3D-Printed Device Could Help Cut Energy Bills and Carbon
June 14, 2019 | Swansea UniversityEstimated reading time: 2 minutes
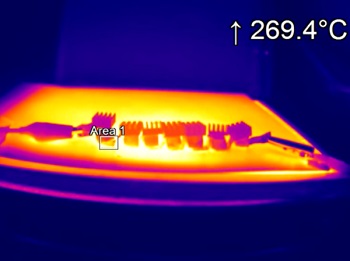
A new 3D-printed thermoelectric device, which converts heat into electric power with an efficiency factor over 50% higher than the previous best for printed materials--and is cheap to produce in bulk--has been manufactured by researchers at Swansea University’s SPECIFIC Innovation and Knowledge Centre.
Image Caption: Thermal camera image: achieving record-breaking efficiency using new printed thermoelectric material
Around one-sixth of all the energy used by industry in the UK currently ends up as waste heat, emitted into the atmosphere. Harnessing this to create electricity could be a huge step forward in helping the industry cut its energy bills and reduce its carbon footprint.
Thermoelectric materials turn differences in temperature into electric power or vice versa. They are used in fridges, power plants and even some smartwatches that are powered by body heat.
Previous research has shown that a material called tin selenide (SnSe), a compound made up of tin (Sn) and selenium (Se), has high potential as a thermoelectric material. The problem is that the methods used to manufacture it require lots of energy and are therefore expensive.
This is where the Swansea researchers’ work comes in. The technique they have developed is potentially very low-cost for industry because it enables SnSe thermoelectric generators to be produced quickly and easily in large quantities.
The team formulated tin selenide into a type of ink which they could print to test its properties. The next step was to develop a type of 3D-printing technique to produce a small thermoelectric generator made out of the ink.
The team’s experiments showed that the material gave record scores for efficiency in performance, which is measured by the “Figure of Merit” (ZT).
The Swansea team’s element achieved a ZT value (a measure of the thermoelectric generator's efficiency) of up to 1.7
The previous best ZT score for a printed thermoelectric material was 1.0
This means an efficiency rate – for turning heat into electricity - for the Swansea team’s element of around 9.5%, compared with 4.5% for the previous best
The breakthrough could be of particular benefit to industries where high temperatures are involved in the manufacturing process.
One example is steelmaking, which generates vast amounts of heat and requires immense electrical power. Recycling the heat into power, therefore, has the potential to boost energy efficiency significantly. Tata Steel is due to support a Ph.D. researcher on the team to explore the industrial application of the technology.
Printing tin selenide to turn waste heat into electrical power
The research team is from SPECIFIC Innovation and Knowledge Centre, a Swansea University-led project which develops technologies for reducing carbon emissions and demonstrates how they can be applied to buildings and industry.
Dr. Matt Carnie of Swansea University, who was lead researcher for this work, said:
“Turning waste heat into electrical power can boost energy efficiency significantly, cutting bills and reducing carbon emissions. Our findings show that printed thermoelectric materials using tin selenide are a very promising way forward.
The device we developed is the best-performing printed thermoelectric material recorded to date, with the efficiency factor improved by over 50% compared to the previous record. It is also cheap to produce in bulk compared with established manufacturing methods.
More work is needed, but already our work shows that this technique, combining efficiency and economy, could be very attractive to energy-intensive industries.”
Suggested Items
High Density Packaging User Group (HDP) Welcomes Lincstech as New Member
07/01/2025 | High Density Packaging User GroupHigh Density Packaging User Group (HDP) is pleased to announce that Lincstech Co., Ltd. (Lincstech) has become a member.
Zhen Ding's 2025 Lean & Digital Initiative Presentation Conference Concludes Successfully, Driving Group Transformation
07/01/2025 | Zhen DingTo advance its digital transformation strategy and embody the CA- PDCA continuous improvement philosophy, Zhen Ding Technology Group (Zhen Ding) successfully hosted the 2025 H1 Lean & Digital Initiative Presentation Conference.
PCBA Market to Reach $147.5 Billion by 2035, Growing at a CAGR of 4.7% from 2025
06/27/2025 | PRNewswireThe Printed Circuit Board Assembly market is projected to reach $147.5 billion by 2035, up from an estimated $90.91 billion in 2025, growing at a steady CAGR of 4.7% during the forecast period.
Summit Interconnect Participates in PCBAA Annual Meeting to Advance U.S. Electronics Policy
06/26/2025 | Summit Interconnect, Inc.Summit Interconnect was proud to participate in the 2025 Annual Meeting of the Printed Circuit Board Association of America (PCBAA), held in Washington, D.C. this June.
North American PCB Industry Sales Up 21.4% in May
06/20/2025 | IPCIPC announced the May 2025 findings from its North American Printed Circuit Board (PCB) Statistical Program. The book-to-bill ratio stands at 1.03.