-
- News
- Books
Featured Books
- pcb007 Magazine
Latest Issues
Current IssueThe Hole Truth: Via Integrity in an HDI World
From the drilled hole to registration across multiple sequential lamination cycles, to the quality of your copper plating, via reliability in an HDI world is becoming an ever-greater challenge. This month we look at “The Hole Truth,” from creating the “perfect” via to how you can assure via quality and reliability, the first time, every time.
In Pursuit of Perfection: Defect Reduction
For bare PCB board fabrication, defect reduction is a critical aspect of a company's bottom line profitability. In this issue, we examine how imaging, etching, and plating processes can provide information and insight into reducing defects and increasing yields.
Voices of the Industry
We take the pulse of the PCB industry by sharing insights from leading fabricators and suppliers in this month's issue. We've gathered their thoughts on the new U.S. administration, spending, the war in Ukraine, and their most pressing needs. It’s an eye-opening and enlightening look behind the curtain.
- Articles
- Columns
- Links
- Media kit
||| MENU - pcb007 Magazine
Rethinking Captive Manufacturing
July 30, 2020 | I-Connect007 Editorial TeamEstimated reading time: 3 minutes
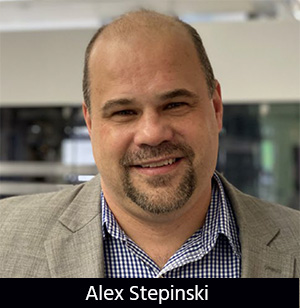
Alex Stepinski and Whelen Engineering caught everyone’s attention a few years ago when they opted to make their own PCBs in an innovative captive facility: GreenSource Fabrication. Now, with the recent purchase of an equipment manufacturer, Alex is helping to design whole factory solutions for OEMs who are interested in bringing PCB fabrication in-house.
Barry Matties: Alex, why don’t you give us your take on what’s going on with the mindset from captive facilities?
Alex Stepinski: Everybody probably knows our story, so I won’t rehash it, but we were kind of the prototype. And the reason Whelen did it was that our visionary COO at the time thought there would be a better way; there was, and we did it. But now we have this case study in North America with Whelen and GreenSource, and other people are looking at us. I see a lot of interest from folks in doing something similar, and this is driven primarily by people who can’t find a fit for their product in the market.
Job shops are jacks-of-all-trades and masters of none, and they have to set up a shop that handles a lot of different customers, in most cases, to provide some safety and diversity to their business. There are some that specialize in broad categories, like flex or microwave. But generally, you see this in Asia more than in the U.S. In the U.S., people tend to do a lot of different things because there’s not enough business.
The OEMs in the U.S. market have a tough time finding a fit because they have a lot of specialty products, and there’s hardly anybody that’s a good fit. In Asia, you can find a better fit, but there are a lot of OEMs that don’t have enough volume to get their attention. Everybody is at the mercy of the supply chain. Having your own captive fab gives you control of your capacity and priority. You get 100% of the attention because you control it. And if you wanted to, you could customize this fab for your product design philosophy and get a lot of efficiencies out of that. That’s what we did here, and now that we’ve taken the next step, we’ve become a job shop to some extent. We’re doing third-party work primarily for the defense and aerospace sector, focusing on technologies that weren’t historically represented in the U.S.
We’re doing a lot of semi-additive processing work for different applications. We’re doing high-stack microvias with very good reliability. This was also something lacking in the U.S. market. We brought this over here, and with these capabilities, we got interest from OEMs. “How do I get something like this for myself? How do I use you as a third party?” We’ve also had interest where OEMs asked us to take advantage of the equipment company we bought and offer them a whole factory solution.
We have a couple of projects where we’re designing factories for OEMs—one on the East Coast, and one on the West Coast—and then a couple that we’re having preliminary discussions with right now. This seems to be a nice niche that no one is covering right now. You could go to an OEM and say, “I can give you a factory customized to your products. It’s a 21st century mindset. It’s green, automated, and flexible. You can run rigid, flex, and backplanes in the same line. It’s a holistic approach to things.” There’s a lot of interest in this, so we’re moving our equipment business to focus on this market.
To read this entire interview, which appeared in the July 2020 issue of PCB007 Magazine, click here.
Suggested Items
Moog Announces Acquisition of COTSWORKS
07/07/2025 | BUSINESS WIREMoog Inc., a worldwide designer, manufacturer and systems integrator of high-performance precision motion and fluid controls and control systems, announced the acquisition of COTSWORKS Inc., an aerospace and defense fiber optics transceiver component manufacturer, for a purchase price of $63 million.
S&K Aerospace Awarded Major Contract Under DLA Maritime Acquisition Advancement Program
07/02/2025 | BUSINESS WIRES&K Aerospace, LLC has been awarded a significant contract under the Defense Logistics Agency’s (DLA) Maritime Acquisition Advancement Program, managed by the U.S. Naval Supply Command - Weapon Systems Support (NAVSUP WSS) in Mechanicsburg, PA.
Green Circuits to Exhibit Full-Service Electronics Manufacturing Solutions at 2025 SMD Symposium
07/02/2025 | Green CircuitsGreen Circuits, a full-service Electronics Manufacturing Services (EMS) partner to leading OEMs, is pleased to announce its participation in the 2025 SMD Symposium, taking place August 5-7 at the Von Braun Center in Huntsville, Alabama.
I-Connect007 Editor’s Choice: Five Must-Reads for the Week
06/27/2025 | Nolan Johnson, I-Connect007While news outside our industry keeps our attention occupied, the big news inside the industry is the rechristening of IPC as the Global Electronics Association. My must-reads begins with Marcy LaRont’s exclusive and informative interview with Dr. John Mitchell, president and CEO of the Global Electronics Association. For designers, have we finally reached the point in time where autorouters will fulfill their potential?
Knocking Down the Bone Pile: Tin Whisker Mitigation in Aerospace Applications, Part 3
06/25/2025 | Nash Bell -- Column: Knocking Down the Bone PileTin whiskers are slender, hair-like metallic growths that can develop on the surface of tin-plated electronic components. Typically measuring a few micrometers in diameter and growing several millimeters in length, they form through an electrochemical process influenced by environmental factors such as temperature variations, mechanical or compressive stress, and the aging of solder alloys.