-
- News
- Books
Featured Books
- pcb007 Magazine
Latest Issues
Current IssueThe Hole Truth: Via Integrity in an HDI World
From the drilled hole to registration across multiple sequential lamination cycles, to the quality of your copper plating, via reliability in an HDI world is becoming an ever-greater challenge. This month we look at “The Hole Truth,” from creating the “perfect” via to how you can assure via quality and reliability, the first time, every time.
In Pursuit of Perfection: Defect Reduction
For bare PCB board fabrication, defect reduction is a critical aspect of a company's bottom line profitability. In this issue, we examine how imaging, etching, and plating processes can provide information and insight into reducing defects and increasing yields.
Voices of the Industry
We take the pulse of the PCB industry by sharing insights from leading fabricators and suppliers in this month's issue. We've gathered their thoughts on the new U.S. administration, spending, the war in Ukraine, and their most pressing needs. It’s an eye-opening and enlightening look behind the curtain.
- Articles
- Columns
- Links
- Media kit
||| MENU - pcb007 Magazine
Ledia 6 Direct Imaging System Offers Enhanced Speed and Precision
December 29, 2019 | Pete Starkey, I-Connect007Estimated reading time: 3 minutes
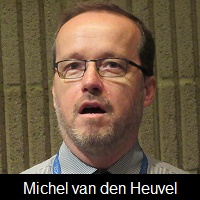
I recently met with Ucamco’s Michel Van den heuvel, imaging product group director, to discuss the benefits of the Ledia 6 direct imaging system, which was introduced earlier this summer and features scan-alignment and improvements in registration and positioning accuracy.
Pete Starkey: Michel, it’s great to see you again.
Michel Van den heuvel: Hi, Pete. I’m happy to see you.
Starkey: One of your specialties is the Ledia direct imaging system, and I understand that there have been some new developments lately. Can you bring us up-to-date with the latest advances?
Van den heuvel: After Ledia 5, SCREEN Graphic and Precision Solutions introduced Ledia 6, which is a further improvement and development of the existing Ledia 5. Based on the feedback they had from customers, they have made further enhancements. One of the main improvements is a new camera-registration system. On the existing Ledia 5, they used step-alignment, which means that the table stops, switches on the light of the registration camera, and takes a picture of the fiducial, and then the table moves to the next fiducial and takes a picture again.
In the Ledia 6, they have introduced scan-alignment. The table moves at a constant speed and does not stop any more. When it needs to take a fiducial, it switches on the light and quickly takes the picture—it’s like a stroboscope effect—and switches the light on and off while the table keeps moving. Through software, they stitch all these pictures together and know exactly where all the fiducials are. It goes much faster because the table doesn’t need to stop.
Starkey: How accurately can you hold registration with this system?
Van den heuvel: Registration and positioning accuracy go together because, eventually, the result that the customer can see on the panel is positioning accuracy. With Ledia 6, we have improved positioning accuracy by 10% compared to the Ledia 5, and also improved registration accuracy by 20%.
In addition to the scan-alignment system, the width of the registration cameras has been doubled in size. Take the example where a solder mask panel has been routed after the panel has been made. This can influence not only the exact size but also the position of the fiducials towards the edge of the panel. With a smaller camera, this could previously result in sometimes missing a fiducial. The double-width scan-alignment camera will completely resolve this issue.
Another improvement, together with the scan-alignment, is that if you have multiple step-and-repeat single PCBs on the panel, and the fiducials of adjacent PCBs are within 12 millimeters of each other, our front-end software will automatically combine these fiducials and scan them with one camera in one go. Instead of doing two scans, you can combine it in one scan. Especially for step-and-repeats of panels, such as BGAs, this greatly improves scan-alignment time.
A further improvement involves new, stronger light sources that we built into the imaging heads. We made a change to the optics to make them capable of handling this stronger light source, which results in up to 25–30% throughput improvement. And the less sensitive is the material, the bigger the improvement you will notice.
Starkey: In a typical case with a solder mask, what would be the exposure time?
Van den heuvel: Exposing time depends on the panel. For 100 millijoules, the exposing time for a 610 x 457-millimeter [24 x 18-inch] panel side would be around 23.7 seconds compared to the previous 30.3 seconds, including four-point registration. Whenever you gain 6.6 seconds in a single run, that is a huge improvement.
Starkey: And your light sources can be tuned to achieve the optimum wavelength for the photo-initiator system in the solder mask?
Van den heuvel: Yes. The way the optical heads are designed, we can 100% independently adjust the different main wavelengths that we use: 365, 385, and 405 nanometers. We can independently adjust each wavelength from zero to 100% and tune to the solder mask at hand and achieve the best possible sidewall, reducing undercut to a minimum.
Starkey: Have you already launched the Ledia 6 into the market?
Van den heuvel: Yes, we have. The first systems in Europe have been sold this year, and two of them have already been installed at ICS in Italy and Optiprint in Switzerland. The results have been as we expected, and our clients are delighted with the outcome. Next week, we will install a third one at Eurocircuits in Hungary.
Starkey: That is splendid! I wish you every success with the system. Thank you very much for your time.
Van den heuvel: Thank you, Pete.
Suggested Items
Driving Innovation: Direct Imaging vs. Conventional Exposure
07/01/2025 | Simon Khesin -- Column: Driving InnovationMy first camera used Kodak film. I even experimented with developing photos in the bathroom, though I usually dropped the film off at a Kodak center and received the prints two weeks later, only to discover that some images were out of focus or poorly framed. Today, every smartphone contains a high-quality camera capable of producing stunning images instantly.
Hands-On Demos Now Available for Apollo Seiko’s EF and AF Selective Soldering Lines
06/30/2025 | Apollo SeikoApollo Seiko, a leading innovator in soldering technology, is excited to spotlight its expanded lineup of EF and AF Series Selective Soldering Systems, now available for live demonstrations in its newly dedicated demo room.
Indium Corporation Expert to Present on Automotive and Industrial Solder Bonding Solutions at Global Electronics Association Workshop
06/26/2025 | IndiumIndium Corporation Principal Engineer, Advanced Materials, Andy Mackie, Ph.D., MSc, will deliver a technical presentation on innovative solder bonding solutions for automotive and industrial applications at the Global Electronics A
Fresh PCB Concepts: Assembly Challenges with Micro Components and Standard Solder Mask Practices
06/26/2025 | Team NCAB -- Column: Fresh PCB ConceptsMicro components have redefined what is possible in PCB design. With package sizes like 01005 and 0201 becoming more common in high-density layouts, designers are now expected to pack more performance into smaller spaces than ever before. While these advancements support miniaturization and functionality, they introduce new assembly challenges, particularly with traditional solder mask and legend application processes.
Knocking Down the Bone Pile: Tin Whisker Mitigation in Aerospace Applications, Part 3
06/25/2025 | Nash Bell -- Column: Knocking Down the Bone PileTin whiskers are slender, hair-like metallic growths that can develop on the surface of tin-plated electronic components. Typically measuring a few micrometers in diameter and growing several millimeters in length, they form through an electrochemical process influenced by environmental factors such as temperature variations, mechanical or compressive stress, and the aging of solder alloys.