Ready, Jet...Print!
June 10, 2019 | KAUSTEstimated reading time: 2 minutes
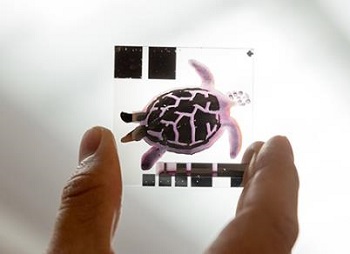
Inkjet printing is expected to fast track the commercialization of organic solar cells. Researchers from the KAUST Solar Center have exploited this technique to generate high-efficiency solar cells at large scales.
Image Caption: Daniel Corzo has developed an inkjet-printing approach to fabricate high-efficiency organic solar cells at a large scale.
Organic photovoltaic materials could soon replace inorganic semiconductors in solar-powered devices because of their lightness, flexibility and low cost. These materials are easy to modify and process in solution, which makes them highly attractive for customization and large-scale production. In particular, customized solar cell designs can be used in conjunction with other printed electronics to power a plethora of applications, such as disposable electronics, intelligent packaging, interactive printed media and lab-on-a-chip devices.
Nonfullerene acceptors are emerging materials that have helped boost the efficiency of organic solar cells close to commercialization. These components are typically blended with electron donors in a light-responsive electrochemical layer. They have proven effective for drawing the light-generated pairs of electrons and negatively charged holes apart and maintaining electric current when exposed to sunlight. However, scale-up and manufacturing challenges have hindered efforts to transfer these materials from the laboratory to industrial and consumer-ready scales.
To bridge this gap, Derya Baran and her colleagues have engineered inkjet-printable solar materials containing a nonfullerene acceptor and deposited these inks over large areas to produce photovoltaic cells. The resulting devices achieved efficiencies of six percent, which is comparable to the efficiencies of their spin-coated analogs.
Ph.D. candidate Daniel Corzo explains that inkjet printing presents several advantages over traditional spin-coating and blade-coating deposition techniques, including low material consumption and rapid design changes through digital platforms. “This enables low-cost manufacturing, patterning into complex shapes, and multilayered device fabrication without the need for multistep lithography,” he adds.
The researchers optimized the printing process by tuning the viscosity and evaporation behavior of the ink to improve both how the droplets were ejected and how they interacted with the substrate surface. According to Corzo, this optimization has provided a repeatable and commercially scalable process.
This bale of turtles is in fact a collection of inkjet-printed solar cells that show a conversion efficiency of 4.76%.
Baran’s team also fabricated high-efficiency turtle-shaped devices, demonstrating the potential for the process to be customized. “It is amazing that we can now fabricate solar cells with complex shapes at the push of a button, opening the door to a wide variety of applications,” Corzo says.
The researchers are currently developing fully printed organic solar cells and enhancing cell efficiency using higher-performance materials. They are also investigating ways to integrate the devices in modules and with other printed electronics for self-powered autonomous sensing.
Suggested Items
Symposium Review: Qnity, DuPont, and Insulectro Forge Ahead with Advanced Materials
07/02/2025 | Barb Hockaday, I-Connect007In a dynamic and informative Innovation Symposium hosted live and on Zoom on June 25, 2025, representatives from Qnity (formerly DuPont Electronics), DuPont, and Insulectro discussed the evolving landscape of flexible circuit materials. From strategic corporate changes to cutting-edge polymer films, the session offered deep insight into design challenges, reliability, and next-gen solutions shaping the electronics industry.
Indium Corporation Expert to Present on Automotive and Industrial Solder Bonding Solutions at Global Electronics Association Workshop
06/26/2025 | IndiumIndium Corporation Principal Engineer, Advanced Materials, Andy Mackie, Ph.D., MSc, will deliver a technical presentation on innovative solder bonding solutions for automotive and industrial applications at the Global Electronics A
Gorilla Circuits Elevates PCB Precision with Schmoll’s Optiflex II Alignment System
06/23/2025 | Schmoll MaschinenGorilla Circuits, a leading PCB manufacturer based in Silicon Valley, has enhanced its production capabilities with the addition of Schmoll Maschinen’s Optiflex II Post-Etch Punch system—bringing a new level of precision to multilayer board fabrication.
Day 1: Cutting Edge Insights at the EIPC Summer Conference
06/17/2025 | Pete Starkey, I-Connect007The European Institute for the PCB Community (EIPC) Summer Conference took place this year in Edinburgh, Scotland, June 3-4. This is the second of three articles on the conference. The other two cover the keynote speeches and Day 2 of the technical conference. Below is a recap of the first day’s sessions.
American Made Advocacy: Supporting the Entire PCB Ecosystem—Materials to OEMs
06/17/2025 | Shane Whiteside -- Column: American Made AdvocacyWith the addition of RTX to PCBAA’s membership roster, we now represent the interests of companies in the entire PCB ecosystem. From material providers to OEMs, the insights of our collective members help us educate, advocate, and support legislation and policy favorable to America’s microelectronics manufacturers. The industry veterans who lead these companies provide valuable perspective, and their accumulated wisdom makes us an even stronger association.