-
- News
- Books
Featured Books
- pcb007 Magazine
Latest Issues
Current IssueInventing the Future with SEL
Two years after launching its state-of-the-art PCB facility, SEL shares lessons in vision, execution, and innovation, plus insights from industry icons and technology leaders shaping the future of PCB fabrication.
Sales: From Pitch to PO
From the first cold call to finally receiving that first purchase order, the July PCB007 Magazine breaks down some critical parts of the sales stack. To up your sales game, read on!
The Hole Truth: Via Integrity in an HDI World
From the drilled hole to registration across multiple sequential lamination cycles, to the quality of your copper plating, via reliability in an HDI world is becoming an ever-greater challenge. This month we look at “The Hole Truth,” from creating the “perfect” via to how you can assure via quality and reliability, the first time, every time.
- Articles
- Columns
- Links
- Media kit
||| MENU - pcb007 Magazine
Solder Mask Curing: UV Bump Overview
August 19, 2019 | Nikolaus SchubkegelEstimated reading time: 3 minutes
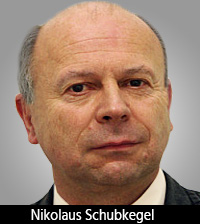
Ultraviolet (UV) bump, also called UV cure, is a processing step in which the solder mask pattern is irradiated with ultraviolet and infrared light. This step is performed with special equipment that is built as a continuous flow system. The system consists of a conveyor belt and tubular UV lamps mounted above and below the belt. The UV lamps (burners) are mounted under a hood. For safety reasons, it must be avoided that UV radiation penetrates outside because it is very dangerous for the human eye.
Typically, the light sources are powerful tubular mercury lamps with strong emissions in the UV and IR bands. It is an infrared-assisted UV exposure. UV radiation is desired, and infrared (IR) radiation is a needed side effect. Generally, the light stays constant in the system; UV energy is adjusted by varying the transportation speed of the panels. The UV energy is selected in the range between 500–4,000 mJ, depending on the solder mask and the purpose. The IR radiation will heat the PCB up to 60–70°C or more, depending on the selected UV energy and panel thickness.
Key Facts About UV Curing Systems
In general, un-doped burners are used. Iron-doped burners can also be used; then, less energy is needed. Almost all equipment is equipped with un-doped burners, which is historical. These types of equipment are used in many industries for curing of paints and inks. The un-doped lamps fit for almost all requirements. On request, the un-doped burners can be replaced with doped burners. In the PCB industry, iron-doped lamps are generally used; in other industries, it can also be gallium-doped lamps.
Depending on the solder mask (see later for further discussion), UV bump is performed either before final thermal cure or after final thermal cure of the liquid photoimageable solder resist.
Energy Levels Required for UV Cure
Generally, UV bump before the final thermal cure is performed at a lower energy (500–2,000 mJ) in comparison to UV bump after final thermal cure (1,500–4,000 mJ). UV bumping of flexible solder mask is carried out at much lower energy than for rigid products. And exposing the solder mask pattern on a contact exposing machine with a blank glass is not UV bump, even at extremely high exposing energy.
UV Cure Before the Final Thermal Cure
As the solder mask heats to temperatures beyond the glass transition temperature (Tg) of that solder mask (the Tg of the solder mask after exposure and developing is lower and different to the final Tg), the solder mask particles will become movable. As the particles move, cross-linking continues, the remaining photoinitiator is destroyed, and volatile components (solvents) are blown out. Also, the surface hardness increases, and the volatile emissions reduce. Furthermore, condensation in the final cure oven is reduced. The chemical resistance to different final finishes (e.g., immersion tin, ENIG, and HASL) and cleaning processes is improved. Moisture absorption is reduced. In short, after direct imaging, it contributes to sealing of the surface. The disadvantage of UV bump before the final thermal cure is the risk of over cross-linking and embrittlement. This happens if the energy is far higher than required and if the system is not closely monitored. The adhesion of legend ink and the adhesion of conformal coating might be reduced.
UV Cure After the Final Thermal Cure
The temperature of the solder mask stays below the Tg. The additional cross-linking can be neglected; the molecules swing only on fixed points, and the movement of the particles is limited. The remaining photoinitiator is destroyed and blown out. Residues condensed on the copper surface from the final curing oven are being destroyed by photo-oxidation and oxidation with ozone. The remained volatiles are blown out; these volatiles might condense on copper and lead to plating defects in ENIG.
Moreover, the resistance to different final finishes is improved, and the absorption of moisture is reduced. Staining after HAL and after wave soldering is also reduced. The ionic contamination and the out-gassing improves significantly as well. And the adhesion of legend ink and conformal coating might be reduced.
To read the full article, which appeared in the August 2019 issue of PCB007 Magazine, click here.
Testimonial
"Advertising in PCB007 Magazine has been a great way to showcase our bare board testers to the right audience. The I-Connect007 team makes the process smooth and professional. We’re proud to be featured in such a trusted publication."
Klaus Koziol - atgSuggested Items
Indium Corporation Promotes Two Leaders in EMEA (Europe, Middle East, and Africa) Markets
08/05/2025 | Indium CorporationWith its commitment to innovation and growth through employee development, Indium Corporation today announced the promotions of Andy Seager to Associate Director, Continental Sales (EMEA), and Karthik Vijay to Senior Technical Manager (EMEA). These advancements reflect their contributions to the company’s continued innovative efforts with customers across Europe, the Middle East, and Africa (EMEA).
MacDermid Alpha Electronics Solutions Unveils Unified Global Website to Deepen Customer, Talent, and Stakeholder Engagement
07/31/2025 | MacDermid Alpha Electronics SolutionsMacDermid Alpha Electronics Solutions, the electronics business of Elements Solutions Inc, today launched macdermidalpha.com - a unified global website built to deepen digital engagement. The launch marks a significant milestone in the business’ ongoing commitment to delivering more meaningful, interactive, and impactful experiences for its customers, talent, and stakeholders worldwide.
KOKI to Showcase Analytical Services and New HF1200 Solder Paste at SMTA Guadalajara 2025
07/31/2025 | KOKIKOKI, a global leader in advanced soldering materials and process optimization services, will exhibit at the SMTA Guadalajara Expo & Tech Forum, taking place September 17 & 18, 2025 at Expo Guadalajara, Salón Jalisco Halls D & E in Guadalajara, Mexico.
Weller Tools Supports Future Talent with Exclusive Donation to SMTA Michigan Student Soldering Competition
07/23/2025 | Weller ToolsWeller Tools, the industry leader in hand soldering solutions, is proud to announce its support of the upcoming SMTA Michigan Expo & Tech Forum by donating a limited-edition 80th Anniversary Black Soldering Set to the event’s student soldering competition.
Koh Young Appoints Tom Hattori as President of Koh Young Japan
07/21/2025 | Koh YoungKoh Young Technology, the global leader in True 3D measurement-based inspection solutions, announced the appointment of Tom Hattori as President of Koh Young Japan (JKY).