-
- News
- Books
Featured Books
- smt007 Magazine
Latest Issues
Current IssueWhat's Your Sweet Spot?
Are you in a niche that’s growing or shrinking? Is it time to reassess and refocus? We spotlight companies thriving by redefining or reinforcing their niche. What are their insights?
Moving Forward With Confidence
In this issue, we focus on sales and quoting, workforce training, new IPC leadership in the U.S. and Canada, the effects of tariffs, CFX standards, and much more—all designed to provide perspective as you move through the cloud bank of today's shifting economic market.
Intelligent Test and Inspection
Are you ready to explore the cutting-edge advancements shaping the electronics manufacturing industry? The May 2025 issue of SMT007 Magazine is packed with insights, innovations, and expert perspectives that you won’t want to miss.
- Articles
- Columns
- Links
- Media kit
||| MENU - smt007 Magazine
Building a Smart Factory Supply Line
April 10, 2019 | Barry Matties, I-Connect007Estimated reading time: 4 minutes
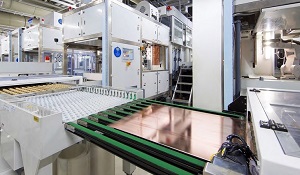
I-Connect007 recently toured Victory Giant Technology (VGT) Co. Ltd. in Huizhou, China—one of China’s largest PCB producers. Currently, VGT generates about US$500 million in annual sales, and have plans to reach $1.5 billion in the coming years. VGT’s facility covers an area of 236,000 square meters with a staff of around 4,000. Its monthly production capacity achieved is currently 600,000 square meters per month and increasing.
Chen Tao founded VGT in Danshui Subdistrict, Huiyang District, Huizhou. Before this, Chen had been working in a Taiwan enterprise as the special assistant to the company president in the early days where he oversaw quality and sales. VGT started construction in 2006 and became operational in 2008. Today, they have three manufacturing facilities with more under construction. Today, Chen continues to lead his team through an impressive expansion plan.
Background
Our tour began in the front offices, and continued through engineering and into factories one, two, and three. The fourth factory—a dedicated HDI facility—is now under construction. Though some resources are shared between the factories, core operations are set up as individual factories. Factory one is basically a traditional PCB shop staffed with operators running each process, but it is being upgraded to support higher mix, lower volume, and higher-tech products.
Factory two is a good example of what automation can do to reduce manpower. Built in 2007, and realizing a 30% reduction in labor, VGT determined that costs could be reduced further with a smart factory. That brought us to factory three—the smartest factory of all.
Designed specifically as a smart factory, this facility removes virtually all of the operators by using software and sensors to manage processes. Though the factory is not entirely optimized as a smart factory yet, work continues to that end.
VGT’s COO Zhou Dingzhong describes it this way, “Compared to our original factory, productivity has increased by 40%, and labor is reduced by 70%. Also, the turnover time has decreased from six to seven days to two days due to the highly automated continuous process.” He continues, “Also, our original factory uses manual handling of materials, which could increase the chance of scratches and defects. We designed our new factory with zero manual handling in mind, which made our yield go up by 5%.”
With three plants running strong, VGT’s ongoing expansion is very evident with construction crews building factory four. This new facility dedicated to HDI will be eight stories and measure around 1 million square feet; it should be operational in May of 2019.
To support all four factories, a new drill center was built, which will house 1,000 drills and be in addition to what they already have in place. There is also a new R&D center, which is under construction. This building will house the large amount of engineering and R&D staff. VGT has dedicated technical staff for R&D projects and a dedicated NPI staff for assisting customers in bringing their new designs to market.
The new center will focus on developing new materials and processes to support 5G wireless, 100 Gbps networking, and automotive markets. Increasing density and improving signal integrity while reducing cost will also be prime focuses.
In addition to all of that construction, a new five-star hotel is being built on location for visiting guests. The property is very impressive with beautiful hills and mountains in the backdrop.
When asked how VGT manages all of their major construction projects, EVP and CTO George Dudnikov said, “We have an internal project manager. Also, our founder [Chen Tao] has provided a lot of target goal input to every factory here and does a lot of the layout.”
