Cooling Nanotube Resonators With Electrons
October 8, 2019 | ICFOEstimated reading time: 2 minutes
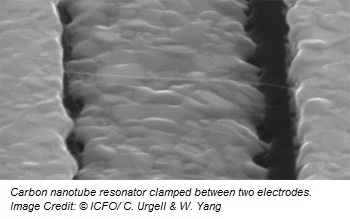
In a study in Nature Physics, ICFO researchers report on a technique that uses electron transport to cool a nanomechanical resonator near the quantum regime. Mechanical resonators have been used with great success as new resources in quantum technology. Carbon nanotube mechanical resonators have shown to be excellent ultra-high sensitive devices for the study of new physical phenomena at the nanoscale (e.g. spin physics, quantum electron transport, surface science, and light-matter interaction).
Mechanical resonators are often used to observe and manipulate the quantum states of the motion of relatively large systems. However, the drawback lies in the thermal noise force, which, if not controlled properly, ends up diluting any possibility of observing the quantum effects. Thus, scientists have been seeking for effective methods to cool down these systems down to the quantum regime and be able to observe quantum effects on demand. One of these approaches has been to use the transport of electrons along the resonator to cool down the system.
Many theoretical schemes have been proposed to cool these mechanical resonators using different electron transport regimes, but experimental difficulties have made it extremely challenging in terms of device fabrication and measurement. Despite many efforts, only one experimental realization of cooling was reported over a decade ago, in which researchers were able to cool down the system to a population number of 200 quanta, which is far from the quantum regime.
Now, in a new study published in Nature Physics, ICFO researchers Carles Urgell, Wei Yang, Sergio Lucio de Bonis, and Chandan Samanta, led by ICFO Prof. Adrian Bachtold, in collaboration with researchers from ICN2 in Barcelona and CNRS in France, have been able to demonstrate an experiment in which they cool down a nanomechanical resonator to 4.6 +/- 2.0 quanta of vibration.
In their study, the team fabricated the resonator by growing a carbon nanotube between two electrodes, where in the last step of the fabrication process, they employed a chemical vapor deposition method to minimize any possible residual contaminant on the device. Then they inserted the system in a dilution refrigerator and cooled it down to 70 mK. The novelty of their technique lied in applying a constant current of electrons through the resonator. When a constant current was applied to the resonator, the electrostatic force of the electrons impacts the dynamics of the vibrations. These modified vibrations react back on the electrons, making a closed loop with a finite delay. This back-action of the electrons on the vibrations can be used to amplify or reduce the thermal vibration fluctuations. In the latter case, they used it to cool down the system to reduce the thermal displacement fluctuations, allowing them to approach the quantum regime limit mentioned before, with a population number never reached before when compared to previous work.
The results of the study have confirmed this method to be an excellent and very simple way to cool down nanomechanical resonators, which could be of utmost importance to scientists working in nanomechanics and quantum electron transport since it will become a powerful resource for quantum manipulation of mechanical resonators.
Suggested Items
Nolan’s Notes: Moving Forward With Confidence
06/03/2025 | Nolan Johnson -- Column: Nolan's NotesWe’re currently enjoying a revitalized and dynamic EMS provider market with significant growth potential. Since December 2024, the book-to-bill has been extremely strong and growing. Starting with a ratio of 1.24 in December, book-to-bill has continued to accelerate to a 1.41 in April. Yet, there is a global economic restructuring taking place. To say that the back-and-forth with tariffs and trade deals makes for an uncertain market is an understatement. While we may be in a 90-day tariff pause among leading economic nations, the deadline is quickly approaching and that leaves many of you feeling unsettled about what to expect.
Mycronic High Flex Changes Division Name to PCB Assembly Solutions
05/20/2025 | MycronicMycronic AB, the leading Sweden-based electronics assembly solutions provider, announced that its division formerly known as High Flex will now operate under the name PCB Assembly Solutions.
SolderKing Achieves the Prestigious King’s Award for Enterprise in International Trade
05/06/2025 | SolderKingSolderKing Assembly Materials Ltd, a leading British manufacturer of high-performance soldering materials and consumables, has been honoured with a King’s Award for Enterprise, one of the UK’s most respected business honours.
Foxconn's Tiger Leap Combining Nature and Technology in Ecological Roof Garden
04/23/2025 | FoxconnHon Hai Technology Group, the world's largest technology manufacturing and service provider, has actively responded to the United Nations Sustainable Development Goals (SDGs).
IDTechEx Highlights Recyclable Materials for PCBs
04/10/2025 | IDTechExConventional printed circuit board (PCB) manufacturing is wasteful, harmful to the environment and energy intensive. This can be mitigated by the implementation of new recyclable materials and technologies, which have the potential to revolutionize electronics manufacturing.