-
-
News
News Highlights
- Books
Featured Books
- pcb007 Magazine
Latest Issues
Current IssueThe Hole Truth: Via Integrity in an HDI World
From the drilled hole to registration across multiple sequential lamination cycles, to the quality of your copper plating, via reliability in an HDI world is becoming an ever-greater challenge. This month we look at “The Hole Truth,” from creating the “perfect” via to how you can assure via quality and reliability, the first time, every time.
In Pursuit of Perfection: Defect Reduction
For bare PCB board fabrication, defect reduction is a critical aspect of a company's bottom line profitability. In this issue, we examine how imaging, etching, and plating processes can provide information and insight into reducing defects and increasing yields.
Voices of the Industry
We take the pulse of the PCB industry by sharing insights from leading fabricators and suppliers in this month's issue. We've gathered their thoughts on the new U.S. administration, spending, the war in Ukraine, and their most pressing needs. It’s an eye-opening and enlightening look behind the curtain.
- Articles
- Columns
- Links
- Media kit
||| MENU - pcb007 Magazine
Institute of Circuit Technology Spring Seminar 2020
March 11, 2020 | Pete Starkey, I-Connect007Estimated reading time: 11 minutes
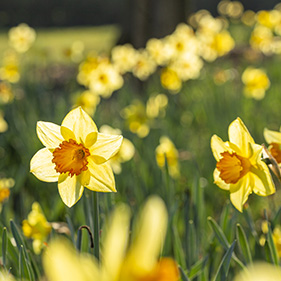
Back to Meriden, the nominal centre of England. The daffodils were blooming, although the weather was hardly spring-like: cold, blustery, and rivers bursting their banks. Some had to take substantial detours to avoid flooded roads, but members of the Institute of Circuit Technology (ICT) are robust and resilient! A good crowd made it to the seminar that followed the annual general meeting of the ICT, with five specialist presentations and excellent opportunities to network with their peers in the industry.
In his welcoming remarks, ICT Technical Director Bill Wilkie commented that the Institute continued to attract new members—membership currently totals over 400—and that the Annual Foundation Course remained an especially popular educational event, introducing the technology to generation after generation of printed circuit engineers and technicians.
The Foundation Course had originated 40 years ago, organised by the Northern U.K. Printed Circuit Group, and held at the Hewlett-Packard facility in South Queensferry. He acknowledged the companies who continued to support the course and presented commemorative plaques to David Douglas, managing director of the Eurotech Group, and Neil Martin, chairman of the Merlin PCB Group.
Wilkie had once more coordinated an excellent seminar agenda. He introduced as his first speaker Chris Wall, technical director at Electra Polymers, who gave a detailed review of the development and processing of an inkjettable solder mask and discussed the advantages of using it in PCB manufacturing. An understanding of the inkjet application process was the fundamental first step in the development programme, and Wall gave a brief introduction to the types of print-head available and how ink-drops were generated.
This gave a good insight into the factors constraining the formulator, particularly the limited choice of suitable raw materials compared with those associated with conventional solder masks, restricted to very low viscosity resins and monomers and pigments with nanoscale particle sizes. Furthermore, it was necessary to keep filler content low or absent, which led to further challenges in achieving acceptable flammability, thermal shock, and solder resistance. Formulations also included flow agents, surface property modifiers, photoinitiators, and thermal curing agents.
Optimum viscosity varied according to the type of print head, and—in combination with surface tension—affected jetting performance according to some complicated fluid dynamics where stable drop formation was a function of Reynolds number, Weber number, and Ohnesorge number. Wall did not dig too deeply into the physics. And once the ink hit the surface, its wetting characteristics and factors like contact angle affected spreading, bleed, and track-edge thinning, as well as the coating performance of any subsequent layers deposited.
The curing mechanism depended on the resin chemistry, and inkjet formulations were generally pin-cured with UV during the printing operation to effectively set the image. A final thermal cure completed the crosslinking reaction. Once a test product had been formulated, it would initially be screen printed to assess its basic solder mask properties, and modified as necessary before being evaluated for its jetting performance and the properties of the jetted coating after curing. The sequence would be repeated as many times as necessary while the formulation was fine-tuned and optimised.
Attributes—such as solder dam resolution, resistance to multiple solder reflow cycles, compatibility with plating chemistry, and conformal coatings—would be ascertained before submitting the final formulation for external testing for compliance with UL 94V0, RoHS, IPC-SM840, NASA specifications, etc., as well as automotive standards and individual customer requirements.
