-
- News
- Books
Featured Books
- smt007 Magazine
Latest Issues
Current IssueSpotlight on India
We invite you on a virtual tour of India’s thriving ecosystem, guided by the Global Electronics Association’s India office staff, who share their insights into the region’s growth and opportunities.
Supply Chain Strategies
A successful brand is built on strong customer relationships—anchored by a well-orchestrated supply chain at its core. This month, we look at how managing your supply chain directly influences customer perception.
What's Your Sweet Spot?
Are you in a niche that’s growing or shrinking? Is it time to reassess and refocus? We spotlight companies thriving by redefining or reinforcing their niche. What are their insights?
- Articles
- Columns
- Links
- Media kit
||| MENU - smt007 Magazine
Estimated reading time: 5 minutes
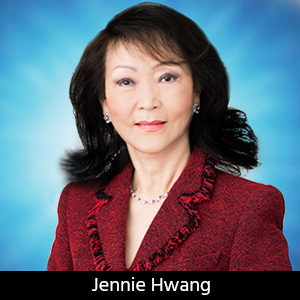
SMT Perspectives and Prospects: Joint Industry Standard IPC J-STD-006—Electronic Solder Alloys
It has been nearly two decades since the global electronics industry adopted lead-free conversion from leaded electronics. Readers who have been in the industry during this period will recognize the changes and challenges the industry has faced and appreciate the fact that taking the element lead (Pb) out of electronics has not been a straightforward path. Right at the outset, in my view, four questions should have been addressed:
- Which solder alloy could be widely accepted?
- Which alloy(s) could be regarded as working alloys?
- Which alloy(s) is (are) merited with high-reliability performance under harsh environments?
- Could the former three questions necessarily be causing mutual exclusivity?
In this column, I will confine my comments to the milestones, key events/activities, and thought processes, to some extent, of IPC Joint Industry Standard J-STD-006: “Requirements for Electronic-Grade Solder Alloys and Fluxed and Non-Fluxed Solid Solders for Electronic Soldering Applications.”
J-STD-006 primarily focuses on solder alloys and is generally deemed mundane—certainly not glamourous. However, solder alloy is critical to electronics, performing a critical function as the interconnecting material for electrical, thermal, and physical connections as well as other surface coating functions. To reiterate my two snippet statements over the years:
- “Solder joint cannot perform better than the solder alloy is intrinsically able to deliver,” summarizing the inseparability of a solder alloy and a solder joint that is made of a specific solder alloy.
- “When/if one single solder joint in an electronic system fails, the whole electronic system, regardless of the level of design sophistication or functional complexity, fails,” summarizing the critical role of solder joint in electronics.
Accordingly, J-STD-006 has been playing a pivotal role in serving the industry’s needs and wants, particularly during the transitional period from the leaded world to lead-free and onward.
Serving as the chairman of the standard over the years, I have been privileged to personally work with both users and suppliers of solder alloys to enhance communication and facilitate solving prevalent issues in a timely manner. Our goal has always been to find the best solution when an issue arises and to reach consensus when different positions exist. Throughout the years, in our communications and discussions, whether in-person or via air waves, our task group always follows the principles of standardization from the American National Standard Institute (ANSI) and IPC.
These principles include how standards should show a relationship to design for manufacturability (DFM) and design for the environment (DFE), minimize time to market, contain simple language, focus on end-product performance, and include a feedback system on use and problems for future improvement. Principles also: include—rather than inhibit—innovation; do not keep people out, and; do not contain information that cannot be defended with data. The standard should include specification information—it should not tell you how to make something. In a nutshell, it is worthwhile being reminded that the standard is a specification—not a know-how document.
With these items in mind—for the benefit of readers who have not been participants in our task group, and for the interest of paving the future path of current and future participants—I share a few highlights of J-STD-006, in both retrospective and prospective perspectives, that might be helpful.
