-
- News
- Books
Featured Books
- pcb007 Magazine
Latest Issues
Current IssueInventing the Future with SEL
Two years after launching its state-of-the-art PCB facility, SEL shares lessons in vision, execution, and innovation, plus insights from industry icons and technology leaders shaping the future of PCB fabrication.
Sales: From Pitch to PO
From the first cold call to finally receiving that first purchase order, the July PCB007 Magazine breaks down some critical parts of the sales stack. To up your sales game, read on!
The Hole Truth: Via Integrity in an HDI World
From the drilled hole to registration across multiple sequential lamination cycles, to the quality of your copper plating, via reliability in an HDI world is becoming an ever-greater challenge. This month we look at “The Hole Truth,” from creating the “perfect” via to how you can assure via quality and reliability, the first time, every time.
- Articles
- Columns
- Links
- Media kit
||| MENU - pcb007 Magazine
Estimated reading time: 7 minutes
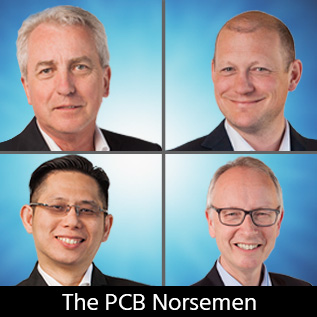
The PCB Norsemen: My Flexible Story—Flex Circuit Development Through the Decades
Social media platforms like LinkedIn and Facebook have made it simpler for all of us to remember birthdays, events, and avoid the always painful "I'm so sorry I forgot our wedding day" issue, but they also affect our professional careers. For all of us who have signed up for a LinkedIn account, you have probably found that you are celebrated every time your employment is changed. Some anniversaries are correct, while others are not. Just before Christmas, Editor Patty Goldman congratulated me for 26 years at Elmatica, which actually is correct, and asked if I could share some thoughts from my long experience in this exciting industry. Some things have changed a lot in the past few decades, but others? Not so much.
Serious Papercutting
My flex story started a few years earlier working as a rep for UK-based Flex-Ability Ltd. (now Merlin). In those days, we used purely adhesive materials, and the challenges we met and tried to solve were mechanical in most cases. My message to customers was, “Usually, we find a solution, so bring all your crazy ideas—even those you think are impossible—and we will sort it out together.”
DFM for flexible circuits became one of my favorite tasks. Every customer had special needs, and we almost always found a solution that worked for the company and our customers. A typical scenario could be a tight construction where the customer wanted a flex tail out from a ZIF connector with a sharp bend through narrow areas where no one thought a PCB could go.
You might wonder how we tested this in the old days when computer-based 3D simulations were not a possibility. Simple! We took a piece of paper, scissors, and started to cut the paper into the shape of the flexible PCB we had in mind. Next, we glued this to samples of the rigid PCB and started to simulate the application. We examined not only how it fit into the application, but we also went through the manual assembly process and found areas where the paper was torn. Then, we improved the model and made assembly notes until we were good to make a real sample. It was rough, honest, handcrafted work.
Curls and Waves in More Than ‘80s Hair
I always asked the customer to give me 3D drawings of the FPC that showed how the FPC should be used in the application. During the 1980s, many people requested semi-flexible, or bend-to-stay, circuits. Rogers introduced a material called Bendflex, and I recommended this material for applications where a single bend with no sharp folds was required.
However, this material did not receive enough attention for Rogers to continue producing it, so it was taken off the market after a decade or so. I still have not seen material with the properties we had with Bendflex unless you choose an aluminum base.
Figure 1: Elmatica has experienced increased demand for both flex and flex-rigid in the last few years.
Surviving Dynamic Movements
I remember one success story related to the early design of disc drives reading and erasing heads. I brought Steve Holding from Flex-Ability to Norway for a brainstorming meeting with our local disk drive OEMs, and we started investigating what was needed to survive dynamic movements with sufficient flexibility in combination with a new level of track width and density.
We tested out how available copper structures and grain direction affected flexibility and dynamic movements, and tuned the design and material choice to meet the required bend cycles. These early developments ended up at a global product owner and were transferred to Asia for mass volume production.
Since Day 1 of my first contact with flexible circuits and DFM, early involvement in guiding product development has been the key to success—and it still is!
