-
- News
- Books
Featured Books
- pcb007 Magazine
Latest Issues
Current IssueInventing the Future with SEL
Two years after launching its state-of-the-art PCB facility, SEL shares lessons in vision, execution, and innovation, plus insights from industry icons and technology leaders shaping the future of PCB fabrication.
Sales: From Pitch to PO
From the first cold call to finally receiving that first purchase order, the July PCB007 Magazine breaks down some critical parts of the sales stack. To up your sales game, read on!
The Hole Truth: Via Integrity in an HDI World
From the drilled hole to registration across multiple sequential lamination cycles, to the quality of your copper plating, via reliability in an HDI world is becoming an ever-greater challenge. This month we look at “The Hole Truth,” from creating the “perfect” via to how you can assure via quality and reliability, the first time, every time.
- Articles
- Columns
- Links
- Media kit
||| MENU - pcb007 Magazine
Additive Electronics Conference Set for October 2019 Debut
October 15, 2019 | Kelly DackEstimated reading time: 9 minutes
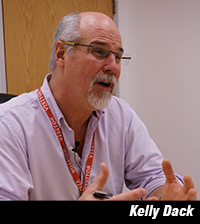
Kelly Dack and Tara Dunn talk about the upcoming conference "Additive Electronics: PCB Scale to IC Scale" on October 24, 2019, hosted by SMTA in San Jose, California, and why it’s an important event for people to attend—especially those involved in the design process.
Kelly Dack: I’ve heard a lot recently about additive electronics, and I’m familiar with the subject only from the standpoint of 3D printers layering up different materials, including conductive materials. But a couple of weeks ago, I reconnected with Tara Dunn who talked to me about the Additive Electronics Conference that’s coming up, which will cover a very different realm. My perception was that this particular context of additive electronics is more of a micro-scale take on finished copper. We discussed seeing copper on a very small scale, which can build circuitry in the range of three-thousandths of an inch all the way down to five microns. I am excited and want to know more about it. Tara, can you tell us what this conference is about?
Tara Dunn: We’re looking for different options to attack the market segment that is sub-75-micron trace and space all the way down to the 5-micron trace-and-space range. This is that gap area between PCB manufacturing and IC fabrication.
Dack: That’s sounds very interesting. Would this be considered cutting-edge or uncharted territory for most PCB designers and engineers?
Dunn: Definitely. People being introduced to the technology will often ask, “What are the design rules?” The blunt answer is there are really aren’t design rules just yet; everything is still developing quickly, and the designs tend to be much more collaborative than we’re used to with traditional PCB design rules. For instance, somebody may come to us and say, “I have this idea, I need this type of material, and I’m trying to accomplish this. How can we go about it?” Tt becomes a brainstorming session. How can we use the technology that we have today in different ways to figure out how to solve the problem?
One of the things we’re hoping to do at the conference is spark a lot of ideas. We want to provide a lot of opportunities for people to let their imagination kick into gear and think, “This person is using this technology this way; how might I be able to apply that?” We want it to be very interactive.
Dack: This is a really good subject for designers. As a designer myself, and having designed lots and lots of flex circuitry, I have learned what you can’t do by making mistakes—especially with copper. Over the years, a designer learns that there are types of processed copper. The copper thickness and grain structure must be considered along with conductor layer topology. Trace or conductor widths are critical not only in considering electrical performance but also in manufacturability. That criticality has to do with the subtractive process of the way we etch copper circuitry onto flex material or any other type of material.
With a subtractive or chemical etching process, there’s a trace structure that based on the height or thickness of the copper foil and relative to the trace width. If a designer isn’t properly considering conductor height to width formulas, the nominal design data—if not addressed by a supplier in CAM—could etch away the base of the copper conductor because of the unique way conductors etch in the tank.
Now, with the additive process, my understanding is that there’s no etch factor. Therefore, the limitations are only in how thin the copper can be printed. At the point that seed copper is printed or imaged onto a surface, the conductors can be grown from that copper, and the cross-section of the conductor doesn’t take on this strange trapezoidal shape as it does during a print and etch cycle; instead, it forms a rectangular shape or thereabouts. Is that true?
Dunn: Yes. There are a couple of different technologies that have received a lot of publicity within the last couple of years, which were triggered by the news that many of the current smartphones are using the modified semi-additive process in very high volume, offshore. Now, we’re looking at having similar technology to mSAP or a semi-additive process here domestically with low-volume and development-type work.
The basic idea behind these two processes is that you start with a very thin seed layer of copper, and that’s usually the key: the thinness of that copper, whether you’re using a very thin copper foil or putting a seed layer of copper down chemically. Then, it becomes an imaging process. You apply your resist, do your imaging, and then use electrolytic copper to plate the traces up to the desired width that you’re looking for. And you’re right, Kelly; because we’re not subtractively etching the trace will straight up and down, there will be no trapezoidal effects. There are RF benefits, in addition to the advantages of space, weight, and packaging. From that point on, these processes are run through PCB fabrication with the same processes used for subtractive etch today.
Page 1 of 2
Testimonial
"In a year when every marketing dollar mattered, I chose to keep I-Connect007 in our 2025 plan. Their commitment to high-quality, insightful content aligns with Koh Young’s values and helps readers navigate a changing industry. "
Brent Fischthal - Koh YoungSuggested Items
How Good Design Enables Sustainable PCBs
08/21/2025 | Gerry Partida, Summit InterconnectSustainability has become a key focus for PCB companies seeking to reduce waste, conserve energy, and optimize resources. While many discussions on sustainability center around materials or energy-efficient processes, PCB design is an often overlooked factor that lies at the heart of manufacturing. Good design practices, especially those based on established IPC standards, play a central role in enabling sustainable PCB production. By ensuring designs are manufacturable and reliable, engineers can significantly reduce the environmental impact of their products.
50% Copper Tariffs, 100% Chip Uncertainty, and a Truce
08/19/2025 | Andy Shaughnessy, I-Connect007If you’re like me, tariffs were not on your radar screen until a few months ago, but now political rhetoric has turned to presidential action. Tariffs are front-page news with major developments coming directly from the Oval Office. These are not typical times. President Donald Trump campaigned on tariff reform, and he’s now busy revamping America’s tariff policy.
Global PCB Connections: Understanding the General Fabrication Process—A Designer’s Hidden Advantage
08/14/2025 | Markus Voeltz -- Column: Global PCB ConnectionsDesigners don’t need to become fabricators, but understanding the basics of PCB fabrication can save you time, money, and frustration. The more you understand what’s happening on the shop floor, the better you’ll be able to prevent downstream issues. As you move into more advanced designs like HDI, flex circuits, stacked vias, and embedded components, this foundational knowledge becomes even more critical. Remember: the fabricator is your partner.
MKS’ Atotech to Participate in IPCA Electronics Expo 2025
08/11/2025 | AtotechMKS Inc., a global provider of enabling technologies that transform our world, announced that its strategic brands ESI® (laser systems) and Atotech® (process chemicals, equipment, software, and services) will showcase their latest range of leading manufacturing solutions for printed circuit board (PCB) and package substrate manufacturing at the upcoming 17th IPCA Show to be held at Pragati Maidan, New Delhi from August 21-23, 2025.
MKS Showcases Next-generation PCB Manufacturing Solutions at the Thailand Electronics Circuit Asia 2025
08/06/2025 | MKS Instruments, Inc.MKS Inc, a global provider of enabling technologies that transform our world, today announced its participation in Thailand Electronics Circuit Asia 2025 (THECA 2025), taking place August 20–22 at BITEC in Bangkok.