-
- News
- Books
Featured Books
- smt007 Magazine
Latest Issues
Current IssueSpotlight on India
We invite you on a virtual tour of India’s thriving ecosystem, guided by the Global Electronics Association’s India office staff, who share their insights into the region’s growth and opportunities.
Supply Chain Strategies
A successful brand is built on strong customer relationships—anchored by a well-orchestrated supply chain at its core. This month, we look at how managing your supply chain directly influences customer perception.
What's Your Sweet Spot?
Are you in a niche that’s growing or shrinking? Is it time to reassess and refocus? We spotlight companies thriving by redefining or reinforcing their niche. What are their insights?
- Articles
- Columns
- Links
- Media kit
||| MENU - smt007 Magazine
Estimated reading time: 10 minutes
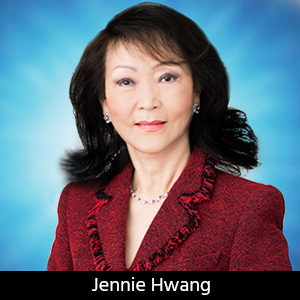
SMT Perspectives and Prospects: Rethinking Manufacturing–Bracing for and Embracing a Post-Pandemic Decade
From a 30,000-foot view, global macroeconomics is facing gusty headwinds, bracing for impact from social-distancing lockdowns and economic shutdowns across the globe as a result of the coronavirus pandemic. Compounding to the pandemic, the world’s two largest economies—the U.S. and China—are butting heads on trade and geopolitical affairs.
Additionally, at the time of this writing, the lawless riots in the midst of the protests for social justice, spreading from coast to coast in the U.S., are destroying properties and businesses in metropolitan areas, aggravating the already-disrupted businesses and adding to the financial losses as the result of the pandemic. The triple whammy of concurrent events puts the country in an unprecedented challenge economically, socially, and politically.
Against this potent backdrop, how should our industry respond? How should we manage and rethink manufacturing? And what are the main issues at hand in near-term and long-term horizons?
COVID-19 has cost lives and caused sorrow and distress. Our hearts go out to all who are in grief. However, the pandemic has propelled our deeper thoughts and made us venture into the wide landscape of the mind. We will have a new normal in business and manufacturing, just as in our daily lives. One old saying states, “Never let a crisis go to waste.” What have we learned from the coronavirus crisis to benefit our future endeavors?
Three tangible areas in business and manufacturing are directly impacted by these concurrent forces: business strategy in manufacturing, supply chain strategy and management, and manufacturing operation practice, including the workforce.
Business Strategy: Re-Evaluate Outsourcing
For manufacturers, the first order of business is to strategize the business model, assessing outsourcing, or not outsourcing. Over the last three decades, the electronics industry has been characterized by its fast-paced technological development, inevitable down-spiral pricing, and market globalization. These also have been the top drivers behind manufacturing outsourcing. The underlying concept of outsourcing can be expressed—simply put—as finding a better or more cost-effective way to have products made or services rendered, meanwhile freeing up the resources and time for “essential” or more critical tasks[1].
The history of outsourcing in the U.S. is worth noting. It is a reasonably fair statement to say that the electronics industry’s circuit board manufacturing essentially pioneered the process to implement a full-blown outsourcing strategy in the late 1980s and early 1990s (depending on how we define a starting point). Gradually but steadily, manufacturing outsourcing within the electronics industry has extended upstream from the board assembly level (semiconductor packaging, integrated circuits foundry) and downstream (system, box) along the food chain. This created a new market and business sector, which originally was termed as contract manufacturing (CM) and later evolved to electronic manufacturing ?services (EMS), which is deemed to be a more appropriate representation for its expanded services.
It is interesting to note that this fast-growing industry was not noticed by Wall Street until the mid-1990s (passing $100 billion mark in 1999). Today, the same concept of manufacturing outsourcing has spilled over to other industries ranging from pharmaceutical to consumer staples, as well as to other functions, such as human resources and information technology management. In parallel, the scope of outsourcing continues expanding and its capabilities are proliferating, becoming an integral part of supply chain management.
When looking at the potential pros and cons of outsourcing, manufacturing outsourcing can potentially offer a number of advantages covering various business aspects, namely:
- Economics and cost savings
- Improvement in business focus
- Operational efficiency
- Technological prowess
- Capital allocation
- Time-to-volume
- Time-to market
- Geographical advantage
- Proximity to customers
- Shared risk or transferred risk down the food chain
- Streamlining the complexity of business ?
