Engineer, Advanced Materials, Andy Mackie, Ph.D., MSc, will deliver a technical presentation on innovative solder bonding solutions for automotive and industrial applications at the Global Electronics A
Gorilla Circuits Elevates PCB Precision with Schmoll’s Optiflex II Alignment System
06/23/2025 | Schmoll MaschinenGorilla Circuits, a leading PCB manufacturer based in Silicon Valley, has enhanced its production capabilities with the addition of Schmoll Maschinen’s Optiflex II Post-Etch Punch system—bringing a new level of precision to multilayer board fabrication.
Day 1: Cutting Edge Insights at the EIPC Summer Conference
06/17/2025 | Pete Starkey, I-Connect007The European Institute for the PCB Community (EIPC) Summer Conference took place this year in Edinburgh, Scotland, June 3-4. This is the second of three articles on the conference. The other two cover the keynote speeches and Day 2 of the technical conference. Below is a recap of the first day’s sessions.
American Made Advocacy: Supporting the Entire PCB Ecosystem—Materials to OEMs
06/17/2025 | Shane Whiteside -- Column: American Made AdvocacyWith the addition of RTX to PCBAA’s membership roster, we now represent the interests of companies in the entire PCB ecosystem. From material providers to OEMs, the insights of our collective members help us educate, advocate, and support legislation and policy favorable to America’s microelectronics manufacturers. The industry veterans who lead these companies provide valuable perspective, and their accumulated wisdom makes us an even stronger association.