MIT Engineers Build Advanced Microprocessor out of Carbon Nanotubes
August 28, 2019 | MITEstimated reading time: 6 minutes
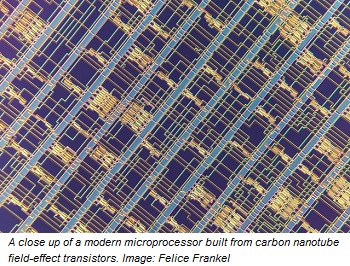
After years of tackling numerous design and manufacturing challenges, MIT researchers have built a modern microprocessor from carbon nanotube transistors, which are widely seen as a faster, greener alternative to their traditional silicon counterparts.
The microprocessor, described today in the journal Nature, can be built using traditional silicon-chip fabrication processes, representing a major step toward making carbon nanotube microprocessors more practical.
Silicon transistors — critical microprocessor components that switch between 1 and 0 bits to carry out computations — have carried the computer industry for decades. As predicted by Moore’s Law, industry has been able to shrink down and cram more transistors onto chips every couple of years to help carry out increasingly complex computations. But experts now foresee a time when silicon transistors will stop shrinking, and become increasingly inefficient.
Making carbon nanotube field-effect transistors (CNFET) has become a major goal for building next-generation computers. Research indicates CNFETs have properties that promise around 10 times the energy efficiency and far greater speeds compared to silicon. But when fabricated at scale, the transistors often come with many defects that affect performance, so they remain impractical.
The MIT researchers have invented new techniques to dramatically limit defects and enable full functional control in fabricating CNFETs, using processes in traditional silicon chip foundries. They demonstrated a 16-bit microprocessor with more than 14,000 CNFETs that performs the same tasks as commercial microprocessors. The Nature paper describes the microprocessor design and includes more than 70 pages detailing the manufacturing methodology.
The microprocessor is based on the RISC-V open-source chip architecture that has a set of instructions that a microprocessor can execute. The researchers’ microprocessor was able to execute the full set of instructions accurately. It also executed a modified version of the classic “Hello, World!” program, printing out, “Hello, World! I am RV16XNano, made from CNTs.”
“This is by far the most advanced chip made from any emerging nanotechnology that is promising for high-performance and energy-efficient computing,” says co-author Max M. Shulaker, the Emanuel E Landsman Career Development Assistant Professor of Electrical Engineering and Computer Science (EECS) and a member of the Microsystems Technology Laboratories. “There are limits to silicon. If we want to continue to have gains in computing, carbon nanotubes represent one of the most promising ways to overcome those limits. [The paper] completely re-invents how we build chips with carbon nanotubes.”
Joining Shulaker on the paper are: first author and postdoc Gage Hills, graduate students Christian Lau, Andrew Wright, Mindy D. Bishop, Tathagata Srimani, Pritpal Kanhaiya, Rebecca Ho, and Aya Amer, all of EECS; Arvind, the Johnson Professor of Computer Science and Engineering and a researcher in the Computer Science and Artificial Intelligence Laboratory; Anantha Chandrakasan, the dean of the School of Engineering and the Vannevar Bush Professor of Electrical Engineering and Computer Science; and Samuel Fuller, Yosi Stein, and Denis Murphy, all of Analog Devices.
Fighting the “bane” of CNFETs
The microprocessor builds on a previous iteration designed by Shulaker and other researchers six years ago that had only 178 CNFETs and ran on a single bit of data. Since then, Shulaker and his MIT colleagues have tackled three specific challenges in producing the devices: material defects, manufacturing defects, and functional issues. Hills did the bulk of the microprocessor design, while Lau handled most of the manufacturing.
For years, the defects intrinsic to carbon nanotubes have been a “bane of the field,” Shulaker says. Ideally, CNFETs need semiconducting properties to switch their conductivity on an off, corresponding to the bits 1 and 0. But unavoidably, a small portion of carbon nanotubes will be metallic, and will slow or stop the transistor from switching. To be robust to those failures, advanced circuits will need carbon nanotubes at around 99.999999 percent purity, which is virtually impossible to produce today.
The researchers came up with a technique called DREAM (an acronym for “designing resiliency against metallic CNTs”), which positions metallic CNFETs in a way that they won’t disrupt computing. In doing so, they relaxed that stringent purity requirement by around four orders of magnitude — or 10,000 times — meaning they only need carbon nanotubes at about 99.99 percent purity, which is currently possible.
Designing circuits basically requires a library of different logic gates attached to transistors that can be combined to, say, create adders and multipliers — like combining letters in the alphabet to create words. The researchers realized that the metallic carbon nanotubes impacted different pairings of these gates differently. A single metallic carbon nanotube in gate A, for instance, may break the connection between A and B. But several metallic carbon nanotubes in gates B may not impact any of its connections.
In chip design, there are many ways to implement code onto a circuit. The researchers ran simulations to find all the different gate combinations that would be robust and wouldn’t be robust to any metallic carbon nanotubes. They then customized a chip-design program to automatically learn the combinations least likely to be affected by metallic carbon nanotubes. When designing a new chip, the program will only utilize the robust combinations and ignore the vulnerable combinations.
“The ‘DREAM’ pun is very much intended, because it’s the dream solution,” Shulaker says. “This allows us to buy carbon nanotubes off the shelf, drop them onto a wafer, and just build our circuit like normal, without doing anything else special.”
Page 1 of 2
Suggested Items
Rules of Thumb: Design007 Magazine, November 2024
11/11/2024 | I-Connect007 Editorial TeamRules of thumb are everywhere, but there may be hundreds of rules of thumb for PCB design. They’re built on design formulas, fabricators’ limitations, and tribal knowledge. And unfortunately, some longtime rules of thumb should be avoided at all costs. How do we separate the wheat from the chaff, so to speak?
Connect the Dots: Best Practices for Prototyping
09/21/2023 | Matt Stevenson -- Column: Connect the DotsPCB prototyping is a critical juncture during an electronic device’s journey from concept to reality. Regardless of a project’s complexity, the process of transforming a design into a working board is often enlightening in terms of how a design can be improved before a PCB is ready for full production.
The Drive Toward UHDI and Substrates
09/20/2023 | I-Connect007 Editorial TeamPanasonic’s Darren Hitchcock spoke with the I-Connect007 Editorial Team on the complexities of moving toward ultra HDI manufacturing. As we learn in this conversation, the number of shifting constraints relative to traditional PCB fabrication is quite large and can sometimes conflict with each other.
Asia/Pacific AI Spending Surge to Reach a Projected $78 Billion by 2027
09/19/2023 | IDCAsia/Pacific spending on Artificial Intelligence (AI) ), including software, services, and hardware for AI-centric systems will grow to $78.4 billion in 2027, according to International Data Corporation's latest Worldwide Artificial Intelligence Spending Guide.
Intel to Sell Minority Stake in IMS Nanofabrication Business to TSMC
09/13/2023 | IntelIntel Corporation announced that it has agreed to sell an approximately 10% stake in the IMS Nanofabrication business to TSMC. TSMC’s investment values IMS at approximately $4.3 billion, consistent with the valuation of the recent stake sale to Bain Capital Special Situations.