ODB++: Transforming Ideas Into Products
October 9, 2019 | Max Clark, Mentor, a Siemens BusinessEstimated reading time: 1 minute
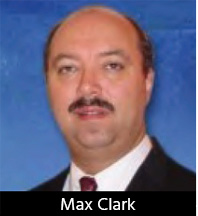
This year, I witnessed an impressive natural event that I had never experienced before in all my life as a native Californian. The painted lady butterfly migration starts from the southeastern deserts of California heading northwest to Oregon, Washington, and further north into Alaska. While that distance covered by a butterfly with a wingspan of 2–3 inches is amazing, what was so impressive was the sheer number of them. This year’s migration represented one billion butterflies, all striving to survive the long journey north. Throughout California, one could simply step outside to witness the most elegant stream of butterflies, one after the other, for days on end.
What does a butterfly migration have to do with transferring intelligent PCB data from design through the manufacturing process? The process of transforming from an earthbound caterpillar into a beautiful flying butterfly where each has a unique wing pattern is not much different than transforming an idea for a product into a schematic, and through hard work, into a unique PCB design. The difference is that nature has created a perfectly connected process, but we still are challenged doing our same process repeatedly with positive results. In the case of a PCB design, the transfer of the design intent and the manufacturing process needs are not yet connected in unison.
The ODB format originated with the objective of delivering on this need. The format was originally introduced for use by PCB fabricators, eliminating the need for a collection of CAM files in multiple formats—such as Gerber, Excellon, IPC-356, or even IPC-350, which was an early attempt to simplify this process. The key to the success of ODB was that it obtained industry acceptance. There was a friendly, informal group working together as early adopters put aside their previous thinking in the hopes of achieving a quick transformation from an effective product model into a deliverable PCB with the minimal amount of data manipulation possible, and in an effective, repeatable, and reliable manner.
To read this entire article, which appeared in the September 2019 issue of Design007 Magazine, click here.
Suggested Items
Hon Hai Education Foundation Continues to Promote Quantum Education
07/04/2025 | FoxconnHon Hai Education Foundation has long been committed to promoting forward-looking technology education in Taiwan's high schools, and held the "High School Quantum Teacher Training Camp" in Tainan City on July 1.
Incap UK Achieves JOSCAR Zero Accreditation
07/04/2025 | IncapIncap Electronics UK has been accredited under JOSCAR Zero, a new sustainability-focused extension of the defence and aerospace sector’s supplier assurance system.
Kitron Secures Contract for Components Supporting Unmanned Aerial Systems
07/04/2025 | KitronKitron has received a contract with an estimated value between EUR 4 and 8 million for the production and supply of advanced electronic components used in unmanned aerial systems (UAS).
NOTE Receives Order Worth 132 MSEK and Expands Collaboration with Customer within Security & Defense
07/04/2025 | NOTENOTE has received an order worth SEK 132 million from one of its existing customers operating within Security & Defense. NOTE thereby strengthens its long-term collaboration with the industry-leading customer.
Delta SEA Partner Event 2025 Unites Regional Partners to Embrace a “Future Ready” Vision
07/03/2025 | Delta ElectronicsDelta Electronics (Thailand) Public Company Limited, successfully hosted its Delta SEA Partner Event 2025: Future Ready at Delta Chungli Plant 5, Taiwan on June 10 – 11 , 2025.