Some Things Never Change
Back in the days, we created some simple design rules that I still find very useful. Some of the parameters are very conservative today, but if you want to produce a low-cost flex, these parameters still apply:
• Flexible materials are subject to slight shrinkage during the manufacturing process; thus, allowance must be made when determining minimum distances between groups of holes
• Circuit pad design should take into account a method of anchorage; this can be by pad filleting, Mickey Mouse ears, or utilizing the plating in the hole on the PTH circuits
• Ninety degree track bends should be avoided
• Route tracks between holes tangentially to gain maximum space; where possible, route these tracks on the component side and increase solderable land on the solder side
• Avoid having rectangular holes, as this can increase tooling costs; this applies to both base and overcoats
• Lands around via holes should be as large as possible
• Avoid via holes in bend areas
• Where the circuit is required to bend, tracking should follow the direction of the bend; do not track across a bend and design the circuit to be single-sided in areas with dynamic bends
• Generally, covercoat apertures should be designed to be smaller than through-hole component lands by an approximate 0.2-mm diameter; when considering the hole size in relation to the solderable land area, the same rules as those used for a rigid PCB apply
• Ground plane areas should be crosshatched to improve bondability when using copper screens, and consideration given to silver polymer-loaded inks when overall circuit thickness is critical
• All inside corners must have a radius; in these cases, a copper tear stop should be incorporated into the design as an added safety feature to guard against tearing or cracks propagating across a flexible circuit
• When routing your traces in a double-sided flex, it is best to stagger the traces to prevent an I-beam effect; with the conductors stacked, you run the risk of compression issues when bending to install
Lots of Prototyping and Testing
If you have read some of my earlier PCB Norsemen columns, you probably understood that my heart pounds for PCB standards. At Elmatica, we value transparency and predictability, and IPC standards for PCB contributes to this, aligning the industry by following the same set of guidelines.
When I started with FPCs, the focus was not on standards but tests and failures. It was all about finding the solution and having the knowledge and experience to know what was working or not. The customers relied on the suppliers to find their way around the challenges offered to them and the right solution for that exact flex circuit. The result was often a large number of prototypes and endless rounds of testing.
I remember how satisfying it was to find a solution for a customer who had been elsewhere and was ready to throw the entire project in the bin. Now, the situation is different. Being a part of the development of several IPC standards, I often get that “throwback Thursday” feeling. It’s quite funny to spot how many of our early recommendations are implemented into IPC-2223D.
Impedance: A Lesser Challenge With Improved Base Material Stability
Today, we see more and more flex circuits with controlled impedance. This was a big challenge in the ‘80s. With the adhesiveless materials we have now—with improved base material stability and thickness tolerances—signal characteristics are much more predictable than with the adhesive-based materials we had before. In fact, some of the most advanced circuits with the smallest tracks and gaps are made on flexible materials.
Figure 2: Choosing a flexible circuit offers multiple advantages; thermal management, and increased design possibilities are just two.
In my work with IPC developing a standard for medical applications, we see a trend in applications such as pacemakers and defibrillators where flexible polyimide materials are widely used. Whereas flexible design in my early flexible days (no, I was not a yoga master back then either) followed more or less the same design rules, the situation in 2019 is quite different. We see a big difference between those simple designs typically manufactured in volumes with general tolerances compared to those extreme high-end designs where dedicated state-of-the-art manufacturing equipment is required, and IPC Class 3 is barely a starting point.
Thinking in Three Dimensions Is Still Vital
In both ends of the design scale, a 3D understanding of the application is vital to provide sufficient DFM support, not to mention the specification. A complete specification (preferably digital) together with a 3D drawing is crucial to give a complete picture of the FPC and secure a product in compliance with the customer’s expectations. It was like that in the ‘80s, and it still is today. Happy flexing!
Jan Pedersen is a senior technical advisor at Elmatica.
This column was originally published in the January 2019 issue of FLEX007 Magazine.
More Columns from The PCB Norsemen
The PCB Norsemen: New Trends in the PCB Industry at productronica 2019The Laminate Market: What Will the Future Bring?
The PCB Norsemen: Avoid Failures in PCB Production With Compliance Control
The PCB Norsemen: From Wooden Huts to Homemade Go-karts—It All Starts With Design!
What Is Reliability Without Traceability?
The PCB Norsemen: Merging the Best of Both Worlds—Young Superheroes and Knowledgeable Wizards!
A PCB Broker’s Guide Through the Galaxy of Automation
The PCB Norsemen: Technology’s Future Comes Together—A Great Slogan for Us All!