New, Integrated Solution From Rehm for Efficient Use of Nitrogen With the Coolflow Option
April 23, 2020 | Rehm Thermal SystemsEstimated reading time: 3 minutes
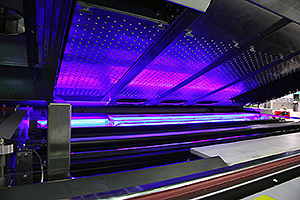
The VisionXP+ convection soldering system from Rehm Thermal Systems features different types of cooling.
For an optimal reflow soldering result, not only is melting of the solder important but also as a stable and reliable cooling process. This soldering process can be designed flexibly with the VisionXP+ convection soldering system from Rehm Thermal Systems. With Rehm CoolFlow, Rehm offers an innovative and integrated cooling principle using liquid nitrogen—there is also a standard cooling option with up to four cooling modules, an extended cooling line, underside cooling and an energy-saving cooling variant.
Along with their partner Air Liquide, Rehm has developed a cooling system (“Rehm CoolFlow”), which deploys the nitrogen used for inertia even more efficiently. The –180 °C cold liquid nitrogen releases its energy in the cooling line, then evaporates and can then be used in its gaseous state for inerting the process atmosphere. The cooling water, which previously required high energy use for cooling, including cooling unit and refrigerant, is completely eliminated. The entire nitrogen path—from the main valve, through the volume flow control and the safety sensors, to the passively controlled gaseous nitrogen supply—is now fitted in the plant housing. This means that all fittings are spatially integrated into the plant. Only a hose for gaseous nitrogen and a vacuum-insulated line for liquid nitrogen feed into the system from the outside. With the exception of hood coolers and the non-split cooling line, Rehm CoolFlow can be combined with all other options.
Cooling is controlled using the software by specifying the frequencies and volume flow rate as required: If the cooling line temperatures are too high, the operator increases the volume flow of liquid nitrogen through the coolers. Everything else is controlled by the system itself: An excess of nitrogen from the coolers is fed into the exhaust air to compensate for a shortfall from the gas network. Furthermore, the Rehm CoolFlow option has features that enable safe working. For instance, the supply of liquid nitrogen is automatically and safely stopped in case of a malfunction. Such measures address the challenges posed by nitrogen management.
In addition to the innovative CoolFlow solution, Rehm Thermal Systems offers flexible standard cooling concepts for VisionXP+. These include:
Standard cooling lines with up to four cooling modules
The standard cooling system consists of up to four individual cooling modules. These allow a precisely controlled cooling process as well as individual adjustment of the cooling gradient. The “closed loop principle” guarantees a closed atmosphere cycle. The standard cooling line consists of an active and a passive cooling module. The active cooling modules are supplied via an external water connection, using a heat exchanger. The coolers can be easily removed and cleaned at the rear of the system. The process chamber does not need to be opened to do this.
Flexible cooling with extended cooling line
For gentle cooling, an extended cooling line can be connected to the VisionXP+. This can be implemented as an extension to standard cooling zones under a nitrogen atmosphere or as a separate, downstream module in an air atmosphere for higher cooling performance for insensitive materials. Further advantages of the air-cooled variant: while nitrogen is needed in the process section of the convection unit to prevent oxidation, the extended cooling line no longer needs to be flooded with nitrogen, resulting in nitrogen savings.
Underside cooling for uniform cooling from above and below
For particularly massive or large assemblies or boards with product carriers, the VisionXP + can also be equipped with underside cooling. The actual cooling process is identical to that of the standard cooling line, but the extracted, cleaned and cooled air flows not only from above onto the module, but also from below.
Gradual cooling for energy saving
Rehm also offers an energy-saving cooling variant for the VisionXP+ convection soldering system: The air is extracted not only at one point but at two points. This results in a smoother cooling gradient and offers significant energy saving potential.
Image: Rehm Thermal Systems
About Rehm Thermal Systems
Rehm is a technology and innovation leader in the state-of-the-art, cost-effective manufacturing of electronic assembly groups. It specialises in thermal system solutions for the electronics and photovoltaics industry. Rehm is a globally active manufacturer of reflow soldering systems using convection, condensation or vacuum, drying and coating systems, functional test systems, equipment for the metallisation of solar cells and numerous customised systems. We have a presence in all key growth markets and, as a partner with 30 years of industry experience, we are able to implement innovative production solutions that set new standards.
Suggested Items
Knocking Down the Bone Pile: Addressing End-of-life Component Solderability Issues, Part 4
07/16/2025 | Nash Bell -- Column: Knocking Down the Bone PileIn 1983, the Department of Defense identified that over 40% of military electronic system failures in the field were electrical, with approximately 50% attributed to poor solder connections. Investigations revealed that plated finishes, typically nickel or tin, were porous and non-intermetallic.
SHENMAO Strengthens Semiconductor Capabilities with Acquisition of PMTC
07/10/2025 | SHENMAOSHENMAO America, Inc. has announced the acquisition of Profound Material Technology Co., Ltd. (PMTC), a premier Taiwan-based manufacturer of high-performance solder balls for semiconductor packaging.
KYZEN to Highlight Understencil and PCB Cleaners at SMTA Querétaro Expo and Tech Forum
07/09/2025 | KYZEN'KYZEN, the global leader in innovative environmentally responsible cleaning chemistries, will exhibit at the SMTA Querétaro Expo & Tech Forum, scheduled to take place Thursday, July 24, at Centro de Congresos y Teatro Metropolitano de Querétaro.
Driving Innovation: Direct Imaging vs. Conventional Exposure
07/01/2025 | Simon Khesin -- Column: Driving InnovationMy first camera used Kodak film. I even experimented with developing photos in the bathroom, though I usually dropped the film off at a Kodak center and received the prints two weeks later, only to discover that some images were out of focus or poorly framed. Today, every smartphone contains a high-quality camera capable of producing stunning images instantly.
Hands-On Demos Now Available for Apollo Seiko’s EF and AF Selective Soldering Lines
06/30/2025 | Apollo SeikoApollo Seiko, a leading innovator in soldering technology, is excited to spotlight its expanded lineup of EF and AF Series Selective Soldering Systems, now available for live demonstrations in its newly dedicated demo room.