RedHawk Partners With Pelican Engineering LLC for GMP Manufacturing Oversight
February 28, 2020 | PR NewswireEstimated reading time: 2 minutes
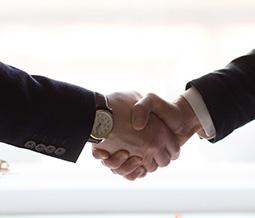
RedHawk Holdings Corp., a diversified holding company engaged in sales and distribution of medical devices, branded generic pharmaceutical drugs, commercial real estate investment and leasing, point of entry full-body security systems, and specialized financial services, announced today that RedHawk Research & Development LLC, a wholly-owned subsidiary of the Company, has agreed to partner with Louisiana-based Pelican Engineering LLC ("Pelican") for the supervision of the Company's quality assurance and future research and development programs.
Pelican is a full-service electronics engineering design firm that provides engineering services and component manufacturing in all aspects of the electrical, electronics, and computer engineering disciplines. Primarily focused on embedded printed circuit board hardware and software development, Pelican is capable of in-house engineering, design, manufacturing, and turn-key delivery of high-quality embedded systems.
Pelican was instrumental in the redesign of the SANDD Pro™ as well as the new printed circuit boards used in the SANDD mini – HP™ and the SANDD mini – FR™. Separately, Pelican is also expected to lead the development and redesign of "Centri", the Company's controlled entry security system, a unique, closed cabinet, nominal dose transmission full-body x-ray scanner.
In June 2019, the Company announced the transition and ongoing maintenance of its current FDA-approved quality management system to the higher and more stringent international medical device standard, ISO 13485:2016. The Company believes it is now near completion of this previously announced quality management transition and has now partnered with Pelican to develop and supervise the quality assurances testing believed necessary to maintain adherence to the stringent standards of ISO 13485:2016.
ISO 13485:2016 specifies global requirements for a quality management system where an organization must demonstrate its ability, and the ability of its suppliers, to provide medical devices and related services that consistently meet customer and applicable international regulatory requirements. ISO 13485 was specifically developed with the objective of harmonizing medical device regulatory requirements for quality management systems in major markets around the world including the United States, Europe, Canada, Japan and Australia. ISO 13485 meets, or exceeds, all U.S. Food and Drug Administration Quality System Regulations Standard 21 CFR 820 which was established in 1978 to outline Current Good Manufacturing Practices (GMP) in the United States.
Commenting on the partnership with Pelican, G. Darcy Klug, RedHawk's Chairman and Interim Chief Executive Officer, said "We believe the previously announced partnership with the CKRX Enterprise sales organization positions us well for the commercial launch of our SANDD™ line of needle incineration products.Our next marketing focus is the consumer launch of the SANDD™ line of needle incineration devices. To properly position RedHawk for the consumer market, we believe we need to obtain Durable Medical Equipment ("DME") Accreditation of our quality assurance program. The transition of our quality assurance program to ISO 13485:2016 and the completion of the quality assurance partnership with Pelican is the next step in preparing for DME Accreditation."
"DME Accreditation is necessary for RedHawk to obtain a DME supplier license," continued Mr. Klug. "With Pelican's support, we believe that we are now positioned to seek the necessary DME Accreditation approvals. With DME Accreditation, we anticipate our customers will be eligible to receive Medicare, Medicaid or insurance company reimbursement for the purchase of our SANDD™ line of needle incineration devices. Obtaining these approvals would be a major milestone on the path for RedHawk to continue executing on its business model."
Testimonial
"We’re proud to call I-Connect007 a trusted partner. Their innovative approach and industry insight made our podcast collaboration a success by connecting us with the right audience and delivering real results."
Julia McCaffrey - NCAB GroupSuggested Items
BAE Systems Receives $12 Million Contract from L3Harris
07/25/2025 | BAE SystemsBAE Systems has received a $12 million contract from L3Harris to support the modification of two Gulfstream G550 aircraft into airborne electronic attack (EA) platforms for the Italian Air Force.
Southwest Antennas Secures First Major European Order for their Permanent Mounting Kits
07/24/2025 | Southwest AntennasSouthwest Antennas is proud to announce the receipt of its first major European order for the company’s Permanent Mounting Kits, marking a significant milestone in its international expansion efforts.
SCS Launches New G4 Spin Coater and Upgrades 6800 Series with Improved Design Features
07/23/2025 | SCSSpecialty Coating Systems (SCS) is pleased to announce the launch of its next-generation G4 Spin Coater, delivering enhanced control, connectivity and usability for research, development and small-scale production environments.
AI-driven MES Rewriting the Rules of Manufacturing Transformation
07/23/2025 | Francisco Almada Lobo, Critical ManufacturingThe Critical Manufacturing MES & Industry 4.0 International Summit, June 12–13, revealed a profound shift in how manufacturers approach digital transformation. AI-enabled execution systems are no longer a future ambition but are essential for navigating complexity and driving change.
Smart Automation: What Industry 4.0 Means for Mid-sized Electronics Manufacturing
07/24/2025 | Josh Casper -- Column: Smart AutomationIndustry 4.0 has become a go-to phrase in manufacturing circles, though it’s often used as a slogan rather than a clearly defined concept. At electronics manufacturing trade shows or conferences, marketing banners and vendor literature display the term prominently; many technical sessions also focus on it. Industry 4.0 is the push for smart factories, with a focus on autonomous machines, cloud-connected systems, and AI-powered decisions.