New Way to Beat the Heat in Electronics
May 17, 2019 | Rice UniversityEstimated reading time: 3 minutes
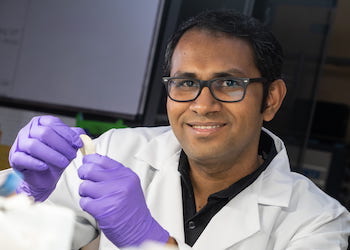
A nanocomposite invented at Rice University’s Brown School of Engineering promises to be a superior high-temperature dielectric material for flexible electronics, energy storage and electric devices.
Image Caption: Rice research scientist M.M. Rahman holds a flexible dielectric made of a polymer nanofiber layer and boron nitride. The new material stands up to high temperatures and could be ideal for flexible electronics, energy storage and electric devices where heat is a factor. Photo by Jeff Fitlow
The nanocomposite combines one-dimensional polymer nanofibers and two-dimensional boron nitride nanosheets. The nanofibers reinforce the self-assembling material while the “white graphene” nanosheets provide a thermally conductive network that allows it to withstand the heat that breaks down common dielectrics, the polarized insulators in batteries and other devices that separate positive and negative electrodes.
Research scientist M.M. Rahman and postdoctoral researcher Anand Puthirath of the Ajayan lab led the study to meet the challenge posed by next-generation electronics: Dielectrics must be thin, tough, flexible and able to withstand harsh environments.
“Ceramic is a very good dielectric, but it is mechanically brittle,” Rahman said of the common material. “On the other hand, polymer is a good dielectric with good mechanical properties, but its thermal tolerance is very low.”
Boron nitride is an electrical insulator, but happily disperses heat, he said. “When we combined the polymer nanofiber with boron nitride, we got a material that’s mechanically exceptional, and thermally and chemically very stable,” Rahman said.
The 12-to-15-micron-thick material acts as an effective heat sink up to 250 degrees Celsius (482 degrees Fahrenheit), according to the researchers. Tests showed the polymer nanofibers-boron nitride combination dispersed heat four times better than the polymer alone.
In its simplest form, a single layer of polyaramid nanofibers binds via van der Waals forces to a sprinkling of boron nitride flakes, 10% by weight of the final product. The flakes are just dense enough to form a heat-dissipating network that still allows the composite to retain its flexibility, and even foldability, while maintaining its robustness. Layering polyaramid and boron nitride can make the material thicker while still retaining flexibility, according to the researchers.
“The 1D polyaramid nanofiber has many interesting properties except thermal conductivity,” Rahman said. “And boron nitride is a very interesting 2D material right now. They both have different independent properties, but when they are together, they make something very unique.”
Rahman said the material is scalable and should be easy to incorporate into manufacturing.
From left, postdoctoral researcher Anand Puthirath, academic visitor Fanshu Yuan and research scientist M.M. Rahman show the high-temperature flexible dielectric material invented at Rice University. The three are among authors of a paper in Advanced Functional Materials that details the work. Photo by Jeff Fitlow
Co-authors of the paper are Rice academic visitors Aparna Adumbumkulath and Fanshu Yuan, alumnus Thierry Tsafack, graduate students Morgan Barnes, Zixing Wang, Sandhya Susarla, Seyed Mohammad Sajadi, Devashish Salpekar and Hossein Robatjazi, research scientist Ganguli Babu and Rafael Verduzco, an associate professor of chemical and biomolecular engineering and of materials science and nanoengineering; Sampath Kommandur and Shannon Yee of the Georgia Institute of Technology; and Kazuki Nomoto, S.M. Islam and Huili Xing of Cornell University. Ajayan is chair of Rice’s Department of Materials Science and NanoEngineering, the Benjamin M. and Mary Greenwood Anderson Professor in Engineering and a professor of chemistry.
The Army Research Laboratory funded the research.
A lab video shows how quickly heat disperses from a composite of a polymer nanoscale fiber layer and boron nitride nanosheets. When exposed to light, both materials heat up, but the plain polymer nanofiber layer on the left retains the heat far longer than the composite at right. Courtesy of the Ajayan Research Group
Suggested Items
Symposium Review: Qnity, DuPont, and Insulectro Forge Ahead with Advanced Materials
07/02/2025 | Barb Hockaday, I-Connect007In a dynamic and informative Innovation Symposium hosted live and on Zoom on June 25, 2025, representatives from Qnity (formerly DuPont Electronics), DuPont, and Insulectro discussed the evolving landscape of flexible circuit materials. From strategic corporate changes to cutting-edge polymer films, the session offered deep insight into design challenges, reliability, and next-gen solutions shaping the electronics industry.
Flexible Electronics Market to Reach $66.9 Billion by 2032, Growing at a CAGR of 9.2% from 2025
06/30/2025 | PRNewswireThe flexible electronics market is projected to reach $66.9 billion by 2032, up from an estimated $38.4 billion in 2025, growing at a robust CAGR of 9.2% during the forecast period.
All Flex Solutions Upgrades Lamination Layup
06/22/2025 | All Flex SolutionsAll Flex Solutions has invested in Ulrich Rotte lamination layup stations in their rigid flex layup area. The Ulrich Rotte stations automate the layup process by handling the lamination plates, which are heavy, and sequencing the layup process for the operators.
SEMI FlexTech Solicits Proposals for Advancing the Future of Flexible Hybrid Electronics
06/18/2025 | SEMIFlexTech, a SEMI Technology Community, today issued a Request for Proposals (RFP) to advance flexible hybrid electronics (FHE) technologies, including the development of advanced materials and additive processing.
Roll-to-Roll Technologies for Flexible Devices Set to Grow at 11.5% CAGR
06/11/2025 | GlobeNewswireAccording to the latest study from BCC Research, the “Global Markets for Roll-to-Roll Technologies for Flexible Devices” is expected to reach $69.8 billion by the end of 2029 at a compound annual growth rate (CAGR) of 11.5% from 2024 to 2029.