HP and BASF Expand Industrial Alliance to Advance Digital Manufacturing
June 5, 2020 | Globe NewswireEstimated reading time: 3 minutes
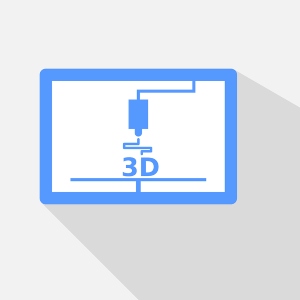
BASF, the world’s leading chemical company, and HP, the leader in industrial 3D printing solutions, today announced an expansion of their strategic alliance to advance digital manufacturing. Together, the companies are working closely with innovators in the auto, consumer, medical, and industrial manufacturing sectors to open up new market opportunities, jointly develop new best-in-class applications, and achieve unmatched quality, breakthrough economics, and more sustainable production.
At the center of the expanded collaboration is the launch of a first-of-its-kind polypropylene (PP) for additive manufacturing. The HP 3D High Reusability PP enabled by BASF was developed and qualified for HP’s Jet Fusion 5200 Series 3D printing solution to enable companies across industries to design and produce 3D printed parts faster, more cost-effectively, more sustainably, and at higher volumes than ever before.
“The advancement of our long-standing partnership with HP truly demonstrates our shared vision to help transform industries, enable sustainable production, and enable our customers to shape the Additive Manufacturing industrialization,” said François Minec, Managing Director, BASF 3D Printing Solutions. BASF 3D Printing Solutions unveiled its new Forward AM brand last year as it continues to pursue its goal of driving industrial scalability with future-oriented, leading-edge materials and technology. “The introduction of PP is another important step as we collaborate on best-in-class materials to transform manufacturing. Our teams have worked closely to develop a high quality, sophisticated PP that fully leverages the advanced capabilities of HP’s Jet Fusion 5200 platform – truly a win-win for innovative companies investing in the shift to digital manufacturing.”
“HP and Forward AM by BASF share a deep commitment to accelerating the shift to digital manufacturing by delivering innovative, sustainable solutions and materials that open up entirely new opportunities,” said Ramon Pastor, Interim President of 3D Printing and Digital Manufacturing, HP Inc. “The powerful combination of the world’s leading materials science and most advanced 3D printing capabilities yields superior quality, reliability, workflow, and cost savings for customers. From advanced prototyping to the production of final parts, we are excited about the impact this new PP will have for designers, engineers, and businesses around the world.”
BASF and HP have a long history of innovating together. BASF is a foundational partner in HP’s 3D printing materials ecosystem and the two companies have collaborated on an array of sustainable and innovative materials including ULTRASINT® TPU01 thermoplastic polyurethane released last year. Developed for HP’s Jet Fusion 5200 3D Series, the new PP enables the 100% reuse of collected surplus powder2, leading to less waste3 and more efficient production.
Already, the Forward AM team and HP are working with industry leaders including Extol, GKN Powder Metallurgy/Forecast 3D, Henkel, Oechsler, and Prototal to jointly develop applications with the new PP on HP Jet Fusion 5200 3D printing systems. Polypropylene has historically been a highly desirable material in industrial manufacturing due to its low cost, colorability, chemical resistance and UV stability, with nearly unlimited use in the world’s leading industries including consumer appliances and the $2 trillion automotive market. The availability of a new additive material that replicates a traditional material used for a wide variety of auto parts found in vehicles’ interior, exterior, and under-the-hood offers significant advantages for auto makers.
“We have been truly impressed by the joint effort between Forward AM by BASF and HP to help us accelerate our digital manufacturing initiatives,” said Matthias Weißkopf, senior vice president for research and development, Oechsler AG. “The introduction of new materials such as PP enables us to quickly and cost effectively design, iterate and produce innovative new 3D printed parts for customers across industries. We expect a fast ramp up of entirely new applications that leverage the inherent advantages that 3D printing provides for auto makers, home and commercial appliances and the medical industry.”
Suggested Items
Delta SEA Partner Event 2025 Unites Regional Partners to Embrace a “Future Ready” Vision
07/03/2025 | Delta ElectronicsDelta Electronics (Thailand) Public Company Limited, successfully hosted its Delta SEA Partner Event 2025: Future Ready at Delta Chungli Plant 5, Taiwan on June 10 – 11 , 2025.
Murray Percival Company Welcomes CeTaQ to Its Line Card, Optimizing SMT Processes for PCB Manufacturers
07/03/2025 | Murray Percival CompanyThe Murray Percival Company, a trusted supplier to the Midwest's electronics industry, is pleased to announce that it has added CeTaQ to its line card, a global expert in Surface Mount Technology (SMT) measurement systems.
RBB’s Jeff Schartiger Appointed to SMTA Ohio Board as Technical Advisor
07/03/2025 | RBBRBB, a trusted leader in electronics manufacturing since 1973, is proud to announce that Jeff Schartiger, Operations Manager at RBB, has been appointed to the SMTA Ohio Chapter Board as a Technical Advisor.
Kitron Receives EUR 4 Million Contract for Defense Airborne Radar Application
07/02/2025 | KitronKitron has received an order valued at EUR 4 million to produce electronics modules for airborne radar application, destined for the US market.
Zollner Completes Full Acquisition of Bluechips Microhouse
07/01/2025 | Zollner Elektronik AGZollner Elektronik AG has successfully finalized its complete takeover of Bluechips Microhouse Co., Ltd., in Thailand. In the future the company will operate as part of the Zollner Group of companies under the leadership of Thomas Kiefl—strategically networked, technologically focused and internationally oriented.