-
- News
- Books
Featured Books
- pcb007 Magazine
Latest Issues
Current IssueInventing the Future with SEL
Two years after launching its state-of-the-art PCB facility, SEL shares lessons in vision, execution, and innovation, plus insights from industry icons and technology leaders shaping the future of PCB fabrication.
Sales: From Pitch to PO
From the first cold call to finally receiving that first purchase order, the July PCB007 Magazine breaks down some critical parts of the sales stack. To up your sales game, read on!
The Hole Truth: Via Integrity in an HDI World
From the drilled hole to registration across multiple sequential lamination cycles, to the quality of your copper plating, via reliability in an HDI world is becoming an ever-greater challenge. This month we look at “The Hole Truth,” from creating the “perfect” via to how you can assure via quality and reliability, the first time, every time.
- Articles
- Columns
- Links
- Media kit
||| MENU - pcb007 Magazine
Estimated reading time: 7 minutes
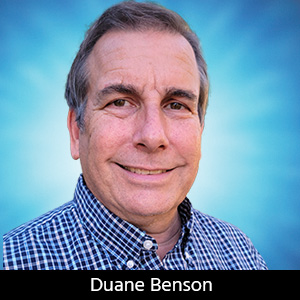
Powerful Prototypes: New PCB Fab Technology—What You Need to Know
I doubt that anyone reading this needs to be told that the printed circuit board (PCB) is the basic building block of all modern electronics, so I won’t go there, but I will discuss some of the newest terminology you might see in your daily electronics adventures. Exotic materials have been around for a while, but being “exotic,” most of us could safely ignore them. However, as clock speeds increase, and board sizes decrease, some of those exotic materials are getting close to mainstream.
While PCBs have been around since the early part of the 20th century, most of us today would still be able to identify the thing that Paul Eisler invented in 1936 as a PCB. On the surface, not a lot has changed since then beyond the introduction of solder mask, silk screen, and multiple layers. But underneath, a lot has changed, especially recently.
Most PCBs today are constructed using materials designated as FR-4. The “FR” stands for flame-retardant (or fire-resistant; something related to not burning), and the “4” indicates that the material is glass fiber and epoxy resin.
The electrical and mechanical characteristics of the PCB are determined by the specific types of binding agent, the makeup of the glass fiber or other structural material, and the circuit design and layout. Modern FR-4 boards can have dozens of copper layers and handle both surface-mount and through-hole components, but the material has its limitations. That’s where the new technology comes in. Fiberglass and standard epoxy matt do not create a physically or electronically smooth surface, and high speeds and smaller geometries increasingly require such “smoothness.”
Consider this column to be a brief glossary of the terminology you will need to be familiar with when venturing beyond a standard, rigid FR-4 PCB.
Rigid PCBs
Starting with what we already know, rigid PCBs, usually simply identified by the standard term “PCBs,” covers the vast majority of electronics construction. As indicated by the label, this type of board is intended to remain rigid and do not bend, warp, or flex. In some cases, the rigid PCB is a primary structural support for heavy components. In other cases, the board isn’t structural but needs to not warp during assembly or operation.
Rigid boards can have as few as one conductive layer or up to tens of layers. Simple slow-speed designs with good spacing between components typically use two, four, or six layers. More advanced designs that require dense spacing, or designs with exotic requirements, often need more layers for complex routing, grounding, and careful signal control.
Boards with one layer of copper attached to an insulating layer of substrate (base material) are referred to as single-sided PCBs, while boards with multiple layers may also be called multilayer PCBs. Single-sided rigid boards are rare except in very low-cost, high-volume consumer products.
Rigid boards are the most robust technology for non-exotic applications. They have good strength and durability and can be built in varying thicknesses to suit a variety of requirements. It is also the least costly technology.
Flexible, or Flex, Printed Circuits
Flex circuit boards use polyimide, a type of heat- and flame resistant-plastic with excellent insulation properties. It has good strength and is also flexible. Flex PCBs can be made single-sided or up to about one dozen layers. The more layers, the less flexible it will be.
Most flex circuits are designed to be bent once during the system assembly and then not moved in operation, such as in very small devices or devices where the circuit needs to conform to an irregular surface. Flex is also used in place of cables when repeated bending is outside of the stress capabilities of wiring harnesses. Inkjet print heads, for example, are generally connected to their electronics with flex circuits for this reason.
Rigid-flex
This is a hybrid consisting of one or more rigid PCBs with flex circuits laminated into the stack and extending out. Often, rigid-flex will be used in applications where space is at a premium, and the surfaces are irregular. Cameras, phones, and other mobile devices make heavy use of rigid-flex.
