Joe Fjelstad Breaks Down His Occam Process
March 4, 2020 | I-Connect007 Editorial TeamEstimated reading time: 21 minutes
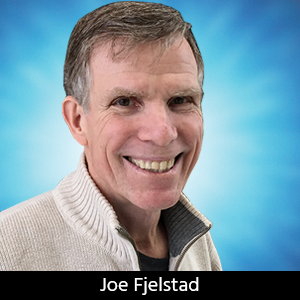
Joe Fjelstad recently met with the I-Connect007 Editorial Team to discuss the potential benefits of his Occam process for solderless assembly. This technique allows assembly of the PCB without the risks associated with traditional surface-mount processes, such as solder joint failure. Has the time come for the industry to embrace Occam?
Nolan Johnson: Joe, we wanted to talk to you about shrinking device sizes and features because you have been doing some work in that area.
Joe Fjelstad: I actually go back to Tessera where we were developing chip-scale packaging in the form of the micro-BGA in the early 1990s. Tom Di Stefano was the company founder. The original name of the company was IST Associates. The micro-BGA addressed solder reliability issues at that time. Tab was the rage at that time using the interconnect on the exterior of an IC and fanning out to a still fairly fine pitch. Tom had the notion of putting a little flex circuit on top of the chip and then fanning it inward to a relatively coarse pitch above the surface of the IC. That was the earliest of the chip-scale packages and the one that really broke the ice for the CSP revolution.
Tom knew from his experience at IBM that there were concerns about the reliability of flip-chip and use of underfill and other things that people were looking at to try and deal with the inevitable coefficient of thermal expansion mismatch between a silicon chip at 3 ppm/C and FR-4 with a CTE of 24 ppm/C. He and his colleagues at the time came up with the idea of putting a buffer between the chip and the PCB substrate. It became a poor man’s flip-chip and something that everybody could use. That was almost 30 years ago, and we’re seeing the benefits of that still today.
Johnson: One of the things you’ve been working on recently is the Occam process. Tell us about that.
Fjelstad: For about a dozen years, I’ve been pounding sand. I think it is an inevitability, but it involves a sea change in terms of how things get done. Happy Holden is familiar with my pursuit of some order in the industry and the idea of locking in on a fundamental grid pitch. Over a quarter-century ago, I put together a little Lego module with Vern Solberg at Tessera and said, “Here’s what the future looks like.” All the component terminations are on a common grid, and the result is the ability to route more predictably and easily.
Quite frankly, I think we can do it, but the reality is that it involves a lot of attention to and embracing of order, rather than the cacophony that we have today. The situation today is a seemingly endless number of IC package types, lead formats, and pitches. These were the result of choosing to transition to surface mount without fully appreciating its potential and power. Sadly, we didn’t immediately jump to area array. Instead, we went to peripherally leaded components first, and then that’s when the wheels of the orderly design fell off, and the 80% rule stepped in. It’s nonsense.
Johnson: Walk us through it, for those who aren’t familiar with your Occam process.
Fjelstad: The idea sprang from my opposition to lead-free because tin-lead is a superior solution, and there was no real risk of harm to the consumer from lead in electronic solder. However, as soon as the EU mandated lead-free, I had an epiphany while sitting down to write an article, and I wrote three words—assembly without solder—and the Occam process came immediately to mind. Reverse the manufacturing process. Rather than building a PCB and soldering components to it, build a “component board” and build the circuits up on it using an additive process.
This was the first way I saw, but there are many ways to do it. Fundamentally, the idea was to invert or reverse the process. The Occam process concept completely bypasses the soldering process and all of the problems associated with it, which we’re all quite familiar with, and we have been dealing with in earnest for the last dozen years or more. The transition to lead-free was not easy, nor was it required in the long run, if you look at the science.
Johnson: I’m trying to imagine your component board and the circuitry on top.
Fjelstad: I’ve created a number of graphics over time, but in cross-section, it becomes fairly clear what the process steps are. There’s actually a significant reduction in the number of steps required for manufacturing and electronics assembly. In fact, with help from my good friend, PCB designer John Goodrich, a demo was cobbled together, showing how one could build something like this at home using 5-minute epoxy, conductive ink, and nail polish. I won’t bother you with the details here, but it worked. While I have a preference for bottom-terminated components (BTCs) and land grid arrays (without solder balls), the concept will also work with legacy components; it is just not optimal. The idealized components from my perspective are only components that exist on a common grid and only components that have bottom termination.
Here’s a simple thought experiment that illustrates the process. Think of putting all the components flat on a surface to which epoxy does not adhere well. Build a little dam around the components, pour epoxy over them to seal them in place, lift off the cured embedded component assembly, and then start doing your buildup on the exposed terminations. There are obviously some cleaning steps to make sure the contacts are not contaminated, and there may be a number of layers of insulation that are going to have to be built onto it, depending on the number of copper layers required. My thinking along those lines has been the possibility of using a photoimageable resist because it’s very easy from a buildup standpoint and building layer on layer.
Page 1 of 3
Suggested Items
Driving Innovation: Direct Imaging vs. Conventional Exposure
07/01/2025 | Simon Khesin -- Column: Driving InnovationMy first camera used Kodak film. I even experimented with developing photos in the bathroom, though I usually dropped the film off at a Kodak center and received the prints two weeks later, only to discover that some images were out of focus or poorly framed. Today, every smartphone contains a high-quality camera capable of producing stunning images instantly.
Hands-On Demos Now Available for Apollo Seiko’s EF and AF Selective Soldering Lines
06/30/2025 | Apollo SeikoApollo Seiko, a leading innovator in soldering technology, is excited to spotlight its expanded lineup of EF and AF Series Selective Soldering Systems, now available for live demonstrations in its newly dedicated demo room.
Indium Corporation Expert to Present on Automotive and Industrial Solder Bonding Solutions at Global Electronics Association Workshop
06/26/2025 | IndiumIndium Corporation Principal Engineer, Advanced Materials, Andy Mackie, Ph.D., MSc, will deliver a technical presentation on innovative solder bonding solutions for automotive and industrial applications at the Global Electronics A
Fresh PCB Concepts: Assembly Challenges with Micro Components and Standard Solder Mask Practices
06/26/2025 | Team NCAB -- Column: Fresh PCB ConceptsMicro components have redefined what is possible in PCB design. With package sizes like 01005 and 0201 becoming more common in high-density layouts, designers are now expected to pack more performance into smaller spaces than ever before. While these advancements support miniaturization and functionality, they introduce new assembly challenges, particularly with traditional solder mask and legend application processes.
Knocking Down the Bone Pile: Tin Whisker Mitigation in Aerospace Applications, Part 3
06/25/2025 | Nash Bell -- Column: Knocking Down the Bone PileTin whiskers are slender, hair-like metallic growths that can develop on the surface of tin-plated electronic components. Typically measuring a few micrometers in diameter and growing several millimeters in length, they form through an electrochemical process influenced by environmental factors such as temperature variations, mechanical or compressive stress, and the aging of solder alloys.