What Has Been Accomplished
First and foremost, we thank our task group members who have worked patiently and relentlessly to move the J-STD-006 forward and upward over the years. J-STD-006 has moved (improved) from J-STD-006 to J-STD-006A version (May 2001), and to J-STD-006 B (January 2006) and J-STD-006B with Amendments 1 and 2 (October 2009), further to J-STD-006C (July 2013) and J-STD 006C with Amendment 1 (October 2017). For the recent years since the lead-free transition period, key milestones include:
- J-STD-006A was revised to J-STD-006B. The Revision J-STD-006B, published in January 2006, essentially was to “introduce” lead-free alloys (i.e., Table A-1)
- In October 2009, Amendments 1 and 2 to J-STD-006B were introduced to include proper notes for tables
- In 2011, our task group’s focus was to harmonize the alloy designation or naming system. Efforts were directed to elect a logical system that is also practical to our industry’s use. Several options have been considered. For instance, the order of the metallic elements in an alloy designation can be predicated on the rules of academic/metallurgy (e.g., AgAuBiCuInNiSbSn) or custom and convenience (e.g., SnAgAuBiCuInNiSb)
- J-STD-006C was born in July 2013 to adopt the naming system of our choice and the conversion of all alloy designations in accordance with the naming
system of choice - Amendment 1 to J-STD 006C was published in October 2017 to incorporate new alloy listings, the statements regarding rare earth elements, and the expansion of control ranges of nominal compositions
Solder Alloy Inclusion in the Standard
Requirements to list a solder alloy in the J-STD-006 include:
- All elements, including dopants, shall be disclosed
- All elemental dosages, including dopants, shall be provided
- Analytical methods to identify and confirm the presence and quantity shall be provided
It should be noted that all elements herein refer to all intentionally introduced elements or included in the manufacturing process of an alloy composition for a purpose, use or expected function, rare earth or otherwise (e.g., La, Ce, Nd, Mn, Ge, etc.) regardless of dosage (e.g., 88 wt% or 0.01 wt%); that is, elements in an alloy composition that are not introduced by design are impurities.
Upcoming Challenges
In our recent past meetings, I have challenged the task group to address four questions:
- How can we make J-STD-006 document more useful, more complete, more informative, and more practical to the industry (i.e., suppliers, users, or any interested party)?
- Which area(s) should be added?
- Which area(s) should be expanded?
- What are the priorities?
To this end, one of the recurring issues that was brought up in our task group meetings is dopant vs. impurities. As more new alloys are being developed with intentionally added dopant(s)
in a small weight percentage, J-STD-006 bears the responsibility to provide a guide.
Framework Efforts on Dopants vs. Impurities
Updating solder alloy impurities remains a challenge. Differentiating dopants from impurities drives another level of effort. I have laid out the skeletal framework that is to be considered in three distinct categories of elements.
1. Current impurities elements (Table 3-2).
- E.g., Ag, Cd, Pb, Al, Cu, Sn, As, Fe, Zn, Au, In, Sb, Bi, Ni
2. Additional elements to be considered.
- E.g., Phosphorus (P), sulfur (S), others
- It is worth noting that QQ-S-571F (Federal specification: solder, electronic) limits P at 0.010 wt% and S at 0.005 wt%, but J-STD-006 makes no call on these two elements, which could potentially affect the properties and behavior of a solder alloy
3. Dopants being used in alloys that are listed in the current impurity table.
- E.g., Ni, others
To move forward to the next stage of development of J-STD-006, the issue is requested to be addressed. This will be a daunting task, demanding substantial efforts and affecting suppliers, users, and the industry overall.
This column originally appeared in the January 2020 issue of SMT007 Magazine
More Columns from SMT Perspectives and Prospects
SMT Perspectives and Prospects: Warren Buffett’s Perpetual Wisdom, Part 2SMT Perspectives and Prospects: Warren Buffett’s Perpetual Wisdom, Part 1
SMT Perspectives and Prospects: Artificial Intelligence, Part 5: Brain, Mind, Intelligence
SMT Perspectives and Prospects: Artificial Intelligence, Part 4—Prompt Engineering
SMT Perspectives and Prospects: The AI Era, Part 3: LLMs, SLMs, and Foundation Models
SMT Perspectives and Prospects: A Dose of Wisdom
SMT Prospects and Perspectives: AI Opportunities, Challenges, and Possibilities, Part 1
SMT Perspectives and Prospects: Critical Materials—A Compelling Case, Part 3