What It Takes to Be a Milaero Supplier, Part 4
May 18, 2020 | Anaya Vardya, American Standard CircuitsEstimated reading time: 4 minutes
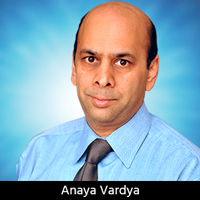
Introduction
The decision to pursue military and aerospace (milaero) certification impacts every facet of the organization, and not every shop is prepared to make this transformation. This is the final article in a four-part series, breaking down what it takes in sales and customer service, engineering and CAM, purchasing and quality, and manufacturing. In Part 4, Anaya Vardya explores what it takes to be a milaero supplier in the area of manufacturing.
Working Environment
Good business practices have always included providing employees a safe and adequate working environment. Later came the expectations to reduce stress and repetitive motion fatigue through the implementation of ergonomics. Milaero organizations must take this to another level by adding in a combination of human and physical factors, including:
- Social considerations: Non-discriminatory, calm, non-confrontational
- Psychological considerations: Stress-reducing, burnout prevention, emotionally protective
- Physical considerations: Temperature, humidity, heat, lighting, airflow, hygiene, noise
The key is that the working environment needs to be “appropriate for the organization’s product or service.” In other words, the appropriate environment for a PCB manufacturer will be much different than for a contract manufacturer or a sheet metal fabricator.
Operational Planning and Risk Management
Milaero suppliers must have a process in place to convert customer requirements into something that the plant can use to build the product. This is typically accomplished by using some form of a traveler or work order. Whatever tool is used, it must contain what’s required, as well as the sequence of processes required—such as inspection and tests and the criteria for each process and for the acceptance of products. The considerations for operational planning include:
- People and product safety
- Manufacturability and reliability
- Handling and product damage prevention
- Product obsolescence and recycling
Risk management is not a requirement for ISO 9001 but is a really big deal for milaero work—identifying potential manufacturing risk and taking steps to either mitigate the risk, as well as acknowledge and accept it. This can involve a very detailed advanced product quality planning (APQP) process before a job is released to identify any manufacturing concerns or challenges the order may present. Another common method is to employ process failure mode effects analysis (pFMEAs). Risk management is simply identifying what could go wrong in each process, and what to do about it if it does.
Equipment Validation
Commercial and ISO 9001 manufacturers typically don’t put much thought into validating a new piece of equipment; their focus is generally on getting it installed and operating as quickly as possible. Of course, much care is given to ensure proper installation and operation, but in most cases, the manufacturer would be hard-pressed to provide evidence of validation a year or two later. This is another unique requirement that often necessitates milaero manufacturers to develop a new process to address.
The good news is that this does not need to be a complicated process; usually, a simple checklist will suffice. It should include installation checks to ensure a proper environment and that electrical, air, and water sources are complete. The next set of checks ensure that any needed preventive maintenance, calibration, and work instructions have been created. The last check should validate the quality of products produced from the equipment, typically through a first article noting the part and work order numbers and quality approval.
Technology
Specific to military work, a supplier cannot just build any technology that a customer sends to them. There is a technology qualification process that is done during the initial MIL-PRF-31032 certification. This establishes a certain technology level that the milaero supplier is qualified to build. If a supplier wants to increase their approved technology level, there is a process to do this called “add-on qualification” that requires special additional testing and Defense Logistics Agency (DLA) approval.
FOD
Foreign object debris/damage (FOD) started when an airplane mechanic left a wrench in a jet engine after a repair, resulting in catastrophic engine failure. FOD has now been flowed down through the entire supply chain involved in milaero work. There is a protocol established by Boeing that most companies follow in some manner that involves 6S “clean as you go” throughout the shop, FOD inspections, and management FOD walks. Potential FOD threats include hairs, fluff, paper, water, burrs, fingerprints, slivers, grease, paint, cleaning solvents, lubricant oils, ink, dust, tacking residues, insects, food crumbs, coins, staples, and paperclips.
For the PCB industry, the most critical manifestation of FOD would be permanently entrapped debris that would be a cosmetic issue, in the best case, to conductive debris that could result in a latent failure in the field in the worst case. There are three levels of FOD areas that need to be identified in a company
1) FOD awareness areas (low risk)
- Offices
- Lunchroom
- Conference Room
2) FOD control areas (medium risk)
- Shear and materials prep
- Drill/route
- Photo
- Image
- Plating
- Lab
- Test
- Final inspection
- Microsectioning
3) FOD critical areas (high risk)
- Lamination
- LPI coat and expose
- Shipping
Conclusion
As can be seen throughout this four-part series, becoming a milaero manufacturer changes the game significantly, adding new processes and a much higher degree of complexity when dealing with milaero orders. Milaero products demand some of the most technically challenging PCBs in the industry, and in many cases, will require the expansion of your staff. Before jumping in with both feet, it is a decision that must be carefully considered.
Editor’s Note: Read Part 1, Part 2, and Part 3.
Anaya Vardya is president and CEO of American Standard Circuits. Vardya is also co-author of The Printed Circuit Designer’s Guide to… Fundamentals of RF/Microwave PCBs and Flex and Rigid-Flex Fundamentals. Visit I-007eBooks.com to download these and other free, educational titles.
Suggested Items
TT Electronics Secures £20 Million in Aerospace and Defence Contracts as European Programmes Accelerate
06/06/2025 | TT ElectronicsTT Electronics has been awarded more than £20 million in new and renewed defence contracts, marking a major step forward in its contribution to Europe’s rapidly evolving defence landscape.
Elma Electronic Bolsters Quality Management Company-wide with Added AS9100:D and ISO9001:2015 Certifications
06/02/2025 | Elma ElectronicElma Electronic now includes AS9100:D and ISO 9001:2015 certifications at its Horsham, Pa. manufacturing facility, earning the company a multiple site accreditation designation.
See TopLine’s Next Gen Braided Solder Column Technology at SPACE TECH EXPO 2025
05/28/2025 | TopLineAerospace and Defense applications in demanding environments have a solution now in TopLine’s Braided Solder Columns, which can withstand the rigors of deep space cold and cryogenic environments.
ICEFlight to Accelerate Maturation of Cryogenic Technologies for Hydrogen-Powered Flight
05/27/2025 | GKN AerospaceGKN Aerospace is one of the project partners in ICEFlight (Innovative Cryogenic Electric Flight), a project aiming to contribute to the development of hydrogen-powered flight.
Vertical Aerospace Makes Aviation History with Piloted eVTOL Flight in Open Airspace
05/27/2025 | BUSINESS WIREVertical Aerospace, a global aerospace and technology company that is pioneering electric aviation, announced it has made European aviation history with the first-ever piloted wingborne flight of a winged electric vertical take-off and landing (eVTOL) aircraft in open airspace.