-
- News
- Books
Featured Books
- pcb007 Magazine
Latest Issues
Current IssueInventing the Future with SEL
Two years after launching its state-of-the-art PCB facility, SEL shares lessons in vision, execution, and innovation, plus insights from industry icons and technology leaders shaping the future of PCB fabrication.
Sales: From Pitch to PO
From the first cold call to finally receiving that first purchase order, the July PCB007 Magazine breaks down some critical parts of the sales stack. To up your sales game, read on!
The Hole Truth: Via Integrity in an HDI World
From the drilled hole to registration across multiple sequential lamination cycles, to the quality of your copper plating, via reliability in an HDI world is becoming an ever-greater challenge. This month we look at “The Hole Truth,” from creating the “perfect” via to how you can assure via quality and reliability, the first time, every time.
- Articles
- Columns
- Links
- Media kit
||| MENU - pcb007 Magazine
Estimated reading time: 6 minutes
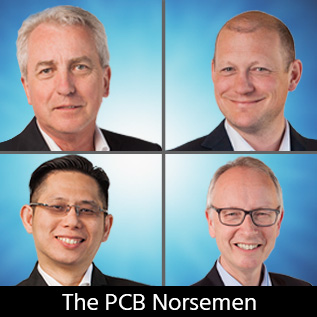
What Is Reliability Without Traceability?
High reliability and compliance are hot topics at conferences all over the world. If you are a supplier to industries like defense, automotive, medical, and aerospace/space, high-reliability and regulatory compliance are strict demands for electronic device manufacturers. For example, the automotive industry has zero-kilometer failure requirements. In the defense industry, there are full life-cycle service requirements, function on demand, and traceability throughout the entire production process plus strict compliance and origin requirements.
In this column, I will discuss how high-reliability demands enforce the need for traceability, and at what level the traceability should be. Cost is a vital part of how much we invest in reliability. In the medical world, we talk about ALARP risk, meaning “as low as reasonably practicable.” But how can we discuss a reasonable risk if life is at stake? And if we accept the risk, how can we limit the damage and cost?
Printed Board Traceability: Down to the Sheet of Base Material Used
Working with printed boards for decades, I have seen the result of how good traceability can limit the cost when a disaster occurs, and I have seen the contrary. In other words, we can turn the disaster into a problem that’s still costly and involves lots of resources but avoids the pandemic feeling.
A good example would be if a big shipment arrived at the customer’s door and they discovered when they opened and tested the boards that the PCBs had thinner copper plating than required. One’s first thought might be to return the high-cost PCB, resulting in huge claims and costs. However, with good traceability markings, we could limit those boards down to a few production panels in the PCB factory. A case like this was settled by replacing a few boards instead of having a full shipment sent back to the factory in China. Thus, the traceability saved the involved parties both time and money.
An important role of traceability in printed board production is to confirm transparency and traceability of materials, production sites, and production processes. When traceability is used for cost limitation, we must add traceability to the printed board’s position in a production panel, and a unique production printed board and panel identification. Ultimately, we should be able to trace down to the actual sheet of base material used. This level of traceability is possible today but rarely implemented. With the implementation of full connected factory control, we will soon see such traceability even down to used chemicals and other process parameters that are impossible to achieve right now.
Today, in printed board production, we accept the fact that errors occur because of the high number of complex processes and simply because humans are involved. We also know that hidden failures will escape the outgoing control. This leads us to the importance of consequence and cost limitation when the failure potentially could jeopardize function and reliability in the end product, such as life-critical medical devices.
Traceability in PCB Production: Not a Sufficient Focus
Being chair of two IPC task groups where we write performance standards for printed boards used in automotive and medical devices, traceability is frequently discussed. We experience how traceability has a focus in PCB assembly processes but is generally neglected in requirements to PCB production. Some companies understand the importance of traceability and implement different smart ways to trace one printed board back to its panel, or at least the production lot, and limit the consequential cost. Other printed board factories have implemented good systems. However, when the systems are not implemented into the performance standards, it’s left to the customers and suppliers to apply for them, and they often don’t. If the system was made mandatory in the performance standard, they would have to follow it.
Strict Requirements for Medical Devices: Not Consistent Enough
As a part of my work with the automotive and medical standards, I have learned that traceability is an area where some companies are good while others simply miss out. Very few, if any, excel. The closest are companies involved in human implant electronics. When I looked into the standard, I found the same as we see in medical electronics—the requirements are strict for the manufacturing of the medical devices, but not upstream to printed board manufacturing.
One might think that with the importance traceability offers, there would be several IPC standards describing how to handle it, but there are not. IPC-1782 is the only one describing the issue, and it is the standard for manufacturing and supply chain traceability of electronic products. Until now, this standard described traceability for electronic production, excluding the printed board. This is about to change. In the ongoing work toward a new revision, we have started to discuss how we can implement traceability for printed boards as well.
Compliance to Specification and Corporate and Regulatory Requirements
To secure traceability of compliance to product performance and requirements in an electronic device application, a computer-readable digital specification should be created during the product development process. This specifies the product requirements in all PCB procurement stages between buyer and seller through the complete product lifecycle, and encompass the parameters as written in the procurement documentation as a minimum.
It is a good habit to let the digital specification be part of the request for quotation to protect the buyer and secure that the seller has sufficient capability to meet the specified qualification and performance requirements. Such digital specification is not common today, but I am sure it will be in the near future because it is the best way to secure that all requirements are maintained through the complete supply chain.
In many industries, there are regulatory compliance requirements enforced by the country the electronic device is being employed. The most obvious is in the defense industry where traceability must show where all critical components are made. When procuring printed circuits or materials to the defense industry, there is no such thing as assuming or relying on questionable interpretations. There are no options for shortcuts whether your supplier follows the regulations or not. You must know the country of origin down to the printed circuit or material level of your products, and the bill of materials (BOM) should encompass a country of origin for every article.
Traceability: Not Just a Buzzword
In the medical industry, we have regulatory requirements from authorities such as FDA and EU Medical Device Directive. Good traceability routines are vital and can be the defining factor between failure and success, or even worse, life or death. If traceability and limitation of consequential cost are important for you, I recommend staying tuned to the development of IPC-1782 with its new revision being developed right now. From my perspective, this standard will give us an important tool, especially if you link it up to IPC-2581 and the CircuitData specification language. All of this is currently under development and will give the future an important tool to control your traceability needs. Stay tuned; we will come back with further news on this topic. For Elmatica, traceability is not a buzzword; it’s one of our three core values.
Jan Pedersen is a senior technical advisor at Elmatica.
This article was originally published in the May 2019 issue of PCB007 Magazine.
More Columns from The PCB Norsemen
The PCB Norsemen: New Trends in the PCB Industry at productronica 2019The Laminate Market: What Will the Future Bring?
The PCB Norsemen: Avoid Failures in PCB Production With Compliance Control
The PCB Norsemen: From Wooden Huts to Homemade Go-karts—It All Starts With Design!
The PCB Norsemen: Merging the Best of Both Worlds—Young Superheroes and Knowledgeable Wizards!
The PCB Norsemen: My Flexible Story—Flex Circuit Development Through the Decades
A PCB Broker’s Guide Through the Galaxy of Automation
The PCB Norsemen: Technology’s Future Comes Together—A Great Slogan for Us All!