Plug-and-play for Higher Purity
November 25, 2019 | TA-POEstimated reading time: 3 minutes
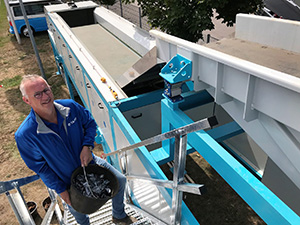
Separating transformers, electric motors, but also small fractions of copper wire from ferrous scrap streams is a piece of cake for the TA-PO 1000, a solution developed by Dutchman Roberto van den Kieboom.
TA-PO is a relatively young recycling technology firm from the Netherlands that designs and fabricates lines to separate magnetic material from partially magnetic material. Company founder and CEO Roberto Van den Kieboom is on a mission. ‘Asia’s scrap import restrictions have made clear there is no future for mixed materials,’ he says. ‘Our solutions help recyclers reach the higher purity and quality required by the smelters.’ Other advantages include multiple shredding and the end of any sorting by hand.
The TA-PO 1000 is a complete plug-and-play line that can be used to separate current electronic scrap flows from 0 to 130 mm in a clean iron fraction with less than 0.3% copper. This fraction after separation is approximately 80% of the total input of the TA-PO 1000 separator, the remaining 20% consists of transformers, electric motors, small copper wire, printed circuit boards and more.
Tiny copper fractions
Van den Kieboom: ‘These e-scrap fractions are often cleaned as much as possible by hand sorting. However, it appears that the ferrous metal usually contains more than 0.3% copper, which is a shame because it cannot be used as a high-quality raw material. And the copper is in the iron fraction for which ultimately is not paid for.’
Another thing, says the entrepreneur, it’s impossible to separate small copper wire by hand. ‘But by using the TA-PO 1000, even the smallest pieces of wire automatically end up with the transformers and electric motors.’
The TA-PO saves labour costs. Separating eight tonnes of e-scrap fraction by hand requires four human sorters. The TA-PO 1000 separator can be used 24/7 with an up-time of 99%.
Powerful magnetics
The TA-PO 1000 features a specially developed magnet which separates 100% magnetic parts (clean iron) from partly magnetic parts (transformers, electric motors, printed circuit boards, etc.) at a high speed via a vibrating feeder, chute and conveyor belt through amagnetic field.
Asked for the machine’s capacity, Van den Kieboom says: ‘It all depends on the scrap input, size of the fractions and the settings of the technology. On average, it is 10 to 30 tonnes per hour. But we are currently working on a unit capable of processing up to 70 tonnes per hour.’
Easy to maintain
Bulk weight, fraction size and required settings determine the capacity of the TA-PO 1000. Smart design means maintenance is carried out quickly. Challenging parts such as side guide caps and the sliding channel can be opened automatically via a touchscreen, conveniently as well as safely because the machine can no longer be started at these times.
Remote service
All TA-PO 1000 separation machines are equipped as standard with a modem so that support can always be provided remotely. Adjustments can also be carried out by the operator’s own staff after a brief explanation. When acorrect separation result has been achieved, this adjustment can easily be saved as standard and quickly recalled. The TA-PO 1000 can either be used as stand-alone unit or directly in line behind the shredder and existing magnet system.
Ready to use… indoors or outdoors
The TA-PO 1000 has a 15 metre cable and a 380 volt / 32 amp plug, so it canbe used everywhere without having to make special provisions in advance. The entire TA-PO 1000 separation machine is almost 11 metres long, 1.65 metres wide and 3.4 metres high with a total weight of less than seven tonnes.
According to Van den Kieboom, indoor installation is preferable but the TA-PO 1000 also performs well under extreme climate conditions: ‘Even at minus 10 Celsius, but also at plus 45 Celsius.’ Partly thanks to its galvanised and double-layer powder-coated base frame, a long service life is guaranteed.
Suggested Items
The Evolution of Picosecond Laser Drilling
06/19/2025 | Marcy LaRont, PCB007 MagazineIs it hard to imagine a single laser pulse reduced not only from nanoseconds to picoseconds in its pulse duration, but even to femtoseconds? Well, buckle up because it seems we are there. In this interview, Dr. Stefan Rung, technical director of laser machines at Schmoll Maschinen GmbH, traces the technology trajectory of the laser drill from the CO2 laser to cutting-edge picosecond and hybrid laser drilling systems, highlighting the benefits and limitations of each method, and demonstrating how laser innovations are shaping the future of PCB fabrication.
Day 2: More Cutting-edge Insights at the EIPC Summer Conference
06/18/2025 | Pete Starkey, I-Connect007The European Institute for the PCB Community (EIPC) summer conference took place this year in Edinburgh, Scotland, June 3-4. This is the third of three articles on the conference. The other two cover Day 1’s sessions and the opening keynote speech. Below is a recap of the second day’s sessions.
Day 1: Cutting Edge Insights at the EIPC Summer Conference
06/17/2025 | Pete Starkey, I-Connect007The European Institute for the PCB Community (EIPC) Summer Conference took place this year in Edinburgh, Scotland, June 3-4. This is the second of three articles on the conference. The other two cover the keynote speeches and Day 2 of the technical conference. Below is a recap of the first day’s sessions.
Preventing Surface Prep Defects and Ensuring Reliability
06/10/2025 | Marcy LaRont, PCB007 MagazineIn printed circuit board (PCB) fabrication, surface preparation is a critical process that ensures strong adhesion, reliable plating, and long-term product performance. Without proper surface treatment, manufacturers may encounter defects such as delamination, poor solder mask adhesion, and plating failures. This article examines key surface preparation techniques, common defects resulting from improper processes, and real-world case studies that illustrate best practices.
RF PCB Design Tips and Tricks
05/08/2025 | Cherie Litson, EPTAC MIT CID/CID+There are many great books, videos, and information online about designing PCBs for RF circuits. A few of my favorite RF sources are Hans Rosenberg, Stephen Chavez, and Rick Hartley, but there are many more. These PCB design engineers have a very good perspective on what it takes to take an RF design from schematic concept to PCB layout.