University Students Point to the Future in their Research
April 23, 2019 | Nolan Johnson, I-Connect007Estimated reading time: 6 minutes
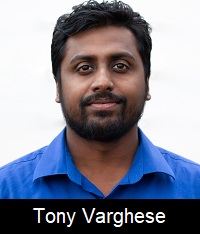
PCB fabrication is a technical business. There’s chemistry, machinery, and complex processes that need to be followed in a competitive environment that changes constantly. Still, the industry continues down an evolutionary, rather than an revolutionary, path, but that may be changing. Cutting-edge automation, artificial intelligence (AI), machine learning, and Industry 4.0 are all part of the response to the increasing demands for printed circuit boards that are not only faster, smaller, and cheaper but also higher-frequency, lower-loss, more temperature tolerant, and higher reliability. In many cases, it will be unique and advanced research coming out of the university system that will help move the industry forward.
In this article, I introduce you to four students who are examples of the caliber of research being undertaken by the youth of this industry. Meet Goutham Ezhilarasu, Tony Verghese, Sameeksha Katoch, and Emma Pederson—three doctoral candidates and an undergraduate engineering student. I became acquainted with them at the recent FlexTech conference hosted in Monterey, California, by SEMI in February 2019. Among them, the basic research they’re conducting includes the development of materials that can either act as a heat exchanger and a thermal sensor (Tony Varghese), AI learning techniques for equipment optimization (Sameeksha Katoch and Emma Pederson), and embedding ICs in flexible interconnect packaging (Goutham Ezhilarasu). These four students discuss their work, goals, and student careers.
Nolan Johnson: What university do you attend, and can you tell me about your research project?
Tony Varghese: I attend Boise State University where I’m doing my Ph.D. I’m in the final year of my degree program, and my work is focusing on flexible thermoelectric generators, which produce electricity based on waste heat or temperature difference. They can also be used as a thermohaptic instrument, so it can produce heat and cold based on the direction you apply current to it. Finally, they can be used for temperature sensing.
Sameeksha Katoch: I’m a Ph.D. student at Arizona State University, working with Emma Pedersen, who is an undergraduate student. And she is working in the NSF Research Experience for Undergraduates (REU) program at the SenSIP center funded by the National Science Foundation I/UCRC program and industry members (i.e., Raytheon, NXP, Intel, Sprint, etc.). We do a couple of projects where a lot of undergraduate students can gain research experience. The NSF cyber-physical systems (CPS) project that Emma is currently working on is related to fault protection in utility-scale solar arrays.
Emma Pedersen: I’m pursuing a degree is in aerospace engineering at Arizona State University.
Goutham Ezhilarasu: I’m a Ph.D. student at the University of California, Los Angeles (UCLA). And I work on flexible hybrid electronics. I’m demonstrating flexible hybrid electronics using a process called fan-out wafer-level packaging (FOWLP), which is a technique popularized by TSMC (Taiwan Semiconductor Manufacturing Company). You demonstrate a full system by reconstituting a wafer around the dies. What I mean by that is you first assemble the dies on a wafer with an adhesive on top, and then you pour the molding compound and let it cure so that the dies are later embedded in the molding compound.
Then, we had separate conversations about their respective research. First up was Tony and his work on thermoelectric generators. Tony describes the current industry situation to give his work some context.
Varghese: Most of the devices you see in the market are bulk; they are pretty solid and rigid. This project focuses on transforming them into flexible devices so that you can connect them into flexible sensors, and eventually have self-powered sensors and devices. The main property we are looking for in thermoelectric material is called the figure of merit (ZT), which is dependent on the electrical conductivity, thermal conductivity, and Seebeck coefficient of the material. In the first process, we develop this thermoelectric material using a screen-printing technique. We develop the material to get a ZT of one, which is very close to bulk devices. Our first goal was to replicate the value in the bulk devices using the flexible additive manufacturing technique.