Workplace Culture and the Environment
Creating a comfortable campus for employees is important in China as a part of the overall strategy to help keep employee turnover at a minimum. High turnover is a real problem for business in China, especially around the Chinese New Year when employees return to their home cities and often do not come back. I was told that turnover at VGT is lower than average for China. VGT strives to make their campus comfortable and provides amenities for the employees, including basketball courts, a small park for walking and relaxing, a vegetable garden that supplies the employee canteen with fresh veggies, and comfortable onsite dormitories. In fact, Dudnikov stays in the dorms when working in China. He now splits his time between China and the USA.
Employees work 12-hour shifts with one hour-and-a-half break for lunch and another half-hour break. Employees are also provided daily feedback on their performance with a visual grape chart. In China, a lot of factories use this type of grape chart. When an operator hits their KPI targets, they get a blue or green grape. And speaking of green, a real effort is being made here to minimize the waste stream and improve the environment. VGT recently invested over $15 million in upgrading its wastewater recycling capabilities and capacity to support the additional factory expansions. They have also installed rooftop solar panels to generate supplemental electric power. Being green and having a low carbon footprint is a goal for executive management.
A good work environment is also very important to the workers. With so much activity going on, the air quality is quite good. The distinctive PCB shop odor is not present. Local regions in China are getting serious about being environmentally friendly more than ever. It is reported that some companies are being asked to move out of certain regions because they can’t support the environmental requirements. Meanwhile, VGT recently won an award from the Chinese government for being one of two board shops out of 200 with green production and a low carbon footprint; the other one was a quick-turn shop.
To read the full article, which appeared in the March 2019 issue of SMT007 Magazine, click here.
Suggested Items
I-Connect007 Editor’s Choice: Five Must-Reads for the Week
06/20/2025 | Andy Shaughnessy, I-Connect007It’s been a busy week in this industry, and we have news and articles from the PCB design, fabrication and assembly communities. Some of this news is out of this world. We may be losing the high ground—the really high ground. Columnist Jesse Vaughan explains how the U.S. seems to be falling behind in space, and how this could affect our ability to defend ourselves in the future. We have an update on the U.S.-China tariff talks, which seem to be moving forward, though sometimes at a snail’s pace.
MRSI Systems, LLC Files Patent Infringement Lawsuit Against Suzhou LieQi in China
06/16/2025 | MRSI Systems, LLCMRSI Systems, LLC (a part of Mycronic Group), a global high-tech company that provides high precision production solution in electronics industry, filed a patent infringement lawsuit against Suzhou LieQi Intelligent Equipment Co., Ltd. (SZLQ) with Shenzhen Intermediate People’s Court for infringement of MRSI Systems’ patent related to die bonder (Case No. (2025) YUE03minchu No. 7154).
Takeaways from the Keynotes at the Edinburgh EIPC Summer Conference
06/16/2025 | Pete Starkey, I-Connect007It was seasonably wet and windy in Edinburgh, Scotland, June 3-4, where delegates from 17 countries convened for the 2025 EIPC Summer Conference to enjoy a superlative program of 18 technical presentations over two days, plus an excursion to a whisky distillery. EIPC President Alun Morgan welcomed everyone to the Delta Hotel, reminding us that in its previous iteration, it was the Royal Scot, traditionally the annual venue of the Institute of Circuit Technology Northern Symposium.
Global Citizenship: Cultivating Cross-border Partnerships With Integrity
06/11/2025 | Tom Yang -- Column: Global CitizenshipWith rising geopolitical pressures, cross-border partnerships are essential for businesses looking to expand their reach, enhance innovation, and drive sustainable growth. However, these partnerships thrive only when founded on trust and transparency. Otherwise, even the most promising collaborations can quickly unravel, leading to financial losses and reputation damage.
Enough Talk—Time to Strengthen America’s Microelectronics Industrial Base
06/09/2025 | James Will, USPAEThe U.S. doesn’t have an innovation problem in terms of microelectronics, or a talent problem or even an investment problem. What the U.S. has is a coordination problem, and that’s threatening the livelihood of our domestic microelectronics ecosystem.