BAE Systems' Factory of the Future
July 13, 2020 | BAE SystemsEstimated reading time: 2 minutes
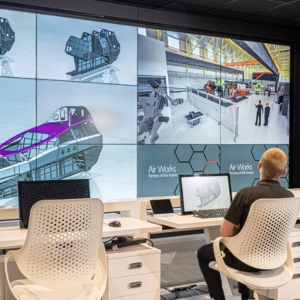
A first-of-its-kind industry 4.0 factory is applying game-changing digital technologies to advance manufacturing on the UK’s next generation combat aircraft system, Tempest.
The new facility at BAE Systems’ site in Warton, Lancashire, is the result of a multi-million pound investment and collaboration with more than 40 blue chip and SME companies along with academic institutions. Harnessing the best of UK innovation, the Company has developed a digitally connected, intelligent factory for future military aircraft production.
Bringing together advanced manufacturing technologies, the factory will transform engineering processes. Automated robots, virtual and augmented reality will increase speed, precision and efficiencies, as well as reduce the costs associated with the manufacture of complex military aircraft structures.
The factory also demonstrates a new approach to the way humans and machines can operate together. Cobotic and flexible robotic technologies remove the need for heavy, fixed, long-lead tooling and can quickly switch from the manufacture of one item or platform to another. Intelligent machines and off-the-shelf robotic technology from the automotive industry have been modified to operate at the precise tolerances required for military aircraft, which are less than a third the width of a human hair on some of our programmes.
Such technology drives greater productivity by allowing operators to focus on more highly-skilled and strategic tasks and production managers to oversee operations from a fully digitised, virtual office.
The new facility underpins efforts of the UK-led Tempest programme to meet the UK’s ambition to remain at the forefront of the Combat Air sector by delivering more cost-effectively and in half the time of previous programmes.
Dave Holmes, Manufacturing Director for BAE Systems Air, said:
“We’ve collaborated with the best of UK industry and academia to develop a cutting-edge facility that combines current and emerging technologies, ensuring the UK remains at the forefront of combat air technology development.
“Driving our manufacturing capabilities forward as we prepare for the fourth Industrial Revolution, will sustain and develop critical skillsets and ensure we can continue to deliver military capability to address future threats, whilst improving productivity and delivering value for money for our customers.”
Technologies inside the factory are already delivering benefits. The intelligent workstation, developed in collaboration with The University of Sheffield’s Advanced Manufacturing Research Centre (AMRC) and Fairfield Control Systems, is in use on the Typhoon production line. It uses a system which recognises operators and automatically delivers tailored instructions using ‘pick by light’ technologies. In addition, additive manufacturing technologies are being used in the production of Typhoon aircraft parts and assemblies.
Suggested Items
Delta SEA Partner Event 2025 Unites Regional Partners to Embrace a “Future Ready” Vision
07/03/2025 | Delta ElectronicsDelta Electronics (Thailand) Public Company Limited, successfully hosted its Delta SEA Partner Event 2025: Future Ready at Delta Chungli Plant 5, Taiwan on June 10 – 11 , 2025.
Murray Percival Company Welcomes CeTaQ to Its Line Card, Optimizing SMT Processes for PCB Manufacturers
07/03/2025 | Murray Percival CompanyThe Murray Percival Company, a trusted supplier to the Midwest's electronics industry, is pleased to announce that it has added CeTaQ to its line card, a global expert in Surface Mount Technology (SMT) measurement systems.
RBB’s Jeff Schartiger Appointed to SMTA Ohio Board as Technical Advisor
07/03/2025 | RBBRBB, a trusted leader in electronics manufacturing since 1973, is proud to announce that Jeff Schartiger, Operations Manager at RBB, has been appointed to the SMTA Ohio Chapter Board as a Technical Advisor.
Kitron Receives EUR 4 Million Contract for Defense Airborne Radar Application
07/02/2025 | KitronKitron has received an order valued at EUR 4 million to produce electronics modules for airborne radar application, destined for the US market.
Zollner Completes Full Acquisition of Bluechips Microhouse
07/01/2025 | Zollner Elektronik AGZollner Elektronik AG has successfully finalized its complete takeover of Bluechips Microhouse Co., Ltd., in Thailand. In the future the company will operate as part of the Zollner Group of companies under the leadership of Thomas Kiefl—strategically networked, technologically focused and internationally oriented.