New Method for the Measurement of Nano-Structured Light Fields
September 23, 2019 | University of MünsterEstimated reading time: 1 minute
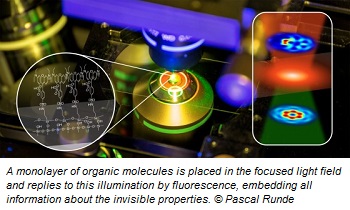
Structured laser light has already opened up various different applications: it allows for precise material machining, trapping, manipulating or defined movement of small particles or cell compartments, as well as increasing the bandwidth for next-generation intelligent computing.
If these light structures are tightly focused by a lens, like a magnifying glass used as burning glass, highly intense three-dimensional light landscapes will be shaped, facilitating a significantly enhanced resolution in named applications. These kinds of light landscapes has paved the way to pioneering applications as Nobel prize awarded STED microscopy.
However, these nano-fields itself could not be measured yet, since components are formed by tight focusing which are invisible for typical measurement techniques. Up to now, this lack of appropriate metrological methods has impeded the breakthrough of nano-structured light landscapes as a tool for material machining, optical tweezers, or high-resolution imaging.
A team around physicist Prof. Dr. Cornelia Denz of the Institute of Applied Physics and chemist Prof. Dr. Bart Jan Ravoo of the Center for Soft Nanoscience (SoN) at the University of Münster successfully developed a nano-tomographic technique which is able to detect the typically invisible properties of nano-structured fields in the focus of a lens – without requiring any complex analysis algorithms or data post-processing. For this purpose, the team combined their knowledge in the field of nano-optics and organic chemistry to realize an approach based on a monolayer of organic molecules. This monolayer is placed in the focused light field and replies to this illumination by fluorescence, embedding all information about the invisible properties.
By the detection of this reply the distinct identification of the nano-field by a single, fast and straightforward camera image is enabled. “This approach finally opens the till now unexploited potential of these nano-structured light landscapes for many more applications,” says Cornelia Denz, who is heading the study. The study has been published in the journal “Nature Communications”.
Suggested Items
Driving Innovation: Direct Imaging vs. Conventional Exposure
07/01/2025 | Simon Khesin -- Column: Driving InnovationMy first camera used Kodak film. I even experimented with developing photos in the bathroom, though I usually dropped the film off at a Kodak center and received the prints two weeks later, only to discover that some images were out of focus or poorly framed. Today, every smartphone contains a high-quality camera capable of producing stunning images instantly.
United Electronics Corporation Advances Manufacturing Capabilities with Schmoll MDI-ST Imaging Equipment
06/24/2025 | United Electronics CorporationUnited Electronics Corporation has successfully installed the advanced Schmoll MDI-ST (XL) imaging equipment at their advanced printed circuit board facility. This significant technology investment represents a continued commitment to delivering superior products and maintaining their position as an industry leader in precision PCB manufacturing.
Orbel Corporation Integrates Schmoll Direct Imaging
06/04/2025 | Schmoll AmericaOrbel Corporation in Easton, PA, proudly becomes the first PCM facility in the U.S. equipped with Schmoll’s MDI Direct Imaging system. This installation empowers Orbel to support customers with greater precision and quality.
Key Insights on Photoresist for Defect Reduction
05/21/2025 | I-Connect007 Editorial TeamIn PCB manufacturing, understanding the intricacies of the photoresist process is crucial for achieving high-quality results. Industry experts Josh Krick, a technical service engineer at IEC, and Tim Blair, a PCB imaging specialist at Tim Blair LLC, share their knowledge on the essential stages of photoresist application, highlight critical advancements in materials, and discuss common defects encountered during production. They share best practices and innovative solutions to enhance the manufacturing process, reduce defects, and ensure efficiency and reliability in high-tech applications.
NXP Unveils Third-Generation Imaging Radar Processors for Level 2+ to 4 Autonomous Driving
05/09/2025 | NXP SemiconductorNXP Semiconductors N.V. unveiled its new S32R47 imaging radar processors in 16 nm FinFET technology, building on NXP’s proven expertise in the imaging radar space.