As an aggregate, these potential advantages offer tremendous appeal to a business, particularly in meeting the immediate competitive needs. The benefits can be vividly evident when a goal-oriented and well-thought-out strategy is effectively executed.
On the flip side, caution and alerts are in order. With the establishment of EMS, does this mean that technology-based companies can forgo core engineering competencies, including manufacturing technology?
It is always a strategic decision to take advantage of the benefits of outsourcing without losing the fundamental knowledge and know-how. The critical thought-process goes to assess core competencies and to sort out the functions or products for outsourcing from those that need to stay in-house. Even after a product or a function is identified to be outsourced, it takes engineering competencies to pose the “right” questions to select the right EMS provider to produce quality products as intended.
In essence, outsourcing a non-value-added task is one thing, but to give up the critical knowledge base is entirely another. Overall, outsourcing should be dealt with as a well-planned strategy, not as a relief tactic. And the outsourcing strategy should be discerned between the temporary lift and long-term business enhancement.
Recalling years ago, during a dinner meeting with Dr. Kazuo Inamura—the founder and chairman of Kyocera Corporation—I queried directly his view on outsourcing manufacturing. He replied just as point-blank, in paraphrasing, “How can an engineer not do manufacturing, and how can an engineering company not produce products?” He made his point, and I understood his sentiment.
Considering a product development cycle, from an innovative concept to technology development, to manufacturing the product, to introducing the product to the marketplace, each of the key milestones is pivotal to a product’s eventual success. The spirit and the principle of manufacturing are a part of a product and should be thoroughly embraced and comprehended with or without employing an outsourcing operation.
Under today’s competitive climate and with appropriate business justification, to outsource certain functions could be advantageous and constitute a smart business move. I have witnessed—and been actively engaged in with joy—the phenomenal development of the EMS operations ranging from the fledgling operation to the robust enterprises across three continents. EMS operations continue to have my genuine good wishes. However, it is prudent for OEMs or ODMs to maintain and acquire the engineering strength and know-how to prepare for future readiness.
Supply Chain Management
During this pandemic period, it is encouraging to note that the Institute for Supply Management’s manufacturing index for the month of May rose to 43.1% from an 11-year low ?of 41.5% in April, indicating that the pace of deterioration slowed as governments eased coronavirus-related restrictions[2]. What have we learned from the coronavirus crisis?
Inventory and supply chain management will have heightened importance and priority to manufacturing efficiency and even to a manufacturer’s viability. Crucial questions to be addressed include:
- Is a reliable dependency on the chain of suppliers in place?
- What is the technology employed to monitor the chain of supply?
- Is a risk management program in place?
- What is the risk mitigation plan and its order of priority?
- Are the policies and procedures to address risks and threats in place?
- Do all strategic raw materials have an alternate source(s), if justified?
- Do all mission-critical components have alternate source(s), if justified?
- What is the level of visibility throughout the supply chain?
- What is the predictability of the supply chain?
- Is there an adequate system in place to ensure internal and external cybersecurity to reduce manufacturing supply chain cybersecurity risks? ?
Weighing the overseas sources juxtaposing with the domestic sources in quality, cost, delivery time, and in-time-availability becomes a strategic as well as an operating issue. Implementing the newly available technologies to minimize the risk and optimize the efficiency of supply chain management is also increasingly becoming a necessity.
Manufacturing Environment and Operation: Technology-Propelled and Data-Driven ?Assuming there is a reasonable likelihood that we and coronavirus may co-exist for an indefinite period of time, and considering that social-distancing practices will continue, a near-term and long-term plan should be formulated and implemented with the goals to ensure workers’ safety and health while maximizing workplace productivity and optimizing manufacturing efficiency.
COVID-19 catalyzed remote work, and the required social-distancing has prompted the need for more sophisticated ways to monitor factory operations, including the deployment of data management and analytics in a “further and faster” manner.
One of today’s deficiencies in deploying the leading technologies as effective tools, such as AI, is the lack of a relevant and sufficient database. AI requires a vast amount of data to function as desired. Accordingly, preparing AI to facilitate manufacturing operations by initiating a “data” program to collect, clean, manage, and use the data is also increasingly important. Data tells the story!
