Silicon Technology Boost with Graphene and 2D Materials
October 1, 2019 | ICFOEstimated reading time: 2 minutes
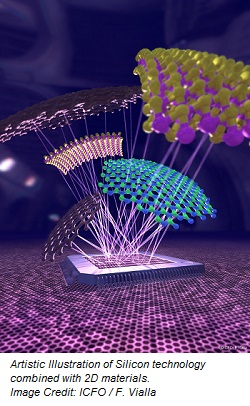
Silicon semiconductor technology has done marvels for the advancement of our society, who has benefited tremendously from its versatile use and amazing capabilities. The development of electronics, automation, computers, digital cameras and recent smartphones based on this material and its underpinning technology has reached skyrocket limits, downscaling the physical size of devices and wires to the nanometre regime.
Although this technology has been developing since the late 1960s, the miniaturization of circuits seems to have reached a possible halt, since transistors can only be shrunk down to a certain size and not further beyond. Thus, there is a pressing need to complement Si CMOS technology with new materials, and fulfil the future computing requirements as well as the needs for diversification of applications.
Now, graphene and related two-dimensional (2D) materials offer prospects of unprecedented advances in device performance at the atomic limit. Their amazing potential has proven to be a possible solution to overcome the limitations of silicon technology, where the combination of 2D materials with silicon chips promises to surpass the current technological limitations.
In the new review article in Nature, a team of international researchers including ICFO researchers Dr. Stijn Goossens and ICREA Prof at ICFO Frank Koppens, and industrial leaders from IMEC and TSMC have come together to provide an in-depth and thorough review about the opportunities, progress and challenges of integrating atomically thin materials with Si-based technology. They give insights on how and why 2D materials (2DMs) could overcome current challenges posed by the existing technology and how they can enhance both device component function and performance, to boost the features of future technologies, in the areas of computational and non-computational applications.
For non-computational applications, they review the possible integration of these materials for future cameras, low power optical data communications and gas and bio-sensors. In particular, image sensors and photodetectors, where graphene and 2DMs could enable a new vision in the infrared and terahertz range in addition to the visible range of the spectrum. These can serve for example in autonomous vehicle, security at airports and augmented reality.
For computational systems, and in particular in the field of transistors, they show how challenges such as doping, contact resistance and dielectrics/encapsulation can be diminished when integrating 2DMs with Si technology. 2DMs could also radically improve memory and data storage devices with novel switching mechanisms for meta-insulator-metal structures, avoid sneak currents in memory arrays, or even push performance gains of copper wired based circuitry by adhering graphene to the ultrathin copper barrier materials and thus reduce resistance, scattering and self-heating.
The review provides insight to all stakeholders about the challenges and impact of solving the 2D material integration with CMOS technology. It provides a roadmap of 2D integration and CMOS technology, pinpointing the stage at which all challenges regarding growth, transfer, interface, doping, contacting, and design are currently standing today and what possible processes are expected to be resolved to achieve such goals of moving from a research laboratory environment to a pilot line for production of the first devices that combine both technologies.
The first 2D material-CMOS roadmap, as presented in this review, gives an exciting glimpse in the future, with first pilot production to be expected already in just a few years from now.
Suggested Items
Trump Copper Tariffs Spark Concern
07/10/2025 | I-Connect007 Editorial TeamPresident Donald Trump stated on July 8 that he plans to impose a 50% tariff on copper imports, sparking concern in a global industry whose output is critical to electric vehicles, military hardware, semiconductors, and a wide range of consumer goods. According to Yahoo Finance, copper futures climbed over 2% following tariff confirmation.
Happy’s Tech Talk #40: Factors in PTH Reliability—Hole Voids
07/09/2025 | Happy Holden -- Column: Happy’s Tech TalkWhen we consider via reliability, the major contributing factors are typically processing deviations. These can be subtle and not always visible. One particularly insightful column was by Mike Carano, “Causes of Plating Voids, Pre-electroless Copper,” where he outlined some of the possible causes of hole defects for both plated through-hole (PTH) and blind vias.
Trouble in Your Tank: Can You Drill the Perfect Hole?
07/07/2025 | Michael Carano -- Column: Trouble in Your TankIn the movie “Friday Night Lights,” the head football coach (played by Billy Bob Thornton) addresses his high school football team on a hot day in August in West Texas. He asks his players one question: “Can you be perfect?” That is an interesting question, in football and the printed circuit board fabrication world, where being perfect is somewhat elusive. When it comes to mechanical drilling and via formation, can you drill the perfect hole time after time?
The Evolution of Picosecond Laser Drilling
06/19/2025 | Marcy LaRont, PCB007 MagazineIs it hard to imagine a single laser pulse reduced not only from nanoseconds to picoseconds in its pulse duration, but even to femtoseconds? Well, buckle up because it seems we are there. In this interview, Dr. Stefan Rung, technical director of laser machines at Schmoll Maschinen GmbH, traces the technology trajectory of the laser drill from the CO2 laser to cutting-edge picosecond and hybrid laser drilling systems, highlighting the benefits and limitations of each method, and demonstrating how laser innovations are shaping the future of PCB fabrication.
Day 2: More Cutting-edge Insights at the EIPC Summer Conference
06/18/2025 | Pete Starkey, I-Connect007The European Institute for the PCB Community (EIPC) summer conference took place this year in Edinburgh, Scotland, June 3-4. This is the third of three articles on the conference. The other two cover Day 1’s sessions and the opening keynote speech. Below is a recap of the second day’s sessions.