Wall summarised the advantages of the inkjet process over the liquid photoimageable route, particularly in the elimination of the coating, drying stages, exposure and development stages, the savings in space, water and energy costs, and the lack of solvent emissions. There was no undercut at image edges, and—therefore—no risk of chemical or flux entrapment. He emphasised that inkjet solder mask relied on good surface preparation for adhesion, chemical resistance, and print quality.
A consequence of the continuing evolution of technology in the electronics industry was the production of e-waste from end-of-life equipment. It had been estimated that the U.K. produced over 500,000 tonnes annually of waste from electrical and electronic equipment (WEEE), of which over 40,000 tonnes originated from IT and telecoms equipment.
Toxic components in WEEE could cause environmental problems if not properly managed; conversely, WEEE contained valuable metals that could potentially be recovered and recycled as raw materials. Indeed, in the case of printed circuit assemblies, the metal content of the waste was higher than in natural metal ores. For example, one tonne of WEEE could contain gold worth around £45,000.
A current project at Coventry University focused on the recovery and recycling of metals from waste printed circuit assemblies as a step towards the circular economy and the sustainability of critical raw materials. Daniel Ray introduced the concept of “urban biomining” as an alternative to the traditional methods of recycling: pyrometallurgy—which involved high temperatures for pyrolysis or smelting—or hydrometallurgy—which utilised chemicals such as acids and cyanide. Neither was considered environmentally sustainable in today’s climate, and bioleaching had been identified as a way forward.
Biomining? Bioleaching? Science fiction? Dr. Mahsa Baniasadi explained that biomining offered a cost-effective and environmentally friendly option for leaching metals from ore using microorganisms to convert solid metals into aqueous species, and was already used to produce about 5% of the world’s gold and 20% of the world’s copper. The objective of urban biomining was to use spent electronics as the feedstock to make fresh electronic components, employing synthetically enhanced microbes to biologically extract specific metals.
As an illustration of current recycling rates, a standard periodic table had been highlighted in different colours to indicate end-of-life recycling input. Copper, silver, and lead were all above 50%, but there was a very low input of many endangered elements. The natural sources of these elements were limited and not located in the U.K., so there was plenty of scope for recycling and sustaining the supply of critical raw materials.
Dr. Baniasadi briefly explained the terminology and some of the mechanisms relevant to bioleaching; for example, redoxolysis referred to oxidation-reduction reactions catalysed by bacteria, acidolysis was the production of biogenic acid, and complexolysis was the production of biogenic complexing agents. She discussed iron oxidation, sulphur oxidation, and biogenic cyanide. Once a metal was in solution, electro-winning techniques could be used to deposit it in a relatively pure state.Page 1 of 2
Suggested Items
Driving Innovation: Direct Imaging vs. Conventional Exposure
07/01/2025 | Simon Khesin -- Column: Driving InnovationMy first camera used Kodak film. I even experimented with developing photos in the bathroom, though I usually dropped the film off at a Kodak center and received the prints two weeks later, only to discover that some images were out of focus or poorly framed. Today, every smartphone contains a high-quality camera capable of producing stunning images instantly.
Hands-On Demos Now Available for Apollo Seiko’s EF and AF Selective Soldering Lines
06/30/2025 | Apollo SeikoApollo Seiko, a leading innovator in soldering technology, is excited to spotlight its expanded lineup of EF and AF Series Selective Soldering Systems, now available for live demonstrations in its newly dedicated demo room.
Indium Corporation Expert to Present on Automotive and Industrial Solder Bonding Solutions at Global Electronics Association Workshop
06/26/2025 | IndiumIndium Corporation Principal Engineer, Advanced Materials, Andy Mackie, Ph.D., MSc, will deliver a technical presentation on innovative solder bonding solutions for automotive and industrial applications at the Global Electronics A
Fresh PCB Concepts: Assembly Challenges with Micro Components and Standard Solder Mask Practices
06/26/2025 | Team NCAB -- Column: Fresh PCB ConceptsMicro components have redefined what is possible in PCB design. With package sizes like 01005 and 0201 becoming more common in high-density layouts, designers are now expected to pack more performance into smaller spaces than ever before. While these advancements support miniaturization and functionality, they introduce new assembly challenges, particularly with traditional solder mask and legend application processes.
Knocking Down the Bone Pile: Tin Whisker Mitigation in Aerospace Applications, Part 3
06/25/2025 | Nash Bell -- Column: Knocking Down the Bone PileTin whiskers are slender, hair-like metallic growths that can develop on the surface of tin-plated electronic components. Typically measuring a few micrometers in diameter and growing several millimeters in length, they form through an electrochemical process influenced by environmental factors such as temperature variations, mechanical or compressive stress, and the aging of solder alloys.