Data capabilities as tools to remotely monitor factories, provide a clearer view of operations, equipment performance and maintenance, allowing the operation to speed up production, reduce waste, and avoid downtime by quickly identifying maintenance and production issues. By identifying and extracting relevant data sets to feed into artificial intelligence, we will gain the ability to predict production and supply-chain problems. With the use of AI, factories are able to go from reactive analytics, reporting on what happened, to proactively analyzing what might happen, and the suggested actions to take.
The better we are at leveraging the emerging technologies (AI in conjunction with IoT and 5G) to enable a real-time contextual understanding and the monitoring of the manufacturing operation and environment, the smarter decisions we are able to make[3].
Manufacturing Workforce
?Unlike other industry sectors, manufacturing takes the physical presence of skilled and well-trained workers. However, some functions can be performed in remote work (or work-from-home). One of the advantages of remote work is removing the geographical barriers in hiring and allowing employers to seek the best skilled workers regardless of where that talent resides. A recent survey by IBM Institute for Business Value found that more than 75% of respondents would like to continue working remotely at least occasionally, while more than half want it to be their primary way of working after the coronavirus crisis ends[4]. When asked what it is about remote work that has worked well, according to the Wall Street Journal, the top three on the list were: no commute, reduced meetings, and fewer distractions[5].
It is expected that the development and deployment of emerging technologies will accelerate. As 5G is becoming more available and more reliable for advanced connectivity, innovations in how we work to achieve the maximum efficiency and output—including work-from-home—will become a part of the workforce in a “proper” extent. Going forward, a hybrid work model is most likely to be implemented throughout the companies and organizations, varying in extent with different natures of the business.
In the next decade, having a skilled and educated workforce, as well as continuing education and training programs—especially in data science and data engineering—will be even more important to competitive manufacturing operation.
To cope with the new world, it is plausible to address additional business decisions, including:
- Are factories logically, strategically, and preemptively distributed in terms of geographical locations?
- Is there a need for redundancy in factories?
- What criteria are to be established for making redundancy of factories?
- What are the key tasks to accelerate the adoption of new technologies—that is, to effectively and timely leverage AI, IoT, 5G, and associated infrastructure and supply chain to achieve the intelligence-teaming manufacturing operating in an integrated manner? ?
With its constantly changing and fast-paced nature, there is no industry quite like the electronics industry, with its technology, operation, and promise. For the last three decades, this most innovative and dynamic industry has made many companies and individuals prosperous. Also, as vividly demonstrated, change and coping with change have been a part of our being. The industry’s ability to adapt to change rapidly has been utterly stunning in the past. And I believe, wholeheartedly, that this ability will continue, as we overcome the compounded challenges of the pandemic, the economic recovery path, and the ongoing U.S.-China trade uncertainty.
There is a rainbow after the storm. The beauty of these crisis experiences is that we are in the position to build a better normal, so let’s brace for the challenges and embrace the opportunities!
References
1. J.S. Hwang, “Outsourcing Manufacturing or Not, and to What Extent?” The SMT Magazine, April 2003.
2. Institute for Supply Management, “May 2020 Manufacturing ISM Report on Business,” June 1, 2020.
3. J.S. Hwang, “Smart Factory Implementation: How Smart Is Smart Enough?” SMT007 Magazine, April 2020.
4. IBM, “IBM Study: COVID-19 Is Significantly Altering U.S. Consumer Behavior and Plans Post-Crisis,” May 1, 2020.
5. H. Torry, “As Coronavirus Lockdown Rules Ease, Some Want to Keep Working From Home,” Wall Street Journal, May 27, 2020.
This column originally appeared in the July 2020 issue of SMT007 Magazine.
More Columns from SMT Perspectives and Prospects
SMT Perspectives and Prospects: Warren Buffett’s Perpetual Wisdom, Part 2SMT Perspectives and Prospects: Warren Buffett’s Perpetual Wisdom, Part 1
SMT Perspectives and Prospects: Artificial Intelligence, Part 5: Brain, Mind, Intelligence
SMT Perspectives and Prospects: Artificial Intelligence, Part 4—Prompt Engineering
SMT Perspectives and Prospects: The AI Era, Part 3: LLMs, SLMs, and Foundation Models
SMT Perspectives and Prospects: A Dose of Wisdom
SMT Prospects and Perspectives: AI Opportunities, Challenges, and Possibilities, Part 1
SMT Perspectives and Prospects: Critical Materials—A Compelling Case, Part 3