Energy Efficient Power Electronics—Gallium Oxide Power Transistors with Record Levels
October 2, 2019 | FBHEstimated reading time: 1 minute
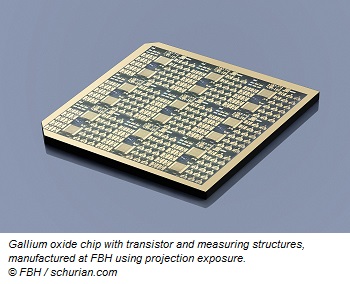
With as little space as possible, they should be able to achieve ever higher power densities with low energy consumption and thus work more efficiently. Conventional components reach their limits here. As a result, scientists around the world are researching novel materials and components that meet these requirements. The Ferdinand Braun Institute, Leibniz Institute for High Frequency Technology (FBH) has now achieved a breakthrough with transistors based on gallium oxide (ß-Ga2O3).
The newly developed ß-Ga2O3 MOSFETs (dt. Metal-oxide-semiconductor field effect transistor) provide a high breakdown voltage with high current conductivity. With 1.8 kilovolts of breakdown voltage and a record output of 155 megawatts per square centimeter, they achieve unique global metrics close to the theoretical material limit of gallium oxide. At the same time, the breakthrough field strengths achieved are far greater than those of established large band gap semiconductors such as silicon carbide or gallium nitride.
Optimized layer structure and gate topology
To achieve these improvements, the FBH team started on the layer structure and the gate topology. The basis was provided by substrates from the Leibniz Institute for Crystal Growth (IKZ) with an optimized epitaxial layer structure. This reduced the defect density and improved the electrical properties. This leads to lower resistances when switched on. The gate is the central "switching point" in field effect transistors, which is controlled by the gate-source voltage. Its topology has been further developed so that the high field strengths at the gate edge could be reduced. This in turn leads to higher breakdown voltages.
Suggested Items
Gorilla Circuits Elevates PCB Precision with Schmoll’s Optiflex II Alignment System
06/23/2025 | Schmoll MaschinenGorilla Circuits, a leading PCB manufacturer based in Silicon Valley, has enhanced its production capabilities with the addition of Schmoll Maschinen’s Optiflex II Post-Etch Punch system—bringing a new level of precision to multilayer board fabrication.
Sierra Circuits Boosts High Precision PCB Manufacturing with Schmoll Technology
06/16/2025 | Schmoll MaschinenSierra Circuits has seen increased success in production of multilayer HDI boards and high-speed signal architectures through the integration of a range of Schmoll Maschinen systems. The company’s current setup includes four MXY-6 drilling machines, two LM2 routing models, and a semi-automatic Optiflex II innerlayer punch.
Elementary, Mr. Watson: PCB Routing: The Art—and Science—of Connection
06/11/2025 | John Watson -- Column: Elementary, Mr. WatsonMany people who design circuit boards love the routing part of the design. This is partially because we want to stop looking at the annoying rat's nest of connections, which seem to have no rhyme or reason at first glance. We want to get to something more exciting. Routing is the ultimate part of solving the puzzle. You take all the messy lines from the schematic and turn them into neat, organized paths.
Connect the Dots: Proactive Controlled Impedance
05/29/2025 | Matt Stevenson -- Column: Connect the DotsFrom data centers to smartphones, designers know that the ohms have it. Getting impedance right ensures all-important signal integrity and delivers high-performing boards. Our designers understand the importance of controlled impedance, but not everyone addresses it in their designs. The most common and important controlled impedance types we see include microstrip, stripline, embedded microstrip, and differential pairs.
Driving Innovation: Traceability in PCB Production
05/29/2025 | Kurt Palmer -- Column: Driving InnovationTraceability across the entire printed circuit board production process is an increasingly important topic among established manufacturers and companies considering new PCB facilities. The reasons are apparent: Automatic loading of part programs, connection with MES systems and collection of production data, and compliance with Industry 4.0 requirements