High-density Interconnect (HDI)
HDI is often promoted as though it were a special type of PCB material. However, it is more about construction technique than about materials. It is a type of rigid PCB that uses construction techniques suitable for fine-pitch components and densely packed components. It would typically use a good quality FR-4 laminate or other resin-based materials that can hold small geometry copper traces and drill holes. Boards that hold components with pin pitches of 0.4 mm (0.016 inches) or less and have blind or buried vias or vias that are 0.15 mm (0.006 inches) in diameter or narrower are typically considered to be HDI boards.
RF/High-speed Digital
Specialized materials are often needed with frequencies greater than 1 GHz and are required with frequencies above 5 GHz. This is true for analog radio-frequency designs and digital designs that operate at those frequencies. The materials use specialized resins with glass fiber, PTFE (Teflon), or specialized resins combined with ceramic. The glass fiber may come as a woven cloth, a matted cloth, or as fibers mixed in the binder and is engineered to match the required frequency response and desired loss characteristics.
High-speed Digital vs. High-frequency
High-speed digital (HSD) and high-frequency describe two different types of signals that are both in the same operating frequency area. HSD describes digital signals in the form of square waves. Today, HSD is generally considered to be digital signals operating at a clock speed of 1 GHz and above. High-frequency refers to radio-frequency (RF) analog signals in the RF spectrum. In the PCB world, it generally refers to analog signals 500 MHz and above.
It is important to understand that the use of these terms is not absolute. Unfortunately, different people and companies will use some of these terms interchangeably or have various definitions to describe different speed ranges.
RF has much more critical requirements than HSD, even in the same frequency ranges. HSD is concerned with the ability to accurately discern between a value of one and a value of zero. As long as the value is discernible, the shape of the signal waveform is not as critical. With RF signals, however, the shape of the waveform is absolutely critical.
Dk (dielectric constant) and Df (dissipation, or electrical loss factor) are the two primary electrical characteristics to consider when looking at high-speed materials.
Metal and Ceramic Core
Metal core, usually aluminum, and ceramic core are hybrid materials with the aluminum or ceramic being laminated to a thin layer of FR-4 or higher-temperature PCB laminate. These materials are used in high-temperature applications, with the metal or ceramic core acting as a heat spreader or heat sink. High-power LED lighting, for example, will use an aluminum core board on which to mount the LED.
They are also used in applications that may not be exposed to extremes of temperature but need careful control of the coefficient of thermal expansion (CTE). For example, large integrated circuits in ceramic chip carriers or direct die attached chips must be on a substrate with a similar CTE if exposed to regular thermal cycling. Otherwise, the stress on the solder joints may crack or break the soldered connections.
Materials Used in PCB Construction
Here’s an overview of some materials used in PCB construction, both common and exotic.
- FR-2 is on the low end of PCB materials. It is a phenolic paper substrate used on very low-cost, single-sided PCBs. It is an old technology that is only used where cost is the primary factor, and quality and reliability are not major concerns.
- FR-4 is the most common PCB material used today. It is constructed of epoxy resin and woven glass fiber. It has the best compromise of manufacturability, durability, and reliability for non-exotic applications.
- Polyimide (aka Kapton) is the standard material used for flexible printed circuits. It is a very strong, high-temperature polymer used to make printed circuits that either need to bend at build time, fit into very tight spaces, or flex during operation.
- PTFE (aka Teflon®) is the standard for high-frequency PCBs. It may be embedded with glass fibers or with a ceramic. The purer the PTFE material, the more difficult it is to work with due to the material being soft and difficult to adhere to anything else. PTFE materials are typically used at frequencies of 5 GHz or more. The most common high-speed PTFE material used is supplied by Rogers Corporation, and the name “Rogers,” while a trademark, is often used generically to mean “high-speed” laminate. PTFE is sometimes referred to as “fluorine substrate.”
- PPE and PPO are specialized resins used with glass fiber and are suitable for use in the range of 1–10 GHz. They look much like FR-4, but have the tightened electrical characteristics needed for higher-speed operation than FR-4.
- Liquid crystalline polymer (LCP) is a newer high-speed material option designed for multilayer, high-speed circuit boards. It is more flexible than other materials. While not as flexible as the polyimide used in flex circuits, LCP does have the ability to be bent far more than any other high-speed material.
The Future
And even more changes are on the way. In the near future, you may see 3D-printed multilayer PCBs, direct copper deposition construction techniques, and even printed circuit systems so dense that they will be measured in microns rather than mils (or fractions of a millimeter). Technological developments never slow down.
Duane Benson is marketing manager and CTO at Screaming Circuits.
More Columns from Powerful Prototypes
Powerful Prototypes: Small Computer ModulesPowerful Prototypes: A Trip Back to the Basics
Powerful Prototypes: The Work World in 2021
Powerful Prototypes: Why Datasheets Matter
Powerful Prototypes: Manufacturing in an Uncertain World
Powerful Prototypes: An Open-Source Adventure
Powerful Prototypes: Five Technological Shifts in the New Decade
Powerful Prototypes: Cost Reduction in Design