Development of Flexible Hybrid Electronics
August 14, 2019 | Weifeng Liu, PhD, FlexEstimated reading time: 1 minute
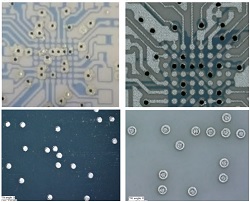
Introduction
Flexible hybrid electronics (FHE) refers to a category of flexible electronics that are made through a combination of traditional assembly process of electronic components with high-precision ink printing technologies . By integrating silicon components with printed inks and flexible substrates, FHE will revolutionize the IoT and wearable industries. With FHE, designers can create a heterogeneous electronic system that can be fully integrated with different sensors, lighter in weight, more cost effective, more flexible and conforming to the curves of a human body or even stretchable across the shape of an object or structure—all while preserving the full functionality of traditional electronic systems.
The FHE industry is still in the early stages of development, and a variety of design, material, assembly and reliability issues need to be addressed. For example, electrical interconnections formed with conductive adhesives may not be as conductive or reliable as compared to conventional solder assembly. Typical polymer-based conductive inks are not as conductive as the etched copper used to make circuit boards and they are mostly not readily solderable. Additionally, commercially available stretchable thermoplastic-based film substrates have relatively low heat resistance and cannot withstand the current lead-free reflow process temperatures.
This article will present a hybrid manufacturing process to manufacture FHE systems with a two-layer interconnect structure utilizing screen printing of silver conductive ink, filled microvias to connect ink traces at the different layers, and use of the traditional reflow process to attach the semiconductor chips to the printed substrates.
Experimental
This study is to convert a rigid multilayer wearable development platform into a flexible one using printed conductive ink and flexible substrate. The current rigid platform contains two active semiconductor components and dozens of passive devices. The largest component is the microprocessor chip. Figure 1 shows the footprint for the microprocessor chip. It is an LGA package with 8X8 array and 64 I/Os. The pad size is 250 mm and the pitch is 400 mm, which leaves the space between pads at 150 mm.
To read this entire article, which appeared in the July 2019 issue of Design007 Magazine, click here.
Testimonial
"Our marketing partnership with I-Connect007 is already delivering. Just a day after our press release went live, we received a direct inquiry about our updated products!"
Rachael Temple - AlltematedSuggested Items
Indium Corporation Promotes Two Leaders in EMEA (Europe, Middle East, and Africa) Markets
08/05/2025 | Indium CorporationWith its commitment to innovation and growth through employee development, Indium Corporation today announced the promotions of Andy Seager to Associate Director, Continental Sales (EMEA), and Karthik Vijay to Senior Technical Manager (EMEA). These advancements reflect their contributions to the company’s continued innovative efforts with customers across Europe, the Middle East, and Africa (EMEA).
MacDermid Alpha Electronics Solutions Unveils Unified Global Website to Deepen Customer, Talent, and Stakeholder Engagement
07/31/2025 | MacDermid Alpha Electronics SolutionsMacDermid Alpha Electronics Solutions, the electronics business of Elements Solutions Inc, today launched macdermidalpha.com - a unified global website built to deepen digital engagement. The launch marks a significant milestone in the business’ ongoing commitment to delivering more meaningful, interactive, and impactful experiences for its customers, talent, and stakeholders worldwide.
KOKI to Showcase Analytical Services and New HF1200 Solder Paste at SMTA Guadalajara 2025
07/31/2025 | KOKIKOKI, a global leader in advanced soldering materials and process optimization services, will exhibit at the SMTA Guadalajara Expo & Tech Forum, taking place September 17 & 18, 2025 at Expo Guadalajara, Salón Jalisco Halls D & E in Guadalajara, Mexico.
Weller Tools Supports Future Talent with Exclusive Donation to SMTA Michigan Student Soldering Competition
07/23/2025 | Weller ToolsWeller Tools, the industry leader in hand soldering solutions, is proud to announce its support of the upcoming SMTA Michigan Expo & Tech Forum by donating a limited-edition 80th Anniversary Black Soldering Set to the event’s student soldering competition.
Koh Young Appoints Tom Hattori as President of Koh Young Japan
07/21/2025 | Koh YoungKoh Young Technology, the global leader in True 3D measurement-based inspection solutions, announced the appointment of Tom Hattori as President of Koh Young Japan (JKY).