We did that with the screen printing thermoelectric legs and were able to develop using a four-leg, 54 microwatts of power and with a temperature difference of 80°C and a power density of 18.8 milliwatts per square centimeter. That’s a very high power density, and we can further improve the power density by stacking more legs on this smaller radius. So, that’s where we came up with this aerosol jet printing because it has very fine features and they can print more than legs on a smaller area and improve the power density.
Another technique we use is photonic sintering. It takes eight to 10 hours for the normal thermal sintering of this material. With the photonic sintering, we were able to reduce it to milliseconds, so it is a very fast process. Now, you can print and sinter in a conveyor belt. You print it, upload to the photonic sinter, and it’s done.
Johnson: It’s fast, conveyorized, replicable, and reliable.
Varghese: And it reduces the cost considerably. The cost of manufacturing is almost 80–90% production. In a conventional process, all of this takes place in a semi-additive process. You have to press it and heat it, and again, it could take up to 10 hours to finish the process, and time is money. To do this, we make our own nanocrystals with the right material and tune the nanocrystal size and dimensions; then, we make it into an ink. First, we tune the ink properties to be compatible with aerosol printing. Next, we study what substrate we’re going to print. We study the surface chemistry of the substrate, check the conduct handling, and see how we can improve the wettability of the ink onto the surface and adhesion.
All of these properties are important for thermal sintering because the thermoelectric material and substrate that you’re using on both have a different coefficient of thermal expansion. Photonic sintering has a very short time and high energy pulse. If you have a very different coefficient of thermal expansion, the materials will break apart and the filling doesn’t stick very well to the substrates.
We can print onto flexible Kapton and tubular substrates. The idea is that if you have heat or a cold pipe, with the 3D conformal printing, one option is to print on a flexible substrate and wrap it around the tube. The other option is to print directly onto the tube. If you print directly onto the tube, you can harvest the heat coming out of the tube easier and more efficiently than by wrapping something around it.
That was the idea for conformal printing, and when we started doing that, we found that there was a lot of porosity inside the filling once we print because aerosol jet printing is more like spray printing. It can be random stacking of the material and evaporating solvent while printing on it so that it creates some bubbles and holes in the filling. We applied some isostatic pressing so that it would densify the filling, reduce the interface contact resistance, and allow more contact area. It also helps to have better photonic sintering.
To read the full article, which appeared in the April 2019 issue of PCB007 Magazine, click here.
Suggested Items
Intervala Hosts Employee Car and Motorcycle Show, Benefit Nonprofits
08/27/2024 | IntervalaIntervala hosted an employee car and motorcycle show, aptly named the Vala-Cruise and it was a roaring success! Employees had the chance to show off their prized wheels, and it was incredible to see the variety and passion on display.
KIC Honored with IPC Recognition for 25 Years of Membership and Contributions to Electronics Manufacturing Industry
06/24/2024 | KICKIC, a renowned pioneer in thermal process and temperature measurement solutions for electronics manufacturing, is proud to announce that it has been recognized by IPC for 25 years of membership and significant contributions to electronics manufacturing.
Boeing Starliner Spacecraft Completes Successful Crewed Docking with International Space Station
06/07/2024 | BoeingNASA astronauts Barry "Butch" Wilmore and Sunita "Suni" Williams successfully docked Boeing's Starliner spacecraft to the International Space Station (ISS), about 26 hours after launching from Cape Canaveral Space Force Station.
KIC’s Miles Moreau to Present Profiling Basics and Best Practices at SMTA Wisconsin Chapter PCBA Profile Workshop
01/25/2024 | KICKIC, a renowned pioneer in thermal process and temperature measurement solutions for electronics manufacturing, announces that Miles Moreau, General Manager, will be a featured speaker at the SMTA Wisconsin Chapter In-Person PCBA Profile Workshop.
The Drive Toward UHDI and Substrates
09/20/2023 | I-Connect007 Editorial TeamPanasonic’s Darren Hitchcock spoke with the I-Connect007 Editorial Team on the complexities of moving toward ultra HDI manufacturing. As we learn in this conversation, the number of shifting constraints relative to traditional PCB fabrication is quite large and can sometimes conflict with each other.